An excellent mold manufacturing factory, which creates high-quality mold products and considerable profits, must have its own unique place. Analyzing its causes, it generally has the following characteristics: perfect system, efficient team, super executive power, The spirit of innovation.
Aside from the strategy and development direction of these companies’ operations, this article mainly explains the system construction and on-site management of the mold factory.
Organizational Structure and Work Procedures
For the mold manufacturing department, different companies have different management structures. For all the matters of the mold, some fitters are responsible for following up, and some TE and production supervisor follow up. The author uses the first mode for management subdivision, which has the advantages of quick response and high efficiency.

1. Design Department – ESI Review, Mold Design
This department is mainly responsible for the early ESI review, mold design, communication with clients, product review, and providing technical support for quotations. For molds with a single product and short cycle, standard parts such as guide ralls, wear plates, stop pins, support pillars, and angular pin can be used. Even the cavity, core and slides can be designed as standard parts, greatly speeding up the manufacturing cycle of new molds.
2. Machining Department – Programming, CNC, EDM, EDW, Lathing and Grinding
This department is mainly responsible for the production and allocation of machining. The process can be coordinated and cross-coordinated so that the machining section can remain fully unobstructed. Blocked processes can be promptly transferred to the next process, greatly reducing the back-and-forth coordination between teams and shortening communication time. This ensures that molds can be put into production in a timely manner, ensuring the quality and delivery time of the molds.
3. Assembly Department – Mold Assembly, TE Follow-up, Mold Modification, Polishing
Fitters are responsible for the assembly, modification of mold schemes, and maintenance of the molds. The master responsibility system is adopted to follow up on the details of the molds, including the progress of materials, processing, and standard parts. They ensure the final delivery time and the quality of the molds. TE are mainly responsible for following up on mold modification, leading the development of modified mold schemes, and reviewing the structure of mold design during the mold design phase.
4. Planning and Process Group (PMC)
This group is responsible for developing production plans and monitoring production progress. They develop part working hours, calculate mold costs, handle exceptions, and arrange part processing technology.
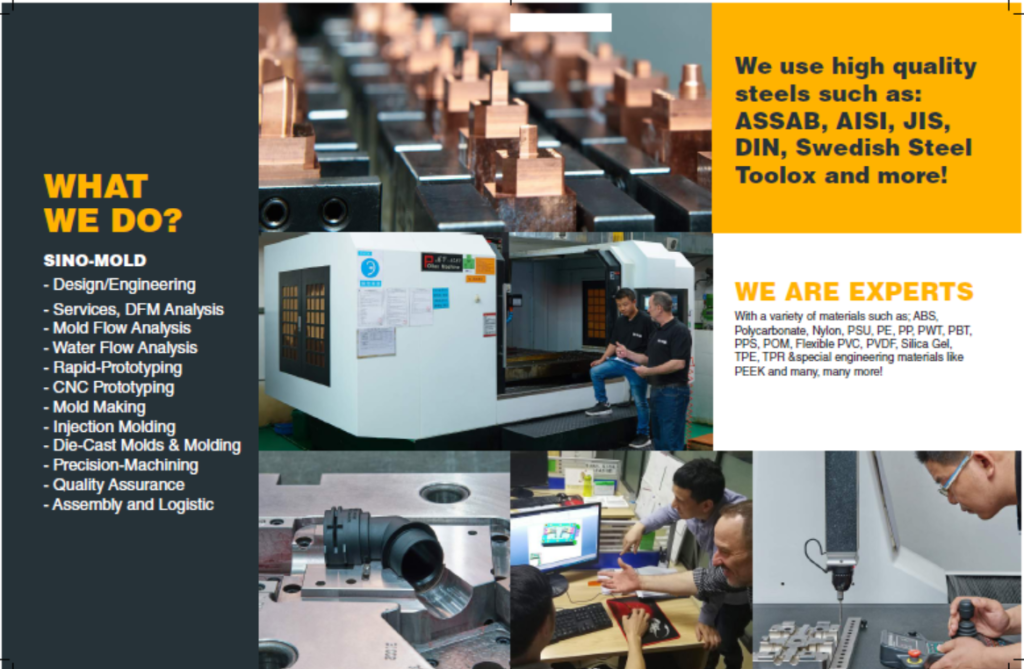
Detailed system construction and site management starting from processing
- CAM Programming Group
It plays a crucial role in mold production, and the programmer’s unreasonable program or insufficient technical ability may result in a workpiece taking more than twice the time to process on a CNC machine or even more. By conducting secondary development on UG, the programmer can use the UG machining template and establish a UG tool library, set parameters uniformly, and avoid adjusting too many parameters. This can reduce the tedious and error-prone manual input of machining parameters, improve programming efficiency, increase CNC machine processing efficiency, improve machining accuracy, and save at least about a quarter of manpower. It can also increase the utilization efficiency of the machine tool.
The programming level directly affects the quality, accuracy, and work efficiency of CNC, EDM, wire cutting, lathing, grinding, and assembly.
1) Develop standardized UG mold machining templates and plugins for all programmers to use. This will improve programming efficiency and reduce errors, including tool speeds and feed rates. Determine reasonable processing parameters for the core insert, inserts, mold base, electrodes, and strictly execute programming to control NC speeds and feeds to prevent workshop CNC program changes and improve efficiency.
2) Write the program in single lines and single tool numbers to facilitate operation when repairing in the CNC workshop, without the need to program separately.
3) Develop a complete programming manual guidebook, including steel, graphite, copper, and specific machining instructions.
4) Secondary development of LINK drawings to reduce manual operations and improve efficiency.
5) Develop secondary program forms. After maturity, paperless operations can be performed. The CNC workshop can open the PDF file to install the tool.
6) Automatic electrode discharge, working with EDM, secondary development of automatic discharge, the basic concept is that the operator installs the electrode, divides the workpiece into the middle and back, opens the CNC file generated by the programming automatically, and automatically discharges, including automatic completion of XYZ data and automatic setting of discharge parameters such as current pulse width.
7) Automatic workpiece detection, working with QC secondary development, automatic detection, the basic concept is that the operator installs the electrode on the three-dimensional coordinate system, divides the workpiece into the middle and back, opens the CNC file generated by the programming automatically, and automatically measures the relevant detection points.
8) Collect and summarize common programming errors and develop the “Common Abnormal Issues in CNC Mold Programming” for programmers to learn and avoid programming abnormalities.
9) The work of the programmer should follow the “CNC Programmer Work Specification,” “CNC Mold Programming Parameter Standard,” and “Common Abnormal Issues in CNC Mold Programming.” The programmer is responsible for following up on the NC progress of the mold they programmed.
10) After completing a set of molds, list the program and electrode inventory table and distribute it to NC, EDM, wire cutting, mold room, and other related personnel, so that they can clearly and timely understand the progress of the required programs or electrodes. NC, EDM, wire cutting, and mold room can arrange work according to the overall plan of the mold.
- In the early stages of design, the programming team should participate in design reviews, inspect the design, hold a processing review meeting after the design is completed, and the programmer should immediately dismantle the electrode and produce a material list, then write the electrode program and discharge drawing, and finally write the steel program and fill in the relevant progress information on the schedule.
- The CNC Machining Group
It is an important department in mold manufacturing, and the quality and efficiency of its machining directly affect the success or failure of the mold. This team needs to effectively combine hardware resources, machine operators, production technology processes, departmental norms, and other software and hardware to fully meet production requirements for product quality and efficiency.
Automatic tool changers should be used to clamp tools for workpiece machining. When selecting machine tools, it is best to choose machine tools with enclosed tool magazines. Machine tools that use open tool magazines are prone to debris such as iron filings on the tool shank, and the tool turret is also prone to jamming during tool changes, which can greatly reduce machining accuracy. If the tool clamping deviation of the machine tool is too large, it may also result in scrapped workpieces.
The transmission method should use a local area network connection, with one computer controlling multiple CNC machine tools, which is convenient for management and saves computer hardware costs.
The CNC machining electrodes should use quick-change EROW or 3R systems, and should be used synchronously with spark machines. All electrodes do not need to be manually set up, but can be directly called by the programming program for machining. The operator only needs to clamp the workpiece and call the programming program. The machining feed rate of all programs is controlled by the programming program. In order to standardize and unify the machining speed and prevent the operator from controlling the machining speed of the machine tool arbitrarily, the operator is required to turn the machine tool’s feed knob switch to 100%, and then the machine tool will automatically change the tool and automatically machine the workpiece. After machining is completed, the operator only needs to check whether the workpiece is qualified, clean it, and remove it from the machine.
For mid-term planning, an off-machine pre-setting station should be used to calibrate the workpiece in advance, and then directly machined on the machine, saving clamping time. For long-term planning, an automatic production line system should be used.
1) Hardware machine tools and software programs should be implemented in a programmed and automated manner.
2) The machine operator should perform foolproof operations, simply clamping the tool according to the program, without the need to modify the program’s speed, feed, etc., to prevent manual errors.
3) Coordinate programming with paperless operations. This saves costs and improves efficiency.
4) Strictly implement the “three checks” (first inspection, mutual inspection, and self-inspection) and “three no’s” (no overlooking the cause, no neglecting preventive measures, and no substandard products flowing out).
5) Check the accuracy and wear of the tool after machining to ensure that the quality and accuracy of the machined workpiece meet the requirements of completing the FIT mold in one go. Prevent the use of dull tools.
- Check the tools in the tool magazine daily and replace any unqualified tools in a timely manner.
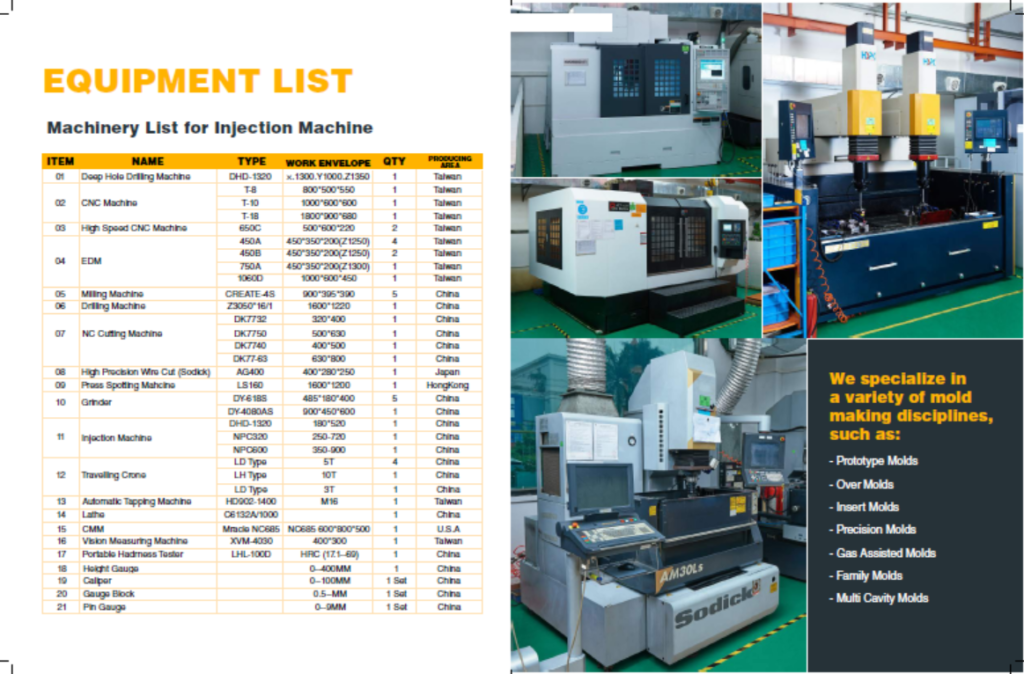
- The EDM (Electrical Discharge Machining) Group
It plays a crucial role in the mold manufacturing industry. EDM has a wide range of applications, small cutting force, and is easy to shape. It can directly use electrical energy to perform gap discharge, which can be used to process small holes, hard alloys processing, mirror processing, and almost all shapes. It can also be used for special surface processing, with a wide range of applications.
For EDM, graphite electrodes should be used for machining. The cost of graphite is about 1.5-2 times that of copper, but the discharge speed of graphite is 30% faster than that of copper, and the forming speed is more than 50% faster than that of copper. Graphite discharge is of great significance for the quick delivery of mobile phone molds. For surface requirements less than VDI18, copper electrodes can be used to meet the requirements.
EROWA or 3R quick clamping positioning should be used for EDM, and an automatic discharge system should be developed. All electrodes, including oblique glue mouth electrodes, can be discharged without calibration, and without touching the numbers. The electrode discharge data is generated in batches by using UG software on the computer, without inputting any discharge parameters. Only the electrode number needs to be entered in the machine, and full-automatic discharge machining can be carried out. In this way, each machine can save about 2 hours of clamping time per day. The average number of machines operated by each person can be reduced from 2 to 3, and errors caused by manual input of discharge parameters can be avoided. If the company has sufficient funds, an off-machine pre-setting station can be used to calibrate the workpiece in advance, and then directly machined on the machine to save clamping time.
1) Coordinate programming to achieve paperless operations, saving costs and improving efficiency.
2) Secondary development should be used to achieve EDM discharge automation, standardization, and basic concept of programmatic operation. The operator installs the electrode, divides the workpiece, and opens the CNC file automatically generated by the program for automatic discharge, including the automatic completion of XYZ data and the automatic setting of discharge parameters such as current pulse width.
3) The machine operator should perform foolproof operations, simply processing according to the program, without the need to modify the program to prevent manual errors.
4) Strictly implement the “three checks” (first inspection, mutual inspection, and self-inspection) and “three no’s” (no overlooking the cause, no neglecting preventive measures, and no substandard products flowing out).
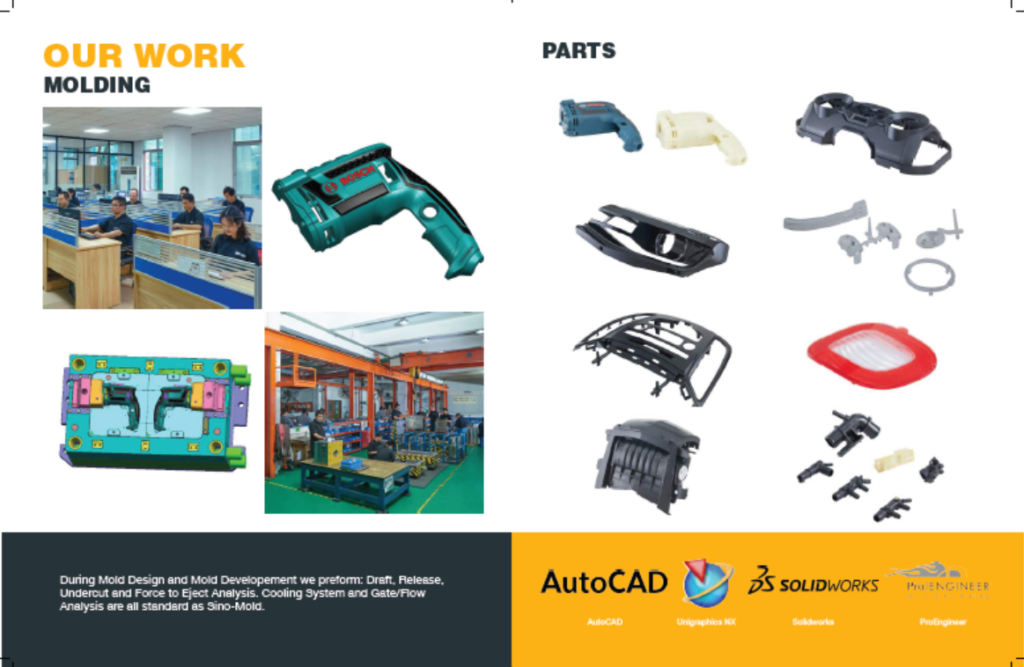
- The EDW (Electrical Discharge Wire Cutting) Group
It is an essential part of the mold manufacturing industry. It has evolved from fast wire cutting to precise slow wire cutting.
For wire cutting, it is necessary to equip multiple parts with quick clamping fixtures, which can effectively reduce clamping time, minimize the difference between part and reference surfaces, save labor costs, and allow rough cuts to be made using medium wire cutting machines for non-precision parts (such as inserts, rows, bevels, etc.). The time required for rough cutting using medium wire cutting is twice as fast as that of fast wire cutting. For precision parts, galvanized wire can be used for machining. The machining speed of galvanized wire is 13% faster than that of copper wire, but the cost of galvanized wire is slightly higher than that of copper wire.
The EDW team should coordinate programming to achieve paperless operations, saving costs and improving efficiency. Secondary development should be used to achieve programmatic, standardized EDW machining. The wire cutting program should be programmed by a dedicated person, and the machine operator should perform foolproof operations, simply processing according to the program without modifying the program to prevent manual errors.
The team should also strictly implement the “three checks” (first inspection, mutual inspection, and self-inspection) and “three no’s” (no overlooking the cause, no neglecting preventive measures, and no substandard products flowing out). Additionally, the team should check the accuracy and wear of the tool after machining to maintain the quality and accuracy of the machined workpiece.
5. Lathing And Grinding Group
The turning, milling, grinding, and drilling processes are important components of mold production.
Lathes are mainly used for processing the shape, inner holes, threads, and round materials. Milling machines are mainly used for rough machining of mold components, such as needle holes, screw holes, water transport holes, spring holes, tapping, and the external shape of mold components. Grinding machines are mainly used for precision machining of the external shape of mold components, and can be used for machining various high-hard and super-hard materials. Drilling machines are mainly used for drilling water transport holes.
The lathe and grinding team belongs to a pure manual craft, with one person operating one machine. Night shifts are not suitable for production due to low production efficiency, low cost of the machine, and low depreciation rate. During normal times, the focus is on producing molds. When there is spare time, standard mold components can be machined for inventory, which can greatly reduce part processing time and shorten the production cycle of molds.
The following training should be provided to the lathe and grinding team:
1). Train employees in the lathe and grinding processes, and master professional knowledge such as the causes of common grinding and milling defects and prevention methods.
2). Train employees on the construction, use, adjustment, and maintenance of common tools, clamps, and measuring tools.
3). Train employees on the types, brands, specifications, performance, uses, and maintenance of common cutting tools and grinding wheels.
4). Train employees on the types, brands, milling and grinding performance, and thermal expansion and contraction performance of metal materials.
5). Train employees to understand the method of reading mold drawings, and the conversion and application of trigonometric functions.
6).Train employees on the specifications, performance, structure, transmission system, and adjustment methods of machine tools.
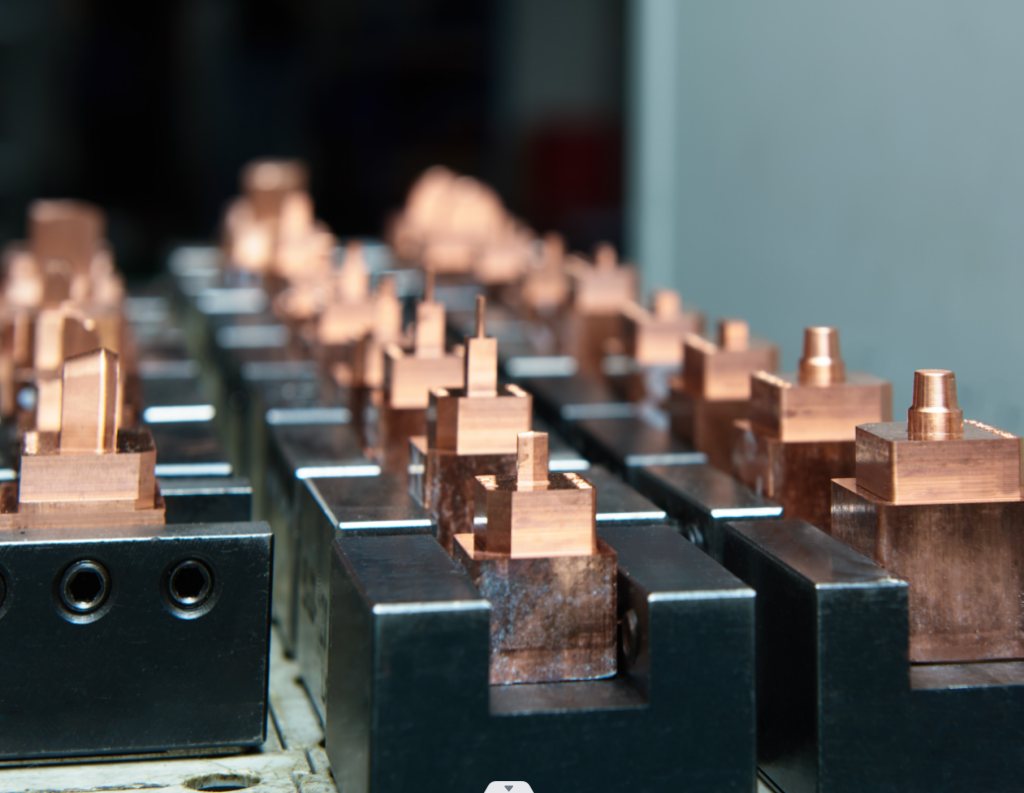
6. Mold Assembly Group
Assembly is the final process after all processing is completed, and it is in a critical and important position in the entire mold manufacturing process. From the perspective of precision mold production, the requirements for the management and operators of the assembly workshop are also very strict. This is reflected in the requirements for product quality, precision machining data of mold components, appearance maintenance, and also requires the operator to have a good quality awareness and operating techniques.
Assembly operations are manual work, which requires clear thinking and meticulous work. Before assembling the workpiece, it is necessary to check whether there are any omissions or errors in each glue position, clearance position, and assembly position. During assembly, attention should be paid to the operation techniques. The use of grinders is prohibited during FIT, and sandpaper and whetstones are allowed to remove knife marks in small areas.
The following measures should be taken for the assembly group:
1). Develop a standardized “Mold Assembly Operating Guide” to provide guidance on the operation techniques for inserts, inclined tops, core molds, and other FIT molds.
2). Develop and improve the “Mold Assembly Technical Manual”, collect assembly cases that have occurred in the past and are known, and use them as teaching materials for regular training.
- Conduct regular abnormality or experience summaries every month, and have each master create PPT training materials.
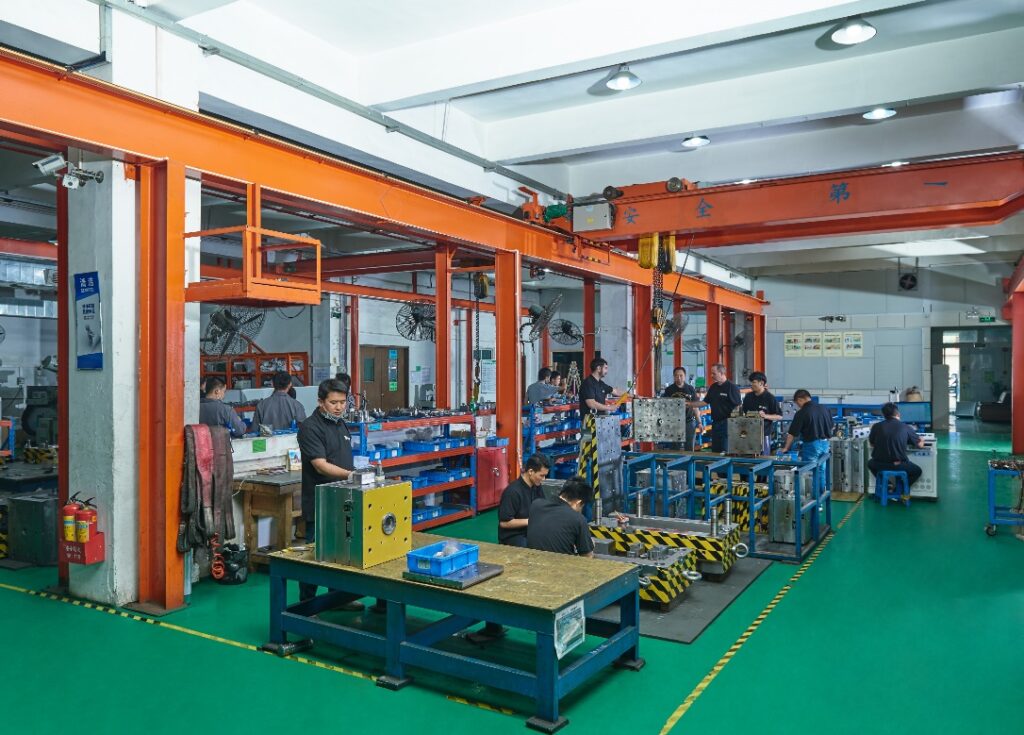
7. Mold TE Group
TE modification mold program is very critical, some mold factory TE professional ability is not strong, resulting in frequent mold repair, in addition to customer mold change, its own mold repair more than ten times are very common. The cost of a mold repair is as little as one thousand yuan, more than several thousand yuan, and the root cause of a mold factory is not profitable too much mold repair is one of the main reasons.
1) List detailed solutions to common mold problems such as tip, shrinkage, deformation, welding, top white and so on.
2) For the modification of the size, it is necessary to start the detection from the 3D physical steel material, then to the product, and then to the injection molding parameters, and gradually investigate the cause.
- TE should sum up experience, review the reasons for each mold repair failure, and prevent the mold repair program from becoming an experimental program.
- Process planning group
Planning is related to the progress control and delivery of the entire mold, and the process directly affects the accuracy and efficiency of the mold, as well as the quality of the final mold products. Each part has a different processing method, which needs to be comprehensively considered in combination with processing cost, operation difficulty and working hour efficiency, and reasonable arrangement of the process flow.
1) Plan to list the detailed schedule, including design, ordering, feeding, mold, drawing, standard parts, spare parts, mold core, insert, inclined top, row position, pressing block, wear plate, etc.
2) Follow up the process in time, check the status of parts every day according to the schedule.
3) The processing process to do color drawings (do secondary development), detailed development of the processing plan, the front die, after the die, row, insert and so on detailed list of processing rules, distinguish programming, CNC, gong machine, grinder, line cutting, spark machine, lathe, drilling machine processing sequence and steps, reduce waiting time.
03 Specific management method
1. Machine Tools and Equipment
1). Thoroughly understand the performance and operation methods of each machine tool, and develop a “Machine Tool Operation User Manual” for each machine to enable technicians to use the machine tools effectively and efficiently.
2). Collect and develop a “Common Abnormal Alerts and Handling Methods” guidebook to train all technicians to handle common abnormal alerts, and ensure that they possess the ability to handle them.
3). Develop a “Machine Tool Maintenance Program” for the use of consumables and daily maintenance of the machine tool based on the relevant recommendations of the machine tool manufacturer and actual situations, to ensure that the machine tool has stable machining accuracy.
- 2. Tooling and Cutting Tools
1). Measure and manage tools: Develop a “Tool Use and Maintenance Guide” for measuring tools such as gauges, center finders, calipers, tool setters, electronic probes, sine tables, etc. to ensure that all technicians can use and maintain them properly. Abnormally damaged tools should be punished according to the rules and regulations.
2). Fixture management: Regularly grind circular iron, code plates, code strips, and other fixtures to ensure their accuracy (and record size changes). Develop a “Fixture Use and Maintenance Guide” for tiger clamps, suction cups, EROWA, wire cutting, and other fixtures, so that every technician can skillfully clamp them.
3). Cutting tool management: In order to ensure machining accuracy and control processing costs, centralize the management of cutting heads, collets, tool holders, cutting tools, and tool inserts; store rough and finish cutting tools separately in the workshop and inventory. Regularly conduct tool inventory, settlement, and procurement. Evaluate the use of new cutting tools and understand the characteristics of different materials processed by different types of cutting tools. Reasonably use cutting tools to reduce tool costs while ensuring quality and efficiency.
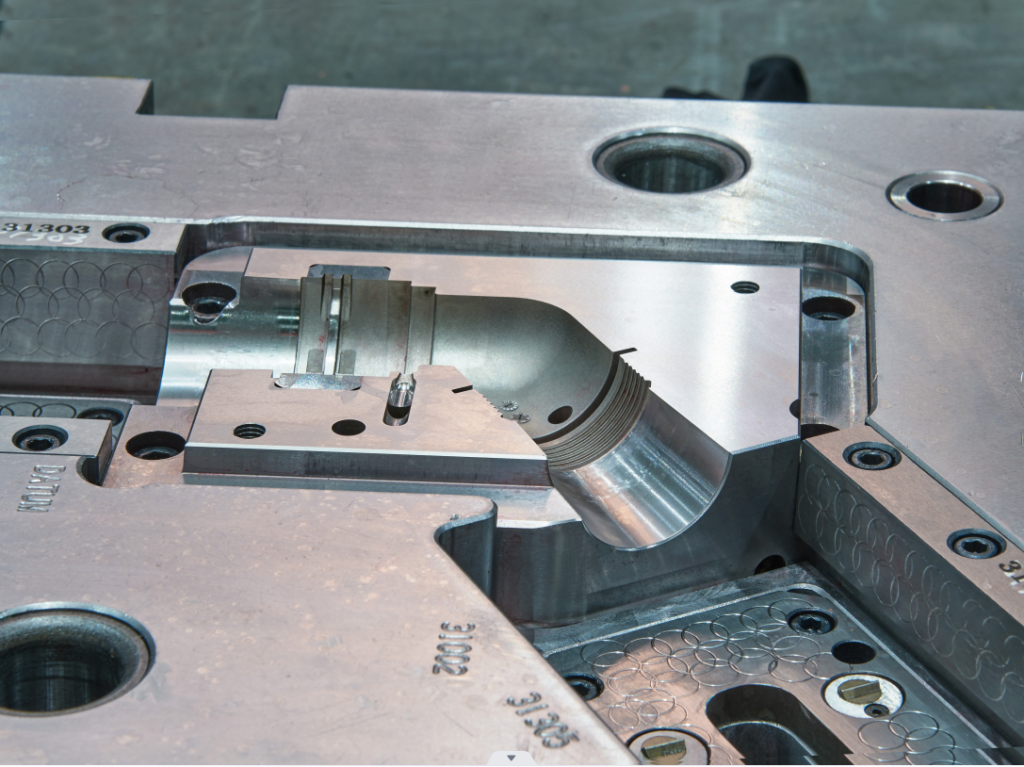
3. Computer System
1). Build a local area network in the company’s intranet and set different access permissions for supervisors, clerks, programmers, and transmission computers.
2). Install computers for different positions according to their job nature, and only install work-related software to prevent the use of company resources for non-work-related matters.
3). Implement unified naming and management of documents and develop a “Document Management Standard.”
4. Workshop Environment 5S Management
A good working environment is crucial for producing good products. Develop a hygiene duty roster and area division, implement 5S on-site environment management, and maintain a pleasing working environment to produce good products. 1S Sorting, 2S Straightening, 3S Sweeping, 4S Cleaning, and 5S Cultivation.
5. Production Site
1). Divide the area and mark it clearly with text, such as machine tool and equipment area, clamping area, work-in-progress area, completed area, tool cabinet, aisle, etc. Assign the responsibility of cleaning and organizing to individuals and develop a “Workshop 5S Management Standard.”
2). Implement transparent management and publish daily production plans, production scheduling, production summaries, quality and efficiency on the workshop bulletin board to create a good working atmosphere.
6. Personnel Management
No matter how good the hardware resources are, they still need people to operate and complete the work. The quality of the personnel directly affects the efficiency of equipment use and the quality of the products. Quality and efficiency are mainly determined by hardware equipment, processes, the quality of technicians, and production management. The quality of the technicians is the most important, and their quality directly affects the quality of the workpieces and the efficiency. The quality of the machine operators can be improved in the following five ways:
1). Work Attitude: A good attitude is the foundation of doing things well. Communicate effectively with them regularly, and make them feel the warmth of the team as colleagues during work hours. Cultivate their positive, careful, and responsible work habits.
2). Basic Knowledge: As an experienced technician, understanding basic knowledge is very important. Each technician should be proficient in common operations such as the placement direction of workpieces and calibration. Post warning signs, develop standard methods for routine operations, and emphasize these common operations repeatedly to prevent low-level errors.
3). Skills Training: Develop operation manuals for various machines, provide on-site training for new employees, and have experienced employees mentor and train them. This will help them become familiar with the operation of the machines as soon as possible, which will be advantageous for production continuity.
4). Quality and Efficiency Awareness: Foster employee awareness of quality and efficiency, and develop quality processing standards for molds, inserts, mold embryos, and electrodes. Let each employee know what kind of workpiece we need to produce to be qualified and prevent NG products from flowing into the next process. For abnormal workpieces, in addition to investigating relevant responsibilities, we should also analyze the reasons, designate preventive improvement measures, and post them publicly to prevent the same errors from happening again. Develop rapid clamping standards to reduce idle machine time and improve production efficiency.
5). Promotions and Management: The turnover rate for general programmers is lower than for NC, EDM, and EDW technicians. When there is a need for programming, technicians who have provided excellent service for 1-3 years can be promoted to programming. This can retain the people we want while also motivating employees.
6). Absolute Obedience: Employees must obey the work arrangements of their superiors, without delay or confrontation.
7. System Standards
With first-class hardware systems and excellent personnel, we need reasonable system standards to guide everyone and create a fair, positive, and energetic work environment. We can explain the system standards we need to use from the perspective of the mold processing process:
1). Communication Standard: When processing drawings and workpiece processes, we must have a “Handover Form” for communication.
2). Daily Reporting Standard: Employees should fill out a “Daily Work Report” every day. This form collects the machine utilization rate, evaluates employee performance, and calculates mold costs.
3). Performance Standard: To improve everyone’s work enthusiasm, we evaluate performance based on the work content of the “Daily Work Report.”
8. Technical Reserves
As a technical industry, in addition to cultivating technical backbone in designers, programmers, and technicians, we also need to develop a valuable set of technical data and operating procedures to ensure safe and efficient production in the event of sudden vacancies in any position. The data mainly includes:
1). Machine equipment operation data.
2). Technician work data.
3). Programming technical data.
9. Production Arrangements
The company generates profits by producing products, and the foundation for efficient production has been laid out. Good production, high-quality products, and customer recognition are our ultimate goals. Therefore, controlling the on-site workshop during production is very important:
1). After the customer places an official order for the entire set of molds, a processing review meeting shall be held promptly, and all supervisors shall be called to formulate a plan, including specific times for mold embryos, materials preparation, design, programming, machining, CNC, EDM, wire cutting, assembly, etc.
2). Based on the overall schedule of the mold set plan, hold meetings in a timely manner to understand the status of the molds in the department, adjust work arrangements, and coordinate the overall mold plan.
3). Implement computer networking management, input every workpiece into the computer system, conduct irregular inspections of the workshop to solve processing problems, strictly self-inspect the workpieces after processing, record data, and save self-inspection reports. Implement continuous shift work arrangements to ensure timely delivery.
4). Track the processing status of each set of molds in detail, ensure accurate and comprehensive data, and record it in the computer system. Any authorized manager can clearly understand the completion status of each set of molds through the computer system.
5). Every week, summarize the production output, exception handling, and learning of new techniques systematically. Each employee should know the shortcomings of their department, and the production situation should be transparent and open.
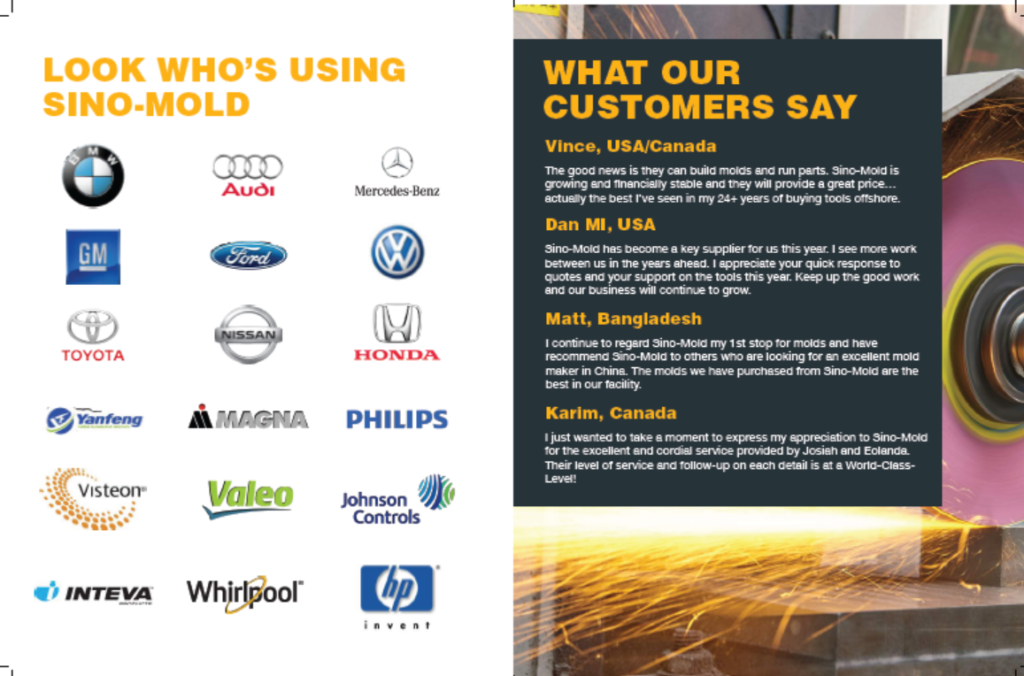
Conclude
No matter how good the system and procedures are, without supervision and execution, they are useless. Team building is critical, and talent is rare. To make profits and grow, companies need not only sufficient orders but also high-quality products and timely delivery. These require technical experts and dedicated employees with strong capabilities to complete. The company needs a sound system, and capable employees should be promoted and given salary increases appropriately, while those with poor abilities should be decisively eliminated. The company’s management must be clear in rewards and punishments so that the enterprise can develop and grow.
If you encounter the following problems in cooperation with the current supplier, such as:
High cost pressure
The manufacturing cycle is too long
technology and innovation needed
High quality requirements
need special customization
no good after sales support
Then you can try to cooperate with Sino-Mold, we will try our best to provide you with a one-stop solution for mold making and injection molding at a reliable price and service !
Email us now :sales@sino-mold.com