Lead In
Plastic injection molding is a highly efficient and cost-effective method for producing plastic parts in large volumes. Injection molds play a critical very important role in this process, as they are responsible for shaping and forming the plastic into the desired product. However, like any tool, plastic injection mold maintenance molds require proper care and maintenance to function effectively and produce high-quality parts over the long term. In this guide, we will explore the importance of maintaining and caring for plastic and injection molding machine maintenance molds, as well as the best practices for cleaning, lubricating, preventing wear and tear, repairing, restoring, storing, and handling these valuable tools.
Whether you are a seasoned injection molding professional or new to the industry, this guide will provide you with valuable insights and actionable tips for ensuring the longevity and optimal performance of your injection molds.
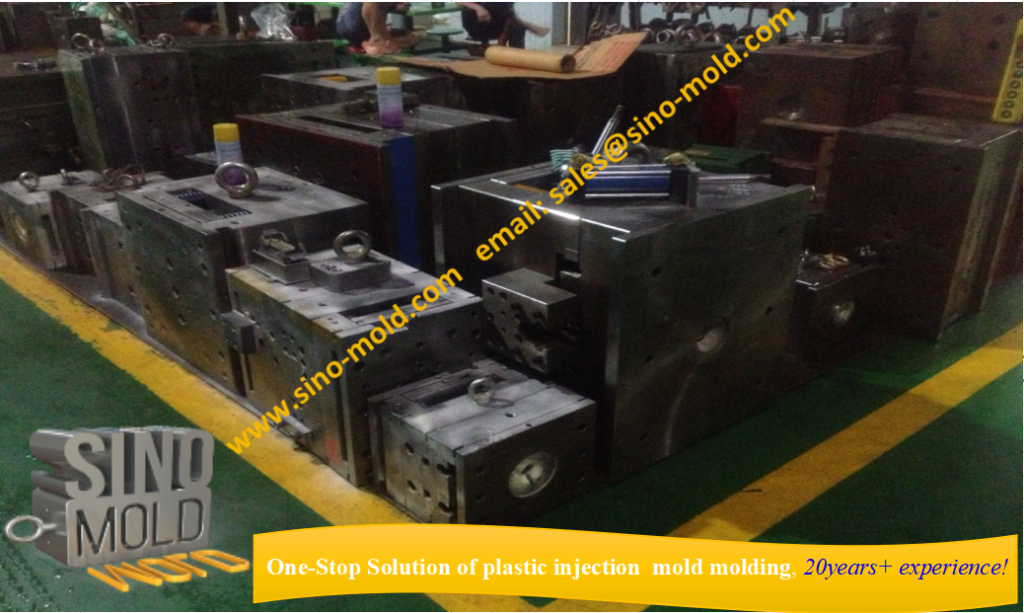
Why is it important to maintain and care for plastic injection mold?
Maintaining and caring for injection mold can have several benefits:
Quality of parts: A well-maintained mold produces high-quality parts with consistent dimensions, surface finish, and structural integrity. Poorly maintained molds can lead to defects such as warping, sink marks, mold rust, and flash, compromising the functionality of the part quality final product.
Production efficiency: A well-maintained mold can reduce downtime, increase production speed, and surface quality, and lower production costs. Manufacturers can avoid frequent repairs and replacements by keeping molds in good condition.
Worker safety: Molds that are not properly maintained can pose safety risks to workers. Regular maintenance and care of molds can prevent these hazards and ensure a safe working environment.
Longevity of molds: Proper mold maintenance can extend the life of a mold, reducing the need for frequent replacements. This can be particularly important for expensive molds, which can cost tens or even hundreds of thousands of dollars to replace.
Regular Cleaning and Lubrication
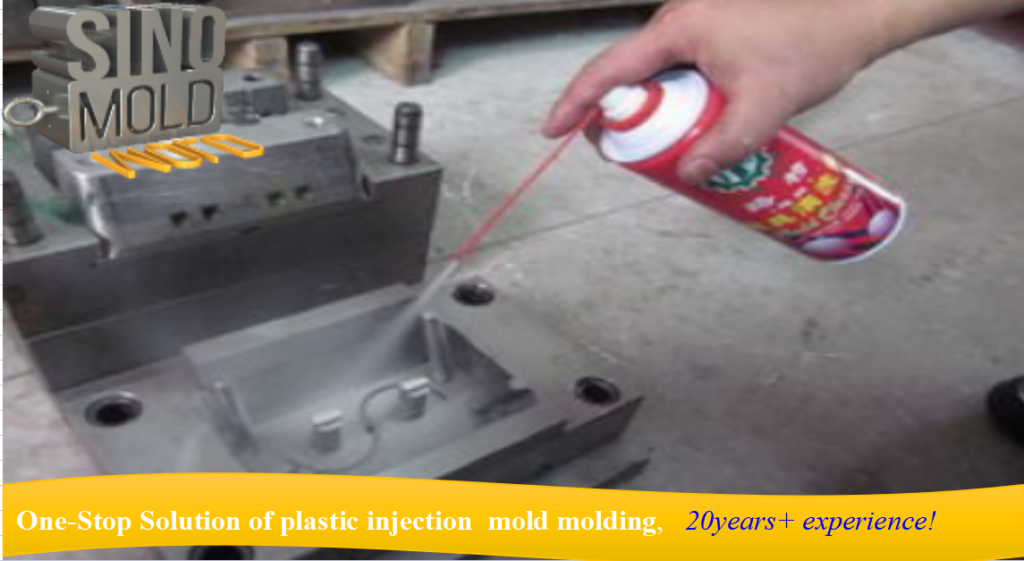
How often to clean and lubricate plastic injection mold?
The frequency of cleaning and lubrication of plastic injection mold depends on various factors such as the production volume, type of plastic material, injection mold, design, and operating conditions. However, in general, maintain plastic injection mold should be cleaned and lubricated regularly to maintain optimal performance and prevent damage.
For example, it is recommended to clean and inspect the molds after every production run to remove any residue or debris that may have accumulated during the process. Lubrication should also be applied regularly to prevent wear and damage to the mold components, particularly those that undergo high friction or pressure. The frequency of lubrication can vary depending on the type of lubricant used, but it is typically recommended to apply a thin layer of lubricant before each production run or every few hours of normal operation.
What are the best practices for cleaning and lubricating plastic injection molds?
Cleaning:
Wear appropriate personal protective equipment (PPE) when cleaning molds, including gloves, safety glasses, and respirators if needed.
Use a mild, non-abrasive cleaner that is safe for the specific mold material and will not damage the surface finish.
Avoid using high-pressure water or abrasive tools that can scratch or damage other deposits in the mold.
Disassemble the mold and clean each component thoroughly, including the cavity, mold core, and cooling channels.
Inspect the mold for signs of wear or damage during the mold cleaning up, such as cracks, chips, or pitting.
Dry the mold components completely dry after cleaning to prevent moisture from causing corrosion.
Lubrication:
Select a lubricant that is suitable for the specific mold material and operating conditions.
Apply a thin layer of lubricant evenly to the mold surfaces using a lint-free cloth or applicator.
Avoid over-lubricating the mold, as an excess lubricant can attract dirt and debris on the mold surface, leading to potential contamination or damage.
Lubricate all moving parts of the mold, including ejector pins, slides, and cores.
Check the lubrication level regularly and reapply as needed during production
Preventing Wear and Tear
How to identify and solve the problems that lead to the wear of plastic injection mold?
Determine the root cause: check the mold design and production process to determine the root cause of mold wear. Common causes of die wear include improper material selection, insufficient cooling, excessive pressure, and improper maintenance.
Check the mold: Make a thorough inspection of the mold to identify worn and damaged areas, such as cracks, chips, or pitting. Check all parts of the mold, including the whole mold cavity surface, surface, core, and cooling channels.
Timely treatment of wear and damage: timely treatment of any wear or damage found in inspection to prevent further damage to the whole injection molding machine. Depending on the damage, repairs may include welding, polishing, or replacing the affected parts.
Improve material selection: ensure that the mold material is suitable for the production process and the type of plastic material used. Consider using more wear-resistant materials, such raw materials such as tool steels or ceramics.
Optimized cooling: ensure that the whole mold surface is fully cooled to prevent excessive heat and moisture accumulation, which leads to wear and damage. Consider using conformal cooling or other advanced cooling technologies to optimize mold life and cooling efficiency.
Reduce pressure: high injection pressures can cause too much pressure on the surface of the mold, leading to wear and damage. Consider lowering the injection pressure or using pressure limit controls to prevent damage.
Carry out a maintenance plan for regular maintenance: Regular maintenance practices, such as cleaning and lubrication, can prevent the mold from wearing and damaging. Follow the mold manufacturer’s recommendations for your maintenance plan, practices, and frequency.
To put it simply, preventing die wear involves a thorough approach. This includes identifying the root cause of the problem, examining the die, addressing wear and damage quickly, selecting better materials, improving cooling methods, reducing pressure, and regularly maintaining the injection mold maintenance itself. By following these steps, you can minimize mold wear, prevent corrosion, prolong the lifespan of the mold, and enhance production efficiency.

How to prevent plastic molds from wearing out?
Choosing the right materials: Selecting materials that are specifically designed for the type of product you are injection molding for can help prevent wear and tear. Using low-quality or incorrect materials can lead to faster damage to the injection molding process itself.
An optimal cooling channel used: Proper cooling of the mold cavity is very important to prevent the mold cavities from warping and cracking. Ensure that there is no debris in the cooling channels and that the cooling system can work effectively. You may also want to consider using advanced cooling techniques, such as conformal cooling, to improve the cooling process.
Decompression: putting too much pressure on the plastic during injection molding can cause it to wear quickly. Adjust the pressure to the optimum level according to the type of plastic to be molded, and ensure the injection process is consistent and accurate.
Implementing regular maintenance: Regular maintenance of the mold is crucial to prevent wear and tear. This includes cleaning, lubricating, and checking for any signs of damage or wear. You should also check for the accumulation of any release agents, which can cause damage over time.
Addressing wear and damage promptly: If you notice any signs of wear or damage, address them promptly. This may include repairing or replacing parts of the front injection molding, to prevent further damage. You should also determine and correct the root cause of any problems to prevent them from happening again.
By following these steps, you can prevent the plastic mold from being worn and prolong its life, and total cost, and finally improve the quality and efficiency of the production process.
Mold Repair and Maintenance
What should be done if a plastic injection mold needs repair or Maintenance?
If a plastic mold needs repair or Maintenance, taking prompt action is essential to prevent further damage and ensure that it can continue to produce high-quality plastic parts. This preventative maintenance involves identifying the problem, planning the repair, choosing a qualified repair service if necessary, testing the mold, and implementing preventive maintenance measures to avoid future issues. Refer these steps, you can effectively repair or restore your plastic mold and optimize its performance for your business.
When to seek professional assistance?
Knowing when to seek professional assistance for your plastic molds is crucial to prevent further damage and ensure that they continue to produce high-quality parts. At Sino Mold Industrial, we offer a range of services to help you maintain and repair your plastic molds.
If you are experiencing issues with your molds such as worn-out or damaged molds, rusting, or uncertain about how to maintain them, our team of experts is always available to provide professional advice and assistance. We can help you identify the problem, plan the repair, choose a qualified repair service if necessary, and test the mold to ensure optimal performance.
In addition, if your plastic mold has reached the end of its lifespan, we can assist you in designing and manufacturing a new one tailored to your specific needs. We provide excellent after-sales service to ensure that your new mold continues to meet your production needs.
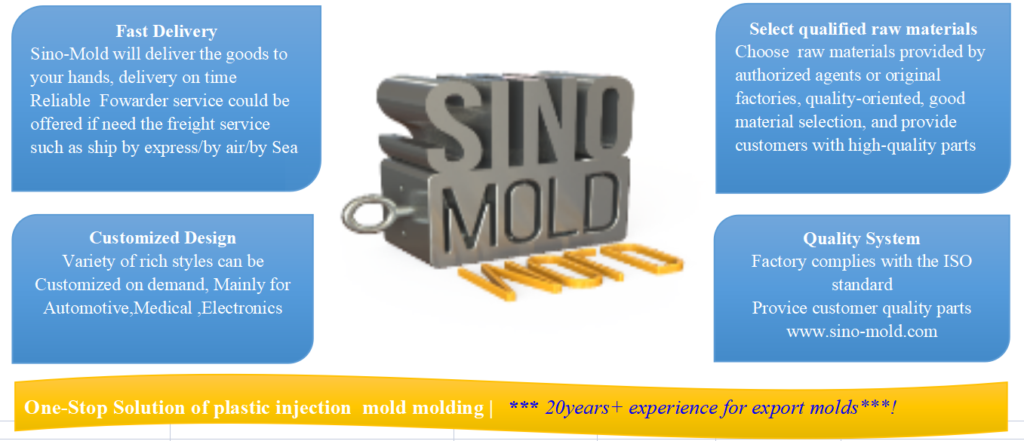
At Sino Mold Industrial Co.Ltd, we pride ourselves on our punctual delivery and outstanding customer service.
Contact us today to know more about our service quickly and how we can help you with your plastic mold needs.
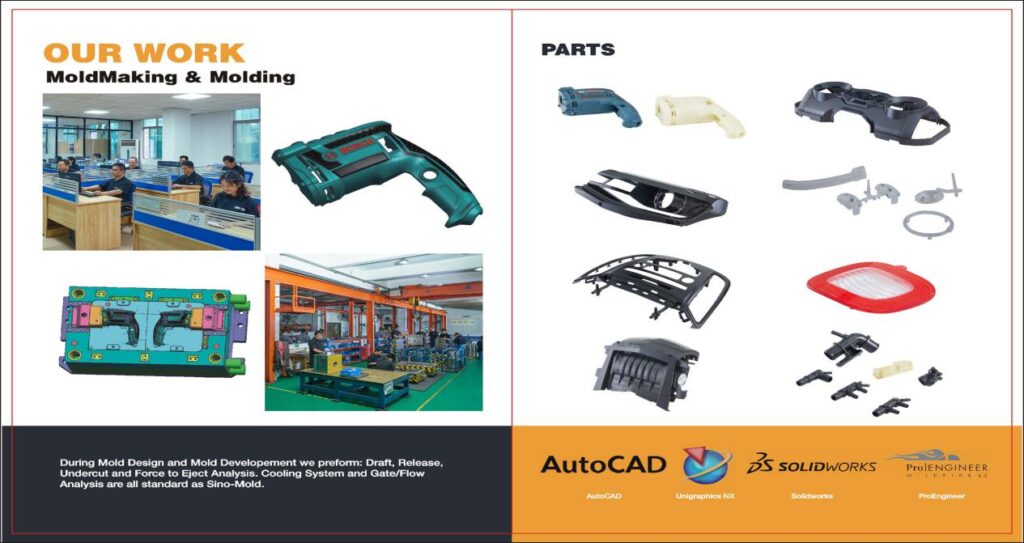
Conclusion
Proper maintenance and care of plastic injection molds are essential for producing high-quality parts consistently, increasing production efficiency, ensuring worker safety, and extending the life of the plastic injection mold plays. By following the best practices for cleaning, lubricating, preventing wear and tear, repairing, restoring, storing, and handling injection molds, manufacturers can ensure the optimal performance of their injection molds.
If you are interested, please subscribe to our channel, and feel free to leave your comments below.
If you require mold services, we invite you to choose us as your trusted supplier now or in near future! Thanks for liking and sharing!