Introduction
Injection molding is a widely used manufacturing process that allows for the mass production of intricate plastic parts with high precision. However, even in this highly controlled environment, imperfections can occur. One common issue faced by manufacturers is the presence of burrs, or excess material, on the edges of molded products. These burrs can compromise the quality, functionality, and aesthetic appeal of the final product. Understanding the causes of burrs and how to prevent them is crucial for maintaining high standards in production and ensuring customer satisfaction.
In this article, we will explore the various reasons why burrs occur in injection molding and provide practical solutions for minimizing their occurrence.
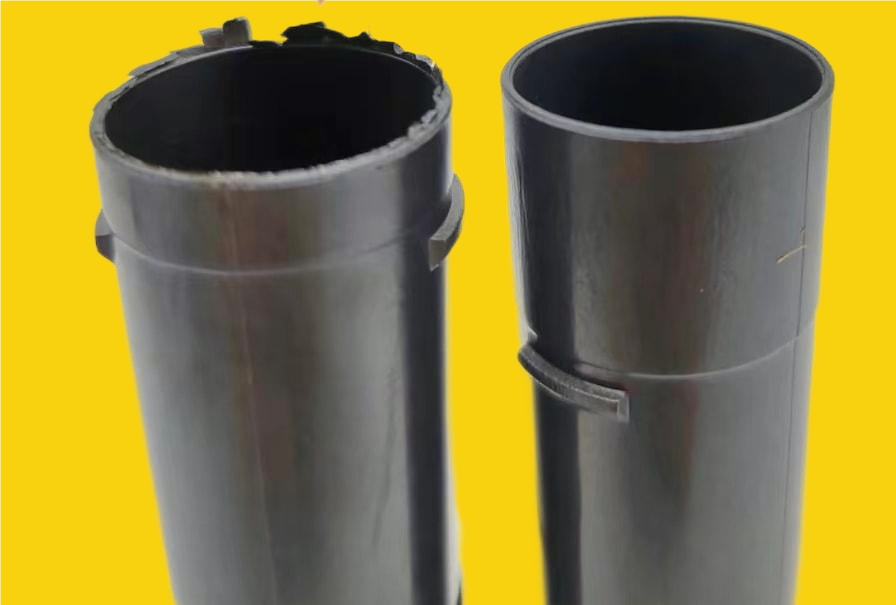
I. Understanding Burrs in Injection Molded Products
Burrs, or flash, are unwanted excess material found on the edges of injection molded products. The molding material can contribute to burr formation when it protrudes at the edges of components during the molding process. These imperfections can impact the aesthetic, functionality, and quality of the final product. Addressing the presence of burrs is crucial for maintaining high standards in manufacturing and ensuring customer satisfaction.

II. Causes of Burrs in the Injection Molding Process
- Mold Problem: Burrs can result from design or manufacturing flaws in the mold cavity. Gaps, misalignment, or worn-out mold parts can cause excess material to escape during the injection process. The molding material can escape through these gaps or misalignments, leading to burr formation.
- Injection Molding Process Issues: Incorrect parameters such as temperature, pressure, and injection speed can lead to injection molding defects like burr formation.
- Injection Molded Parts Defects: Injection molded parts can exhibit defects such as burn marks and jetting. These issues often arise from improper mold design, material use, or process parameters.
- Injection Molding Machine Equipment Problems: Equipment malfunctions or wear and tear can cause inconsistencies in the molding process, leading to burrs. Issues with the injection machine, such as poor mold parallelism and imbalanced clamping, can also contribute to these defects.
- Importance of Injection Nozzle: The injection nozzle plays a crucial role in preventing defects like delamination by reducing the reliance on release agents and ensuring proper mold design.
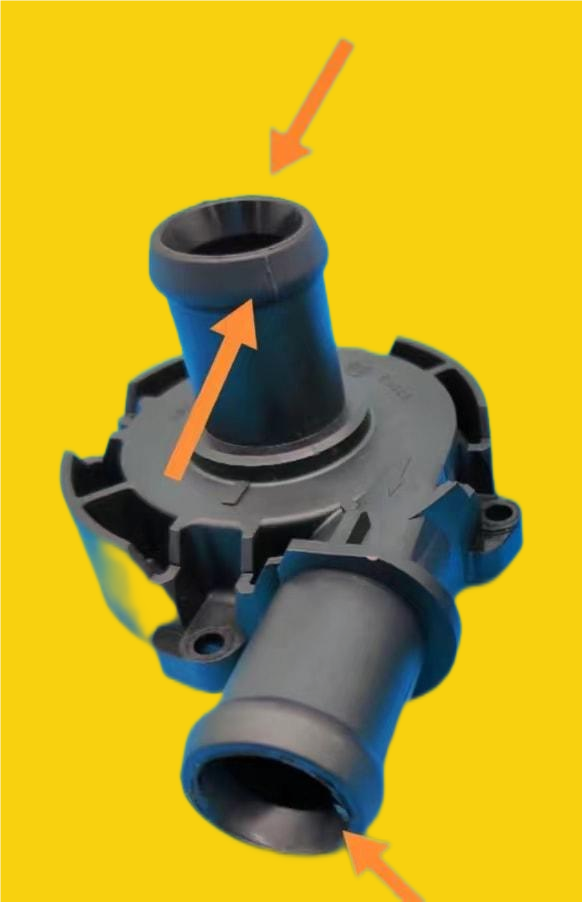
- Plastic Fluidity is Too Good: Highly fluid plastics can seep into small gaps in the mold, resulting in burrs.
- Too Much Melt Injected: Overfilling the mold with molten material can cause excess material to escape and form burrs.
- Low-Pressure Molding Solution: Low-pressure molding can help prevent burrs and unwanted flow lines in molded components by using fluid plastic effectively.
- Mold Surface Has Foreign Matter: Contaminants on the mold surface can interfere with the molding process, causing burrs.
- Caused by Mold Deflection: Uneven pressure or force can cause the mold to deflect, creating gaps where material can escape.
- Insufficient Clamping Force Compared: Inadequate clamping force compared to the projected area of the molded part can prevent the mold from closing tightly, allowing material to leak out and form burrs.
- The Mold is not Closed Tightly: Misalignment or mechanical issues can prevent the mold from closing properly.
- Mold Wear: Over time, molds can wear out, leading to gaps and misalignments that cause burrs.
- Injection Pressure is Too High: Excessive injection pressure can force molten plastic into unwanted areas, creating burrs.
- Material Temperature is Too High: Overheating the material can increase its fluidity, causing it to seep into gaps. Adjusting the mold temperature can help prevent defects like burn marks and flash.
- Part of the Mold is not Tight: Any loose parts in the mold assembly can create spaces for material to escape.
- Mold Clamping Surface Cleanliness: Keeping the mold clamping surface clean is essential to prevent the production of burrs and ensure close adherence of the clamping surface.
III. Troubleshooting Burrs Problems
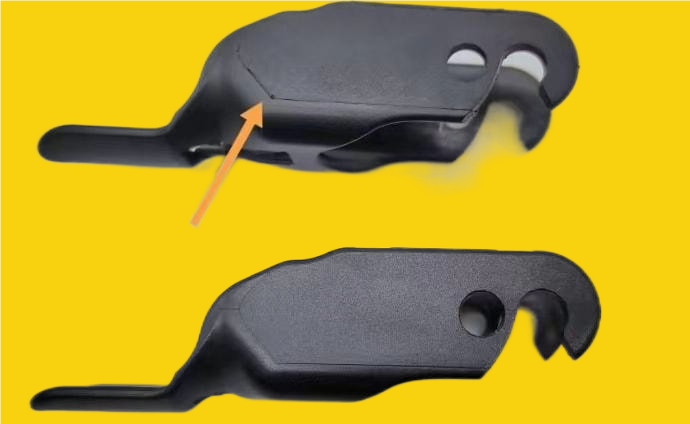
- Optimize Mold Structure: Ensure that the mold design is precise and free from flaws that could cause burrs.
- Adjust the Injection Molding Process:Fine-tune parameters such as temperature, pressure, and injection speed to minimize burr formation.Accurately measure the molding material to prevent excess material from forming burrs.
- Clean or Maintain Equipment:Regular maintenance and cleaning of equipment can prevent malfunctions and contamination.
- Adjust Mold Closing Height:Ensure the mold closes completely and evenly to prevent material leakage.
- Replace the Mold:If the mold is worn out or damaged, replacing it can eliminate burr issues.
- Reduce Injection Pressure:Lowering the injection pressure can prevent material from escaping into unwanted areas.
- Lower the Material Temperature:Reducing the temperature of the material can decrease its fluidity, reducing the risk of burrs.
- Adjust Mold Design:Modify the mold design to eliminate gaps and ensure a tighter fit.
- Optimize Process Parameters:Continuously monitor and adjust process parameters for optimal performance.
III. Troubleshooting Burr Problems: Mold Temperature Considerations
1. Manual Deburring: Skilled workers manually remove burrs using tools. The type of molding material can influence the effectiveness of manual deburring techniques.
2.Mold Deburring:Incorporate features in the mold design that facilitate burr removal.
3.Grinding and Deburring:Use grinding machines to smooth out edges and remove burrs.
4.Freezing Deburring:Use low temperatures to make burrs brittle and easy to remove.
5.Thermal Deburring:Apply heat to burn off burrs.
6.Engraving Machine Deburring:Use precision engraving machines to remove burrs.
7.Chemical Deburring: Apply chemicals to dissolve burrs.
8.Electrolytic Deburring: Use electrolytic processes to remove burrs.
9.High-Pressure Water Jet Deburring: Use high-pressure water jets to clean off burrs.
10.Ultrasonic Deburring: Apply ultrasonic waves to remove burrs efficiently.
V. Importance of Quality Control
Implementing robust quality control measures is essential to detect and address burrs early in the production process. Monitoring the molding material during quality control inspections is crucial to detect and address burrs early. Regular inspections, coupled with advanced technology, can ensure that products meet the highest standards of quality.
VI. Conclusion
Burrs in injection molded products can arise from various causes, including mold issues, process parameters, and equipment problems. By understanding these causes and implementing effective troubleshooting and advanced deburring techniques, manufacturers can produce high-quality, burr-free products. Controlling the molding material is crucial in preventing burrs, as accurate measurement and management of the material can minimize excess protrusions at the edges of components.
At Sino-Mold Industrial Co., Ltd., we are committed to delivering precision-engineered solutions that meet the highest standards of quality and performance. If you have any questions or need assistance with your projects, feel free to reach out to us. sales@sino-mold.com/louise@sino-mold.com
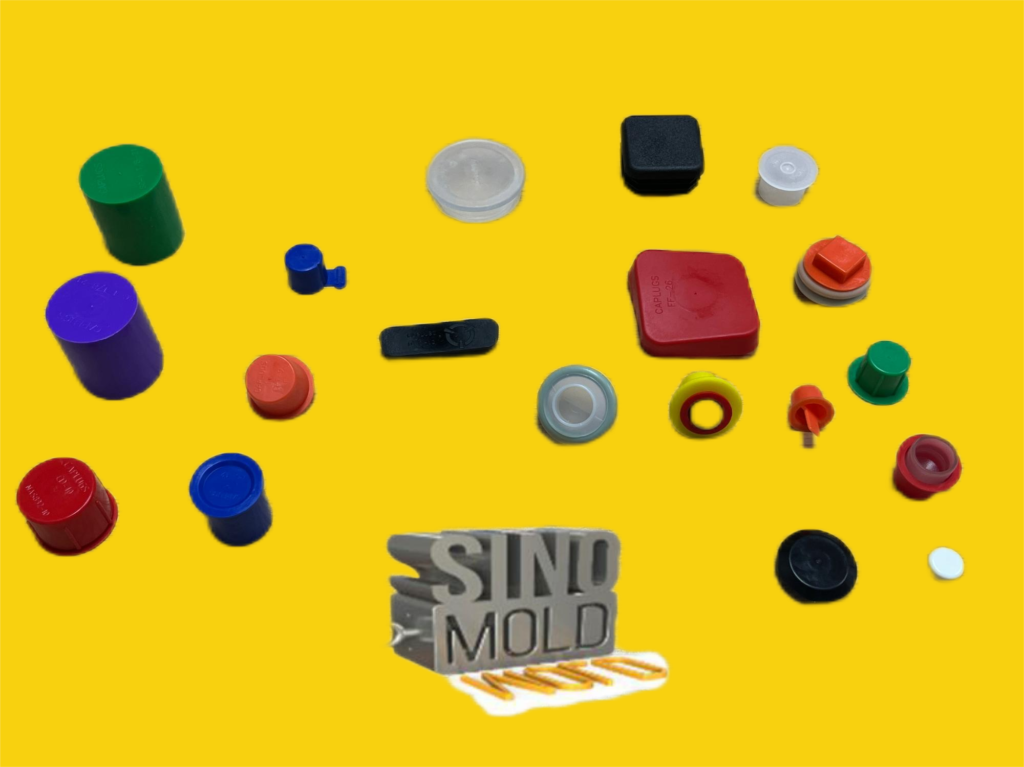