Plastic injection molds are crucial in the manufacturing process of plastic products. In this article, we will cover their definition, advantages and disadvantages, manufacturing process, and cost factors. Additionally, we will address the common concern of the cost of purchasing plastic injection molds.
Plastic injection molds are used to produce high-quality plastic products with precision and speed. However, they have their drawbacks, such as high initial costs and longer lead times. The manufacturing process involves several steps, including design, machining, and testing. The cost of a plastic injection mold is influenced by factors such as size, complexity, and material used.
In this article, we aim to provide a concise overview of plastic injection molds, their benefits and drawbacks, and the cost factors that should be considered. By the end of this article, readers will have a better understanding of plastic injection molds and be better equipped to make informed decisions when considering them for their own products.
What is plastic mold?
Plastic mold is a tool for manufacturing plastic products. It is industrial equipment for producing a large number of plastic products, usually made of metal makings, such as steel or aluminum alloy.
The plastic mold usually consists of two or more parts, each of which has a specific shape and function. In which one part is the “core” of the mold and the other part is the “cavity” of the mold, which correspond to the internal and external shapes of the product respectively. When the molten plastic is injected into the mold, cooled and solidified in it, the molded plastic product can be taken out.
Various kinds of plastic molds are available, and different molds are suitable for the production of
different types of plastic products, such as automobile parts, household appliances, plastic bottles,
electronics parts and so on. Plastic injection mold manufacturing has become a very important industry because widely used in life and many industry.

www.sino-mold.com
Pros of Plastic Molds
High production efficiency: mass production can be realized by using the mold, and a large number of plastic products with the same shape and size can be manufactured at one time, thus improving production efficiency.
High product quality: the size and shape of the die products are accurate, which can meet the requirements of high-precision production and ensure the product quality.
Low cost: Compared with manual production, the use of molds can reduce the manufacturing cost. The mold can be made once and used many times, and the production speed of mold products is fast, which can reduce the labor cost.
Strong repeatability: the mold can be used for many times, with strong repeatability, improving production efficiency and reducing manufacturing cost.
A variety of materials are acceptable: the mold can match a variety of different plastic materials, so that different kinds of plastic products can be produced.
Supporting automated production: the use of plastic molds can be used in conjunction with automated production equipment to achieve an efficient, accurate and automated production process.
Cons of Plastic Molds
Long manufacturing cycle: Mold manufacturing requires design, processing and debugging, and the manufacturing cycle is relatively long, which may take weeks or even months.
High manufacturing cost: It takes a lot of time, manpower and material resources to manufacture the mold, and the cost is high.
High design requirements: the design requirements of the mold are very high, requiring precise design and processing, as well as the technology and equipment of the manufacturer.
Need maintenance: the mold needs maintenance to ensure its quality and performance will not be affected. Otherwise, the service life of the mold may be shortened and the cost will be increased.
In conclusion, although plastic molds have some shortcomings, they are widely used in the field of plastic products production because of their advantages such as high production efficiency, high product quality and low cost.
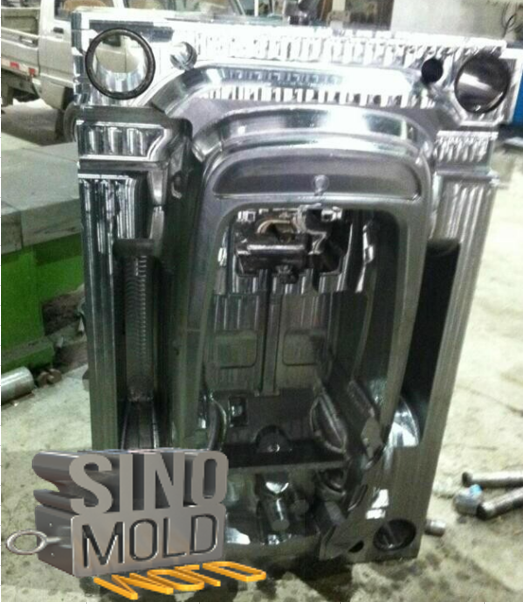
How to make Plastic Injection Mold ?
Design: the design of the plastic injection mold is the first step of this process. The design is usually created using computer-aided design (CAD) software and is based on the product to be manufactured.
Mold base: Mold base is the basis of the injection mold. It is made of a high-strength steel alloy, including cavities, cooling channels and the injection system.
Machining: the mold base is machined using a variety of tools, such as CNC milling machines and lathes. The goal is to create the mold cavities and cooling channels according to the required specifications.
Heat treatment: the die holder is subjected to heat treatment to increase its hardness and durability. This process includes heating the mold base to a specific temperature, and then slowly cooling.
Mold assembly: once the mold base is ready, the mold assembly process begins. This includes the assembly of the mold cavities, cooling channels and the injection system.
Mold trial: before the mold is put into production, it must go through the mold trial process. This includes injecting plastic into the mold to check for any defects or problems.
Production: Once the mold is considered suitable for production, it will be used to make plastic products.
Maintenance: Regular maintenance and cleaning of the injection mold are very important to ensure its life and best performance.
Our Service Flow:

What are the materials of plastic molds?
They are many kind of option for plastic injection mold material .
Depends on the mold life and plastic material and so on, we can choice different mold steel. Such as :
Tool steel: Tool steel is like a superhero alloy steel with super strength and hardness, that helps to make high-precision molds in the industrial world. It’s wear-resistant, can durable withstand high temperatures and also fights off corrosion like a champ! It’s the go-to material for most plastic injection molds.
Stainless steel: Stainless steel is a cool steel material that doesn’t rust easily and has amazing superpowers of corrosion resistance and chemical stability. It’s perfect for making small and medium-sized plastic molds that need to be super precise, like molds for electronic stuff or medical gadgets.
Aluminum alloy: Aluminum alloy is like a superhero that is light and resistant to corrosion. It’s great at conducting heat and is easily workable. It’s perfect for making molds for larger and simpler plastic products like car parts, household appliances and more.
Beryllium bronze: Beryllium bronze is a type of alloy that contains beryllium as the main component, with copper as a secondary component. It is known for its high strength, hardness, and resistance to wear and corrosion, making it a popular material for use in plastic injection molds.
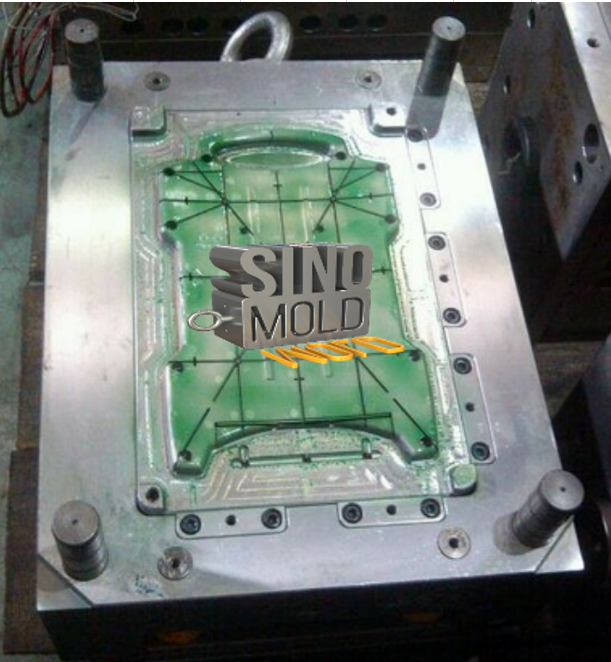
So, depending on the injection products and production needs, other materials can be used to get the best quality and production effect. And when making the molds, it’s important to consider the material’s characteristics like wear resistance and process ability to ensure that the whole injection process is stable and reliable.
Different Hardness Levels of Mold Components
Mold components typically have different levels of hardness, depending on the material used and the required application. Generally, mold components need to have high hardness and wear resistance to withstand high pressure and friction during the production process. Common mold materials such as tool steel and stainless steel have high hardness and wear resistance. In addition, some special surface treatment methods such as nit riding and carbonizing can improve the hardness and wear resistance of mold components, thereby extending their service life.

What are the main plastic mold systems?
Normally when the part ‘s production Quantities is not big, and the design is simple. Most of the mold will use cold runner.
But for some part design, also need perfect outlook, big quantities production etc. Now we will use hot runner for the mold system.
Hot Runner System: The hot runner system is an advanced plastic injection mold system that uses heating elements inside the mold to melt and maintain the plastic at a high temperature, allowing for more even filling of the molds. The hot runner system is typically used in production settings where high-quality appearance and dimensional accuracy of plastic products are required.
Cooling System: The cooling system is used to control the temperature of the molds and cool the plastic. It includes cooling channels inside the mold and an external cooling water system. By controlling the flow and temperature of the cooling water, the mold temperature can be controlled to achieve the desired plastic solidification speed and shrinkage rate.
Switching System: The switching system is a system that can produce plastic products of different sizes and shapes on the same injection molding machine. It achieves this by replacing different modules in the mold to produce different products. It has the advantages of high production efficiency and wide applicability.
Core System: The core system is a component in the mold that forms the hollow parts of the product and is typically used in molds for producing hollow plastic products. The core system typically consists of removable cores and mold bases, and the molten plastic is injected into the core during the injection molding process to form the hollow parts of the product.
In general, different plastic mold systems can be selected based on the requirements of the injection molded product and production needs to achieve the best production efficiency and product quality. Additionally, in the design, manufacture, and maintenance of molds, it is also necessary to consider the coordination and adjustment between different systems to ensure the stability and reliability of the entire injection molding process.

How do plastic molds produce products?
Plastic molds are used to manufacture plastic products by shaping molten plastic into a desired form. After the mold is designed and manufactured:
Prepare the plastic: The plastic is typically prepared by melting it in a heating chamber until it becomes molten. The plastic is then injected into the mold using a specialized injection molding machine.
Cool the plastic: Once the plastic has been injected into the molds, it is cooled to allow it to solidify and take on the shape of the mold. This process can be accelerated by using cooling systems, such as water or air cooling.
Remove the product: Once the plastic has cooled and solidified, the product is removed from the mold. The molds can then be cleaned and reused to produce more products.
Finish the product: Depending on the product being produced, additional finishing steps may be required, such as trimming excess plastic or adding surface textures or markings.
The process of using plastic molds to produce products is highly efficient and widely used in various industries, including automotive, electronics, medical, and consumer goods.
What is temperature control in plastic injection molding?
Temperature control of the mold used for cooling is one of the critical steps in the plastic injection molding process. It has a significant impact on the quality of the product and the production efficiency.
In plastic injection molding, the mold dissipates heat through cooling water, allowing the plastic to form the required shape in the mold. Therefore, temperature control of the mold is essential, directly affecting factors such as shrinkage rate, dimensional accuracy, and surface quality of the product.
Temperature control of the mold can be achieved through the following methods:
Cooling water channel design: By designing a reasonable cooling water channel, cooling water can flow evenly inside the mold, achieving an effective cooling effect.
Temperature control system: A temperature control system installed on the mold can monitor the mold’s temperature in real-time and adjust the mold’s temperature by controlling the flow and temperature of the cooling water.
Cooling water quality control: Ensuring the quality and flow rate of cooling water can effectively control the mold’s temperature and prevent temperature fluctuations caused by factors such as scale and impurities.
In summary, temperature control of the mold is a critical aspect of injection molding production. Through reasonable design and control, it can improve product quality, production efficiency, and reduce production costs.
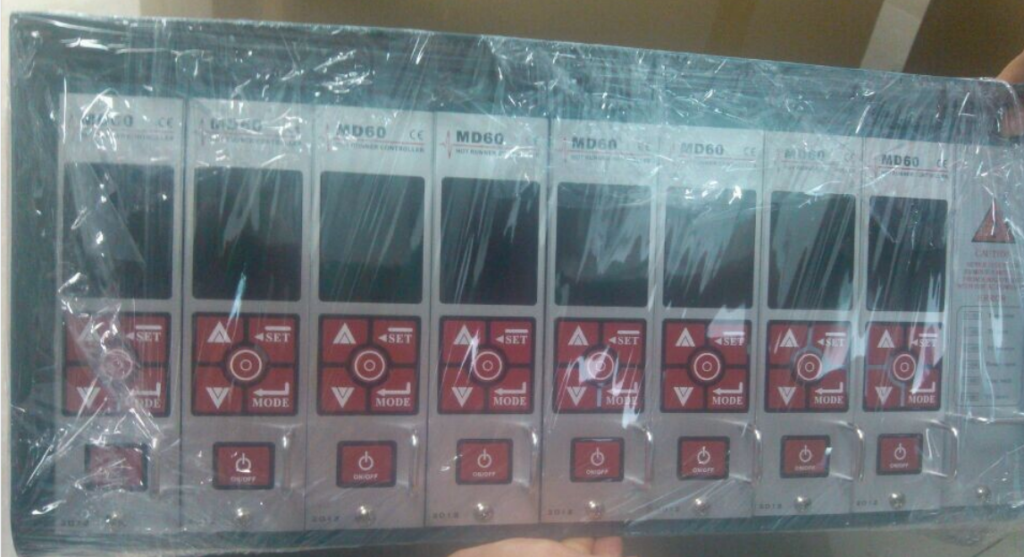
Factors affecting plastic injection mold design
The width and cooling channel diameter of plastic injection molds are crucial in determining the quality of the final product. A wider mold requires a larger cooling channel diameter to ensure effective cooling. A larger cooling channel diameter improves the cooling effect, but excessive diameter can lead to increased manufacturing difficulty and cost. In designing the mold, the width and cooling channel diameter should be determined based on the specific injection product and production requirements for optimal efficiency. During manufacturing, precision and smoothness of the cooling channel diameter must be strictly controlled to prevent hot spots and defects.
The cost of the mold depends on what?
Size and complexity: the greater the size and complexity of the mold, the higher the manufacturing difficulty and cost. This is because large and complicated molds need more makings and longer processing time.
Material type and quality: the choice and quality of mold makings directly affect the manufacturing cost of mold. Commonly used die makings are steel, aluminum, copper, titanium alloy, etc. Different makings have different prices and different qualities.
Manufacturing technology and equipment: Mold manufacturing technology and equipment also have a direct impact on cost. Mold manufacturing requires sophisticated processing and testing equipment, and the price of these equipment will also affect the cost.
Quantity and manufacturing cycle: the number of molds and manufacturing cycle are also factors affecting the cost. The cost of manufacturing multiple molds at a time will be lower than that of manufacturing one mold alone. At the same time, the manufacturing cycle will also affect the manufacturer’s cost calculation.
Technology and maintenance costs: Some complicated molds need more advanced technology and more maintenance costs, which will also affect the cost.
Impact of Size and Complexity on Plastic Parts Production
The size and complexity of plastic parts affect the production process and cost. Small and simple parts can be produced in a single mold resulting in low cost, while medium-sized and moderately complex parts require more processing and tools resulting in higher cost. Large and highly complex parts require special molds and more production steps, making the production cost very high. Choosing the right production method and material can make the process more efficient and cost-effective.

Does the injection mold cost a lot?
When you read this, you may have doubts: since plastic molds are widely used and the production process seems complicated, do I need to spend a lot of money to buy them?
Although the initial cost of injection molds may be high, these costs can be amortized over the production volume during the production cycle. Compared with other production methods, injection molding can typically produce larger batches, thereby reducing the cost per part.
For one thing, injection molds are an investment, not just a cost. Once purchased, you can enjoy long-term benefits in future production cycles, reducing the need to purchase new molds again. This saves you costs and improves your production efficiency.
For another thing, injection molding can usually produce higher quality products compared to other production methods. Due to the high pressure and high temperature used in injection molding, products with higher density, tighter structure, and smoother surface can be produced. The improvement in product quality can be reflected in the final product, increasing customer satisfaction and improving your reputation.
In addition,the plastic injection molding is one of the cheapest and most cost-effective manufacturing forms if you look at the unit price. During injection molding, it is important to remember that the more products you produce with molds, the cheaper the price of each product. While the start-up cost of mass production may be high, as the production continues, the price of the project will get better and better.
Finally, when you choose to purchase injection molds, you must want to work with a reliable supplier. Establishing a good relationship with your supplier can improve production efficiency and ensure your orders are delivered on time. We are start business in 1999 for the 1st factroy. Now have more than 20years experience.
Therefore, when considering the purchase of injection molds, don’t just focus on the cost, but consider their value and potential long-term returns. If you need more information or have any questions, please don’t hesitate to contact us. We are glad to help you understand the cost and value of injection molds.

Final Thoughts
As a professional mold making company, so we try our best to share knowledge in plastic mold. When you have rigorous and rich knowledge of the mold, the impact on the quality of production and operation is immeasurable.We clearly understand what time and quality mean to our customers. If you have never tried to import molds from China, you can contact us and we will definitely give you what you really need.
If you want to know more about plastic mold and molding tech., please follow us.
Please feel free to post your thoughts and comments in the comment box.
Request A Free Quote Now Sales@sino-mold.com !
Sino Team is here always for you!