Injection molding is a widely used manufacturing process for producing plastic parts. Ejector plates play a critical role in this process by controlling the ejection of parts and maintaining the performance of ejector pins. However, one common issue that can disrupt production and increase costs is the frequent breakage of ejector pins. Ejector pins, also known as knockout pins, are crucial components that help remove the molded part from the mold after the injection process. Understanding the various parameters of the molding cycle is crucial in identifying the root causes of ejector pin breakage. When these pins break frequently, it can lead to downtime, increased maintenance, and higher production costs. This article explores the potential causes of frequent ejector pin breakage and offers solutions to mitigate the problem.
1. Understanding Ejector Pins in Injection Molding

Ejector pins are a crucial component in the injection molding process, playing a vital role in ensuring the smooth ejection of molded parts from the mold. These pins are strategically placed within the mold to facilitate the efficient removal of the part, minimizing the risk of damage or deformation. The design and material selection of ejector pins are critical factors in determining their performance and longevity.
In injection molding, ejector pins are typically made from high-strength materials, such as stainless steel or tool steel, to withstand the high pressures and temperatures involved in the molding process. The pins are designed to be durable and resistant to wear and tear, with a smooth surface finish to minimize friction and prevent damage to the molded part.
The ejector pin’s outer diameter and length are critical parameters that must be carefully considered to ensure proper fit and function within the mold. The pin’s surface finish and material selection also play a crucial role in minimizing ejector pin marks and ensuring a smooth ejection process. By paying close attention to these factors, manufacturers can enhance the efficiency and reliability of their molding process, reducing the likelihood of defects and downtime.
Frequent Ejector Pin Breakage in Injection Molding: Causes and Solutions
1. Improper Pin Alignment

One of the primary reasons for ejector pin breakage is improper alignment. If the pins are not aligned correctly with the mold, they can experience uneven stress during the ejection process, leading to bending or breakage. Misalignment can occur due to poor mold design, incorrect installation, or wear and tear over time.
Proper alignment and maintenance of the ejector housing are essential to prevent misalignment and ensure the smooth operation of ejector pins.
Solution: Ensure that the ejector pins are properly aligned during the mold design and installation phases. Regularly inspect the mold for signs of wear and misalignment, and make necessary adjustments. Precision tools and alignment guides can help maintain proper alignment, which is a key part of a well-designed and functional mold.
2. Insufficient Pin Strength

Ejector pins are subjected to significant force during the ejection process. If the pins are not strong enough to withstand this force, they may break. The strength of the ejector pins depends on the material used and their diameter. The interaction between core pins and ejector pins must be carefully considered to ensure the overall strength and performance of the ejection system.
Solution: Choose ejector pins made from high-strength materials, such as hardened steel or carbide, which can withstand the stresses of the ejection process. Additionally, consider increasing the diameter of the pins to enhance their strength, provided that the mold design allows for it.
At Sino-Mold, we ensure that our ejector pins are crafted from top-quality materials to handle the demands of your production process, helping to minimize the risk of breakage.
3. Excessive Ejection Force
Applying too much force during the ejection process can cause the ejector pins to break. Excessive ejection force can also lead to pin push marks, which occur due to the forces exerted by ejector pins during the part’s removal from the mold. This can happen if the molded part is sticking to the mold due to insufficient draft angles, improper cooling, or inadequate release agents.
Using mold release agents can help reduce the force required for ejection by minimizing friction between the part and the mold.
Solution: Optimize the mold design to include appropriate draft angles, which facilitate easier ejection of the part. Ensure that the cooling system is functioning correctly to prevent the part from sticking to the mold. Additionally, using release agents can help reduce friction between the part and the mold.
4.Fatigue and Wear Due to Mold Temperature
Ejector pins are subject to repeated stress cycles, which can lead to fatigue and eventual breakage. Over time, the pins may develop cracks or other signs of wear, especially if they are not properly maintained. The design and maintenance of the ejector plates are crucial in minimizing wear and extending the longevity of ejector pins.
Solution: Implement a regular maintenance schedule to inspect and replace worn or damaged ejector pins. Surface treatments like nitriding or coating can also enhance their durability, making them more resistant to wear.
5.Contamination and Corrosion in Ejector Pin Holes
Contaminants, such as dirt, debris, or moisture, can accumulate in the mold and cause corrosion or damage to the ejector pins. Corrosion weakens the pins, making them more susceptible to breakage.
Regular maintenance of the molding machine is essential to ensure the cleanliness and optimal performance of ejector pins.
Solution: Keep the mold and ejector pins clean and free from contaminants. Regularly clean the mold and apply anti-corrosion treatments to the pins if necessary. Ensure that the molding environment is controlled to minimize exposure to moisture and other corrosive elements.
Design and Material Considerations for Ejector Pins
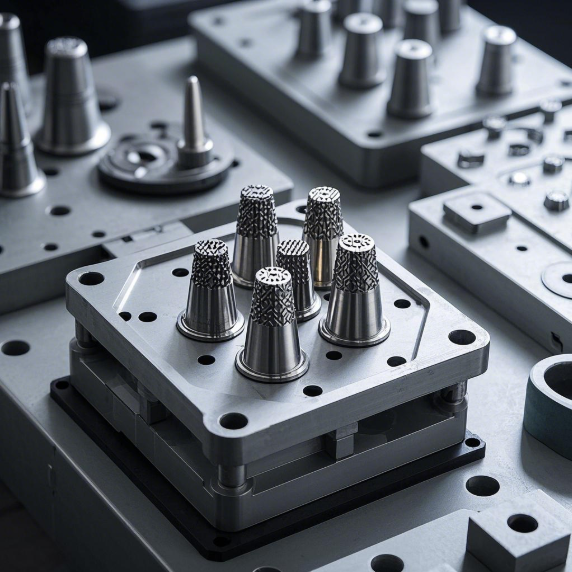
When designing ejector pins for injection molding, several key factors must be considered to ensure optimal performance and longevity. The pin’s material selection, surface finish, and design geometry are all critical parameters that can impact the molding process and final product quality.
Material selection is a critical consideration, as the ejector pin must be able to withstand the high pressures and temperatures involved in the molding process. Common materials used for ejector pins include stainless steel, tool steel, and copper alloys, each offering unique benefits and drawbacks. Stainless steel is known for its corrosion resistance, while tool steel provides excellent hardness and wear resistance. Copper alloys, on the other hand, offer superior thermal conductivity.
The surface finish of the ejector pin is also an important consideration, as a smooth finish can help minimize friction and prevent damage to the molded part. A low surface roughness value, typically in the range of 2-10 microinches, is recommended to ensure a smooth ejection process. This helps in minimizing ejector pin marks and ensuring the aesthetic quality of the final product.
In addition to material selection and surface finish, the design geometry of the ejector pin is also critical. The pin’s outer diameter and length must be carefully considered to ensure proper fit and function within the mold. A uniform cooling system and ejection system can also help minimize ejector pin marks and ensure a smooth ejection process. By optimizing these design and material considerations, manufacturers can improve the durability and efficiency of their injection molding operations.
Ejector Pin Maintenance and Troubleshooting
Ejector pin maintenance is crucial to ensure the longevity and optimal performance of the injection molding process. Regular maintenance can help prevent ejector pin breakage, reduce downtime, and improve overall product quality. Here are some tips for ejector pin maintenance and troubleshooting:
1.Regular Cleaning: Clean the ejector pins and surrounding areas regularly to prevent dirt and debris buildup. Use a soft brush or cloth to remove any debris, and avoid using harsh chemicals that can damage the pins.
2.Lubrication: Apply a suitable lubricant to the ejector pins to reduce friction and wear. Choose a lubricant that is compatible with the material being molded and the operating temperature of the mold.
3.Inspection: Regularly inspect the ejector pins for signs of wear, damage, or corrosion. Check for any scratches, dents, or rust, and replace the pins if necessary.
4.Alignment: Ensure that the ejector pins are properly aligned with the mold cavity. Misaligned pins can cause uneven ejection, leading to product defects.
5.Ejector Pin Replacement: Replace ejector pins that are damaged or worn out. Use high-quality replacement pins that meet the original specifications.
Common issues that may require troubleshooting include:
1.Ejector Pin Breakage: Check for excessive force, misalignment, or inadequate lubrication.
2.Ejector Pin Marks: Check for improper ejector pin design, inadequate lubrication, or incorrect mold temperature.
3.Ejector Pin Sticking: Check for inadequate lubrication, misalignment, or excessive force.
By following these maintenance and troubleshooting tips, you can minimize ejector pin-related issues and ensure optimal performance of your injection molding process.
Minimizing Ejector Pin Marks and Optimizing Performance
Ejector pin marks can be a significant issue in injection molding, affecting the aesthetic quality and functionality of the final product. To minimize ejector pin marks and optimize performance, consider the following strategies:
1.Optimize Ejector Pin Design: Design ejector pins with a smooth, rounded surface to reduce the risk of marks. Use a pin with a smaller outer diameter to minimize the contact area.
2.Use Mold Release Agents: Apply mold release agents to the ejector pins and mold cavity to reduce friction and prevent sticking.
3.Adjust Mold Temperature: Optimize the mold temperature to reduce the risk of ejector pin marks. A uniform cooling system can help prevent uneven cooling, which can lead to marks.
4.Use Ejector Pin Holes: Use ejector pin holes with a smooth, rounded surface to reduce the risk of marks. Ensure that the holes are properly aligned with the ejector pins.
5.Optimize Injection Pressure: Adjust the injection pressure to minimize the force applied to the ejector pins. Excessive pressure can cause marks and damage to the mold.
6.Use a Uniform Cooling System: Implement a uniform cooling system to prevent uneven cooling, which can lead to ejector pin marks.
7.Monitor Ejector Pin Wear: Regularly inspect the ejector pins for signs of wear and replace them as needed. Worn-out pins can cause marks and affect product quality.
Conclusion
Frequent ejector pin breakage in injection molding can be a significant problem, but it is often preventable with proper design, maintenance, and operational practices. By addressing issues such as improper alignment, insufficient pin strength, excessive ejection force, fatigue, contamination, and incorrect pin length, manufacturers can reduce the incidence of ejector pin breakage and improve the efficiency and reliability of their injection molding processes.
At Sino-Mold, we provide expertise in designing and manufacturing molds that are optimized for durability and efficiency. Whether you need guidance on ejector pin issues or are looking for high-quality mold solutions, we are here to support your production needs.Please contact us at sales@sino-mold.com/louise@sino-mold.com.
