
Regarding injection molding, the choice of gate type plays a critical role. Gates are the entry points through which molten plastic is injected into molds, determining the success of the molding process. Different injection gate types can influence product quality, appearance, and efficiency. In this article, we will introduce several common types of injection molding gates to help you better understand their applications and pros and cons.
What is An Injection Molding Gate?
An injection molding gate is a strategically designed, often small, aperture that governs the flow of molten plastic into the mold cavity. The selection of the appropriate injection molding gate type is pivotal to the successful production of your injection molded components.
Key factors including gate type, placement, size, material compatibility, and mold configuration exert a significant influence on the volume, pressure, and temperature of the molten plastic during the injection molding process. The precise design of the gate holds the utmost importance in a range of industries where intricate plastic components are manufactured

Why Injection Mold Gate Design Is Needed?
The design of an injection molding gate holds a direct and profound impact on the outcome of a plastic mold. A well-crafted gate serves as a proficient manager, controlling both the volume and direction of the molten plastic flow into the mold. This is essential to prevent any undesirable flow towards the runner or nozzle, ensuring that the plastic reaches its intended destination – the mold.
Furthermore, a thoughtfully designed mold gate secures the even distribution of molten plastic throughout the entire mold cavity before cooling takes place. This precludes any irregular and premature solidification, thus safeguarding the molded plastic parts from imperfections, such as fractures or stress-related deformations.
Moreover, the injection molding gate generates heat dissipation, a process crucial for optimizing the polymer’s temperature. This prevents the formation of unsightly flow marks and weld lines, enhancing the overall quality of the final product. As a result, manufacturers and product designers can streamline the injection molding process, often eliminating the need for runners, which, in turn, simplifies post-processing treatments
What Is The Importance Of Gate Location In Injection Molding?
In injection molding, the gate is a minute orifice typically positioned between the runner and the mold cavity. While gate design encompasses considerations like gate size, it is the gate’s precise placement that wields a critical influence on the process’s success and the resultant part quality.
The strategic positioning of the injection molding gate serves as a proactive measure to prevent or alleviate complications stemming from gate size inaccuracies. Incorrect gate placement can lead to various molding imperfections, including injection molding flash, weak areas, fractures, uneven thickness, and more. The judicious selection of the gate’s location in injection molding not only ensures the right gate size but also enhances the timing, thus contributing to the overall process’s efficiency and product quality.
What are The Types of injection molding gates?
Sprue Gate:
The direct sprue gate type is a straightforward and widely used method in injection molding. In this approach, molten plastic directly flows into the mold cavity through the sprue, enabling the rapid injection of substantial plastic volumes. It typically demands lower injection pressure and has a brief feeding time. Direct gates are uncomplicated to design and offer high tensile strength around the gate area.

The simplicity of this gate design makes it a cost-effective choice. However, it’s worth noting that these gates can leave marks on the final parts, as the sprue gate must be manually removed from the injection-molded components by technicians.
The direct gate finds its primary suitability in applications with shell or box-shaped molds, deep single cavities, and non-aesthetic parts. It is commonly employed in the production of household appliances and consumer products such as washing machines, trash bins, TVs, printers, and more.
Tab Gate:
The tab gate is a notable injection molding gate design characterized by its flat and wide structure, making it suitable for specific applications. As the name suggests, this gate type resembles a flat tab or rectangular shape, often located strategically on the part. Its distinctive design ensures efficient plastic flow into the mold cavity while minimizing potential defects.

One of the key advantages of the tab gate is its ability to reduce visible marks on the finished parts, resulting in a cleaner and more aesthetically pleasing product. This attribute makes it particularly attractive for parts where surface quality is paramount. Additionally, the tab gate is well-suited for larger and thicker components, as its design allows for adequate plastic flow, reducing the risk of incomplete filling.
Despite these advantages, it’s important to note that the tab gate may require a higher injection pressure to ensure proper mold cavity filling. Therefore, it is essential to match the gate design with the specific requirements of the project and select the appropriate gate size and placement to optimize the injection molding process.
The tab gate’s versatility makes it an excellent choice for a variety of applications, including those in automotive, consumer electronics, and household appliances. Designers and engineers often consider the tab gate when seeking to strike a balance between ease of production and the aesthetic quality of the final product.
Submarine Gates
The submarine or tunnel injection molding gate is typically situated below the mold parting line, which simplifies the automated trimming process during component ejection. It employs a narrow channel that connects the cavity near the parting line, allowing it to fill the cavity from beneath this line. Additionally, the inclusion of a draft angle ensures the smooth ejection of the final plastic parts without any risk of breakage.

The high-shear nature of this tunnel gate design, however, limits the amount of molten plastic that enters the mold cavity. Consequently, submarine or tunnel gates are best suited for molding small components where precise control is essential. Attempting to use them for larger parts may result in unnecessarily prolonged cycle times and subpar surface finishes due to shear heating effects.
Cashew Gates
Resembling the distinctive shape of a cashew nut, the cashew gate finds its purpose in scenarios where the removal of the gate poses a risk of disfiguring the final product. This gate exhibits a gracefully curved structure, making the extraction of molded parts a delicate task to prevent damage or deformation.

Cashew gates are invaluable when navigating challenging areas within the mold that are otherwise inaccessible using conventional tunnel gates. To facilitate this, injection molding manufacturers often incorporate removable fittings that can be easily detached during the ejection process.
One of the notable attributes of cashew gates is their adaptability to various plastic resins. This gate type isn’t restricted to a specific resin, providing a versatile solution that can be considered to suit the unique requirements of your product designs.
Diaphragm Gates
The diaphragm gate and the sprue gate share a similar visual profile, both tapering away from the gate’s base. These gate types find their niche in the realm of molded parts featuring angular shapes. Despite their visual resemblance, the diaphragm gate excels in reducing the occurrence of weld lines and undesirable geometric irregularities in the final product, although it’s worth noting that the temperature, speed, and pressure parameters of the injection molding process can influence the molded part’s quality.

Diaphragm gates prove their worth in applications involving larger parts that demand a substantial resin volume to complete the molding process effectively. Remarkably versatile, the diaphragm gate design aligns with most resin types, presenting itself as an ideal choice to harmonize with the specific requirements of your product’s design.
Edge Gate:
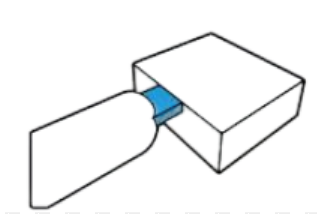
The edge gate stands as one of the most popular and straightforward injection mold gate designs. True to its name, it typically resides along the edge of the workpiece, creating a discernible mark at the point of separation. This design boasts larger cross-sectional areas that facilitate the free flow of molten plastic into the cavity.
Notably, the edge gate is a cost-effective choice for design, making it well-suited for flat parts and those with medium to thick sections. What further enhances its versatility is that edge gates don’t necessitate a specific resin type. This attribute makes them particularly advantageous when aiming to streamline the design for injection molding, as they offer adaptability and efficiency in a wide range of applications.
Hot Runner Gate:
The core concept behind the hot runner mold system lies in maintaining molten plastic in its liquid state until it seamlessly fills the mold with precision. This requires specific temperature and pressure settings to be meticulously controlled. Hot runner valve gates are integral to this process, ensuring uniform pressure and temperature conditions akin to those in the runners. They also retain precise width dimensions consistent with the runners.
What sets the hot runner valve gate apart is its incorporation of ejector pins, providing unparalleled control capabilities. The molten plastic flows into the gate when the pin is retracted and comes to a halt when the pin is pushed back into place.
Moreover, this pin’s retraction and insertion help purge any residual plastic from the front runner system gate, preventing material buildup and thus enhancing overall operational efficiency. The hot runner valve gate stands as a dependable control mechanism throughout the injection process, offering simultaneous individual control over multiple gates.
Hot Runner Thermal Gates:
Hot runner thermal gates, much like their valve gate counterparts, operate under specific temperature and pressure conditions. These thermal gates are exclusive to hot runner systems and are strategically positioned at the top of parts, just above the mold parting line. Unlike some other injection molding gate designs, thermal gates function independently, eliminating the reliance on a runner to facilitate the injection molding process. This design negates the necessity for gate separation from the finished part after molding.
The operation of a hot runner thermal gate distinguishes itself from other gate types, as it lacks pins or valves serving as shut-off mechanisms. Instead, molten plastic flows through the thermal gate onto a valve. The residual plastic left within the hot runner system gate forms a cold slug, often referred to as the ‘thermal gate,’ acting as a temporary barrier once the flow ceases.
Subsequent flows of molten plastic push the thermal gate into the mold, where it melts and merges with the material. Remarkably versatile, the hot runner thermal gate is compatible with a wide range of resin types, rendering it a flexible and suitable choice for a variety of design applications.

Fan Gate:

Fan gates, as the name suggests, are designed in the shape of a fan, featuring a broad opening that allows molten plastic to flow into the mold cavity. These gates gradually widen, forming a fan-like shape that extends from the runner towards the mold cavity, ensuring uniform thickness. They are frequently employed to establish a consistent flow, particularly in the production of larger parts.
The implementation of a fan gate serves a dual purpose, effectively mitigating injection molding defects while preserving the dimensional stability of the parts. Moreover, fan gates excel in the fabrication of flat and thin products, as they are adept at minimizing directional stress and preventing unsightly flow marks. This gate type is particularly well-suited for use with polycarbonate plastics.
Pin Gate:
Pin gates are typically positioned on the B-side of the mold near the ejector pins. These gates find their optimal application in three-plate molds where the runner channel is segregated into a distinct runner plate, causing the mold flow to diverge in various directions before entering the cavity through multiple gate locations. The pin gate is characterized by its minuscule gate point, which is conveniently removed during the injection mold’s opening sequence.
However, one of the drawbacks of the pin gate design lies in its relatively larger runner, which contributes to a higher scrap rate. This is a notable disadvantage associated with the use of pin gates.

How to choose a gate type?
Different injection gate types are suitable for various applications and product requirements. When selecting a gate type, factors such as appearance, waste, production efficiency, and cost need to be considered. Choosing and designing the right gate ensures the production of high-quality plastic products. By understanding these different injection gate types, you can make better choices for your injection molding needs, improving product quality and efficiency.
If you are unsure which gate type to choose, consult with us
Sino-Mold Industrial Co., Ltd. Email: louise@sino-mold.com
In the field of injection molding, gates are a crucial element, and the selection of the appropriate gate type directly impacts product quality and production efficiency. We hope this article has been helpful and that you will be better equipped to choose and design gates for your future injection molding projects. If you have any questions or need further assistance regarding injection gate types, please feel free to contact us.