Plastic injection molding is a complex process that requires precision, expertise, and attention to detail. From material selection to tool design, every aspect of the process must be carefully considered and optimized to ensure high-quality, defect-free parts. However, even the most well-designed processes can encounter issues, andhow to solve the problem? In this article Louise will explore some common process troubleshooting techniques in plastic injection molding, providing insights and practical tips to help you identify and resolve issues in your injection molding processes. #injectionmolding #mold #sino-moldIndustrial
Some injection molding defects may be very difficult to address. These defects can arise from various factors, including the molding process, the materials utilized, the maintenance of the equipment, or the storage conditions of the components. Here are several injection molding defects, causes, and solutions.
Type 1: Problems caused by Molding Process
Some injection molding processes may not be effective for the production. The molding process is the leading cause of defects in injection molding parts.
1. Blister
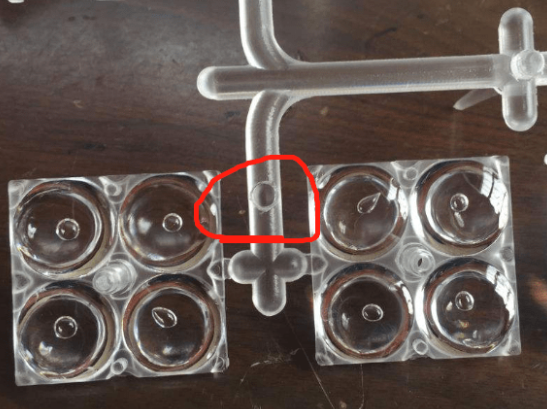
Blisters refer to raised bumps or defects on the surface of a molded part. This problem can be caused by various factors such as issues with the mold used to create the part, the materials used in the injection process, and the specific injection process itself. Specifically, blisters are caused by trapped gas near the outer layer of the part that cannot be released through normal venting methods. These factors can all contribute to the development of blisters on molded parts.
Causes:
Process parameters(cycle time too short or injection speed to high);
Insufficient cooling time;
Material is not dry enough;
Mold temperature is not suitable;
Insufficient venting
Solutions:
Adjust the injection speed to reduce the amount of trapped gas in the mold, so it can prevent the formation of blisters.
Increase the mold temperature to improve material flow and reduce the risk of blistering.
Adjust the venting to prevent the buildup of trapped gas so that vents are appropriately sized, placed, and maintained.
Modify the material to adjust the moisture content, or adding additives.
Modify the mold design to improve cooling or alter the gate location.
Inspect the mold and machine to identify any issues that may be contributing to blistering.
2. Flow Lines
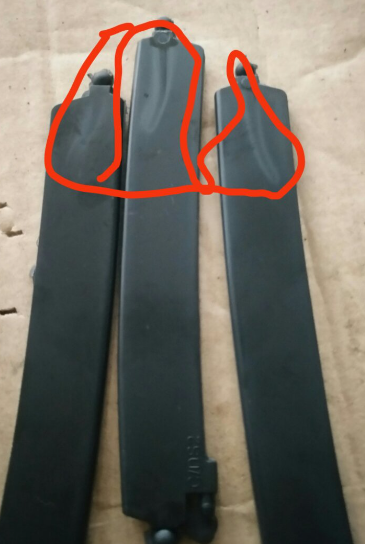
Flow lines are patterns or lines on the surface of a plastic part that are caused by the merging of multiple flow fronts during the injection molding process. They can reduce the aesthetic quality of the part and may also negatively affect its strength and performance. Flow lines usually occur at the intersection or branching points of the plastic flow path, where there may be unevenness or differences in the speed of the plastic flow.
Causes:
poor mold design;
excessively high or low melt temperatures;
uneven or insufficient injection speeds;
The small size of the gate and flow channel;
Variation in the material’s cooling speed as it flows in different directions.
Solutions:
Improving mold design and optimizing the plastic flow path to reduce the number and size of branching and intersection points.
Increase nozzle diameter.
Adjusting injection molding process parameters, such as melt temperature, injection speed, and pressure, to optimize plastic flow uniformity and speed.
Optimizing the heating and cooling system of the mold to ensure even temperature distribution on the mold surface, and avoid heat accumulation or insufficient cooling.
Using high-quality plastic materials to avoid impurities and particles that could affect flow performance.
Performing regular maintenance and cleaning of the mold and injection molding equipment during production to ensure they are operating properly and maintained in optimal condition.
3. Sink Marks
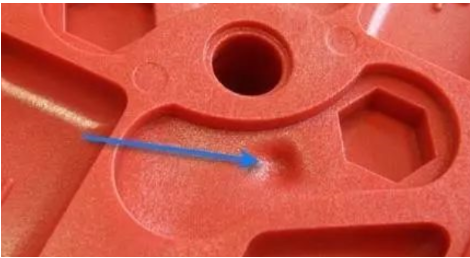
Sink marks are depressions or indentations on the surface of an injection-molded part that is caused by variations in the cooling rate of the plastic material. These variations can result in uneven shrinkage and warpage of the part, leading to localized areas of surface depression. Sink marks can occur in thick sections of the part where the cooling rate is slower, and are more likely to occur when using materials with high levels of filler or reinforcement.
Causes:
mold temperature is not properly optimized(Too short cooling or holding time and pressure);
injection pressure wrong or very low holding pressure;
high melting or molding temperatures;
Improper structural design of the molded component.
Solutions:
Design the part with a uniform thickness to promote even cooling and minimize differential shrinkage.
Modify the part design to eliminate areas of high-stress concentration or wall thickness variation.
Optimize the injection molding process parameters, such as mold temperature, injection speed, and pressure, to ensure even cooling and minimize differential shrinkage.
Use plastic materials with lower levels of filler or reinforcement, or use materials with special additives to improve cooling and minimize sink marks.
Modify the mold design to improve cooling efficiency, such as by adding cooling channels or conformal cooling features.
Perform post-molding operations, such as annealing or stress relief, to reduce the residual stresses that contribute to sink marks.
4. Weld Lines

Weld lines, also known as knit lines, are areas of an injection-molded part where two or more molten plastic flow fronts converge, resulting in a visible line or seam on the surface of the part. These lines can occur when the molten plastic flow fronts cool and solidify at different rates, creating a visible seam or weakened area. Weld lines can occur in areas of the part where the plastic flow fronts meet, such as in the center of a part or at the intersection of multiple flow paths.
Causes:
Uneven wall thickness. (plastic material is reinforced with fillers or fibers that interfere with the flow of the molten plastic)
A too-low or too-high temperature of molten material.
Inserts, holes, and multi-gate features on fabricated parts.
Solutions:
Optimize the plastic flow path and minimize the occurrence of weld lines.
Modifying the part design to eliminate areas of high-stress concentration or areas where the flow fronts converge.
Adjusting the injection molding process parameters, such as melt temperature, injection speed, and pressure, to optimize the plastic flow and minimize the occurrence of weld lines.
Using plastic materials with lower viscosity or using materials with special additives that improve plastic flow and minimize the occurrence of weld lines.
Improve the cooling efficiency, such as by adding cooling channels or conformal cooling features.
Performing post-molding operations, such as annealing or stress relief, to reduce the residual stresses that contribute to the formation of weld lines.
5. Burn Marks
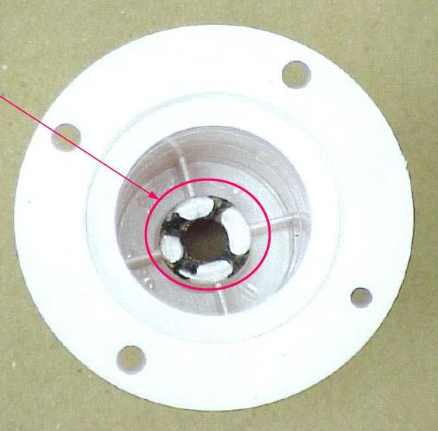
Burn marks are discolorations or black or brown spots on the surface of an injection-molded part caused by excessive heat during the molding process. These marks can negatively affect the aesthetic quality of the part and may also weaken the material, reducing its strength and performance.
Causes:
The plastic material is exposed to excessively high temperatures or prolonged heat exposure, leading to thermal degradation and the release of gases that cause discoloration or burning.
Insufficient ventilation in the mold leads to trapped air pockets that can become superheated and cause burn marks.
Slowly removing the air in the cavity;
The melting temperature is too high;
Tast screw or excessive injection speeds are too high.
The runner system’s design is improper.
Solutions:
Adjusting mold temperature within the recommended range for the specific plastic material being used.
Adjust injection speed and pressure, to prevent excessive heat buildup and minimize the occurrence of burn marks.
Improving the mold ventilation system to ensure proper airflow and reduce the risk of trapped air pockets that can cause burn marks.
Using plastic materials that are more heat-resistant or adding special additives that improve heat resistance and reduce the risk of burn marks.
Cleaning and maintaining the mold regularly.
Type 2: Problems caused by wrong mold storage or materials used
In addition to issues that may arise during the molding process, defects in injection-molded parts can also be attributed to factors related to the plastic resin used, or the way in which it was handled prior to production. These types of defects can range from relatively minor cosmetic imperfections to more serious issues that compromise the structural integrity of the part and potentially pose safety risks in certain applications.
6. Discoloration
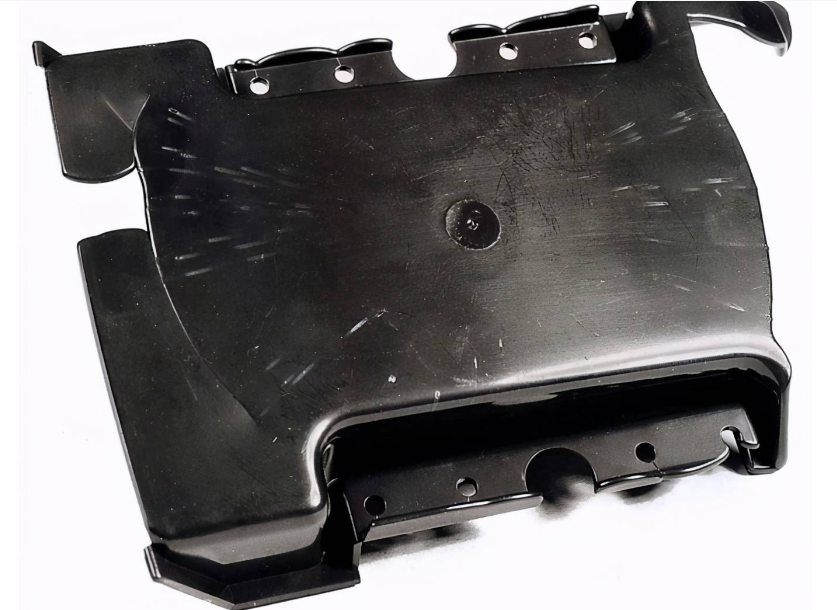
The discoloration is a common defect in injection-molded parts and refers to any variation in color or appearance that deviates from the desired specification. It can occur due to a variety of reasons, including contamination, degradation of the plastic material, overheating, and improper processing.
Contamination can occur when foreign particles, such as dust, oil, or grease, come into contact with the plastic material during processing. These particles can affect the color and appearance of the final part, resulting in discoloration. Degradation of the plastic material can occur due to exposure to high temperatures, moisture, or ultraviolet light, which can cause the material to break down and change color. Overheating can occur when the mold temperature is too high or the injection speed and pressure are not optimized.
Causes:
The plastic material to overheat and change color
Using the wrong processing parameters
Failing to properly dry the plastic material
Solutions:
Using high-quality plastic materials that are less prone to discoloration and degradation.
Ensuring proper handling and storage of the plastic material to prevent contamination and degradation.
Maintaining the mold and equipment to prevent contamination and overheating.
Optimizing the injection molding process parameters, such as mold temperature, injection speed, and pressure, to ensure proper processing and prevent overheating.
Using colorants and additives that are compatible with the plastic material to achieve the desired color and appearance.
Conducting regular inspections and quality checks to identify and address any discoloration issues.
Use a purging compound to eliminate excess colorant
Ensure even mixing of the masterbatch
7. Delamination
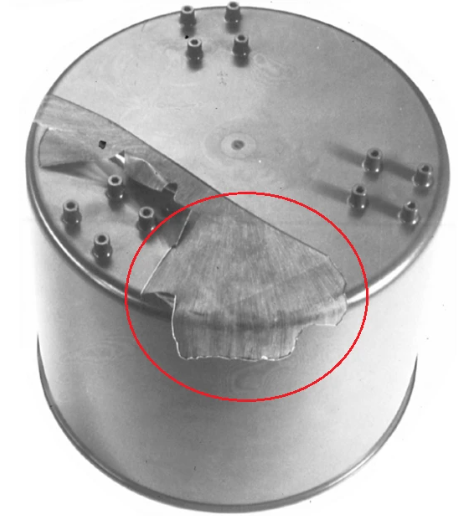
Delamination is a defect that occurs when the layers of an injection-molded part separate or peel apart from each other, resulting in a weakened or structurally compromised part.
Causes:
improper processing,such as using the wrong processing parameters or failing to properly dry the plastic material, can result in delamination
contamination: such as the presence of foreign particles or moisture, can also cause delamination by preventing the plastic material from adhering properly to the mold surface
material incompatibility: such as using different types of plastic materials that are not compatible with each other, can also cause delamination
design issues: such as having thin or uneven walls or sharp angles, can cause stress concentrations that lead to delamination.
Solutions:
Ensuring proper handling and storage of the plastic material to prevent contamination and degradation.
Properly drying the plastic material before processing to remove any moisture.
Optimizing the injection molding process parameters, such as mold temperature, injection speed, and pressure, to ensure proper processing.
Using plastic materials that are compatible with each other and the mold surface.
Designing the part with adequate wall thickness, smooth surfaces, and rounded edges to reduce stress concentrations.
Conducting regular inspections and quality checks to identify and address any delamination issues.
Type 3: Problems caused by Poor Mold Maintenance or Poor Mold Design
Flaws in injection molding can significantly impact mold design. Neglecting to maintain the mold appropriately can also act as a trigger for molding defects. As these defects manifest in the final stages, rectifying them can be an arduous and expensive task.
8. Flash
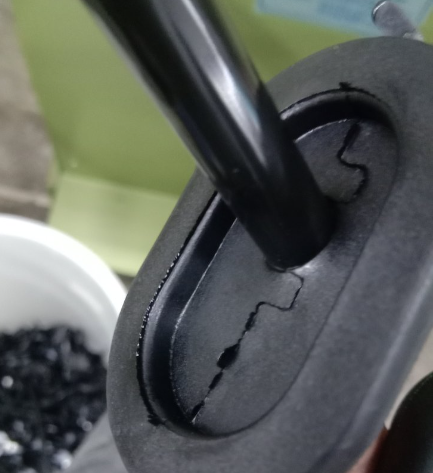
Flash is a common defect in injection-molded parts and refers to excess material that extends beyond the intended parting line or mold cavity. It can occur due to several reasons, including improper mold design, poor mold maintenance, excessive injection pressure or speed, and material shrinkage.
Causes:
Improper mold design or poor mold maintenance can cause flash by allowing the plastic material to escape from the mold cavity through gaps or spaces in the mold.
Excessive injection pressure or speed can also cause flash by forcing the plastic material beyond the intended mold cavity.
Material shrinkage can also contribute to flash by causing the plastic material to contract and pull away from the mold surface, leaving excess material behind.
Solutions:
Optimizing the mold design and maintaining the mold to ensure proper sealing and prevent material escape.
Reducing injection pressure and speed to prevent excessive material flow.
Using plastic materials with lower shrinkage rates reduces the likelihood of excess material being left behind.
Conducting regular inspections and quality checks to identify and address any flash issues.
Using automation or robots to trim excess material and ensure consistent quality.
9. Short Shot
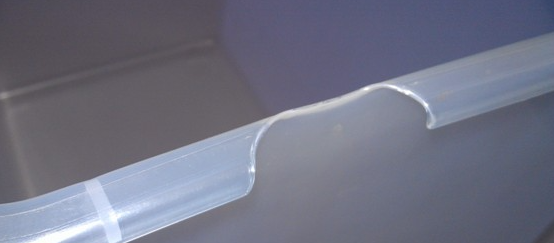
A short shot is a defect that occurs when the injection-molded part is incomplete, resulting in missing or underdeveloped sections of the part. It can occur due to several reasons, including insufficient material, improper mold design, processing parameters, or material properties.
Causes:
Insufficient material can cause short shots by not providing enough plastic material to fill the mold cavity completely.
Improper mold design, such as inadequate venting or gating, can also cause short shots by restricting the flow of plastic material into the mold cavity.
Improper processing parameters, such as low injection pressure, short injection time, or inadequate cooling time, can also cause short shots by not allowing the plastic material to flow and solidify properly.
Material properties, such as high viscosity or low melt flow index, can also contribute to short shots by making it difficult for the plastic material to flow into all areas of the mold cavity.
Solutions:
Optimizing the mold design to ensure adequate venting and gating for proper material flow.
Adjusting the processing parameters, such as increasing injection pressure, prolonging injection time, or increasing cooling time, to provide sufficient material flow and solidification.
Using plastic materials with appropriate properties, such as low viscosity or high melt flow index, to facilitate material flow into all areas of the mold cavity.
Conducting regular inspections and quality checks to identify and address any short-shot issues.
The common injection molding defects:
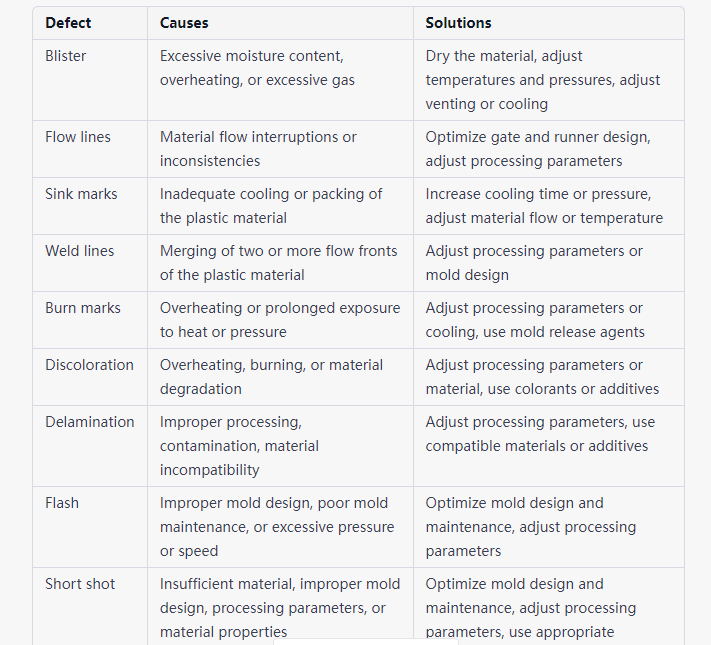
Conclusion
Injection molding is a common manufacturing process used to produce plastic parts. However, this process can result in various defects, such as blisters, sink marks, weld lines, burn marks, discoloration, delamination, flash, and short shot. These defects can be caused by factors such as material properties, mold design, processing parameters, or maintenance. To minimize or eliminate these defects, solutions such as adjusting processing parameters, optimizing mold design, using appropriate materials, and conducting regular inspections and maintenance can be employed.
Comments:
Do you have any other good advice for addressing defects in injection-molded products? Share your tips with Louise at sales02@sino-mold.com or https://www.linkedin.com/in/louise-injectionmold/. Thank you for your help.
Find a good supplier to help you:
At Sino-Mold , Our top-notch technical expertise allows us to avoid these defects by all means. Our cost-efficient plastic injection molding services are available for mass production and rapid prototypes. These and many more you will receive when you upload your design files for a quotation.