In the plastic injection molding industry, boosting production efficiency and capacity is a paramount objective. Multi-cavity mold design is a key method for achieving this goal. It can significantly increase production speed, lower manufacturing costs, and deliver more products in a shorter timeframe. This article delves into the importance, advantages, design principles, and successful real-world applications of multi-cavity mold design.
What is a Multi-Cavity Mold?
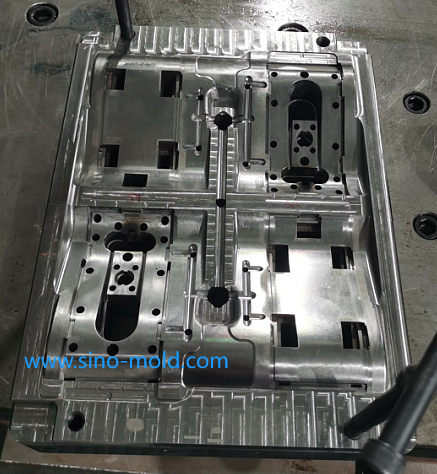
A multi-cavity mold is an injection mold with multiple cavities, each capable of simultaneously producing a single product. This means that multiple identical or similar parts can be manufactured concurrently within a single injection cycle. Multi-cavity molds are typically employed for the mass production of identical or similar components, such as plastic bottles, cutlery, medical equipment parts, and more.
Advantages of Multi-Cavity Molds
Multi-cavity mold design offers several advantages that make it an indispensable tool in the manufacturing process:
Enhanced Productivity: Multi-cavity molds enable the production of multiple parts within a single injection cycle, significantly increasing productivity. This is crucial for meeting high-volume demands.
Cost Reduction: By reducing labor costs and material waste, multi-cavity molds can lower manufacturing costs, ultimately improving production efficiency.
Consistent Product Quality: Multi-cavity molds ensure uniform quality and specifications for every product, reducing variations and defects.
Time Savings: Multi-cavity molds shorten production cycles since multiple parts are manufactured simultaneously, saving time.
Competitive Edge: Multi-cavity molds allow manufacturers to fulfill large batch orders rapidly, giving them a competitive edge in the market.
Practical Applications of Multi-Cavity Molds
Multi-cavity mold designs have found wide-ranging applications across various industries, revolutionizing production processes and enabling manufacturers to meet the demands of high-volume manufacturing. Here are some real-world applications:
Bottle Production: Multi-cavity molds have become the backbone of the plastic beverage bottle manufacturing industry. They facilitate the high-speed production of standardized plastic bottles for a wide range of beverages, from water to carbonated drinks and juices. These molds are optimized to produce consistent bottle dimensions, ensuring compatibility with bottling and packaging equipment.

Medical Equipment Components: Multi-cavity molds play a crucial role in the production of precision medical equipment components. From syringe barrels to intricate instrument parts, multi-cavity molds enable manufacturers to achieve high-quality, high-precision, and high-volume production. This ensures that medical devices meet stringent quality and safety standards.

Household Products: A multitude of everyday household items, such as plastic chairs, tables, storage containers, and kitchenware, are efficiently manufactured using multi-cavity molds. These molds are designed to produce a range of household products quickly and consistently, allowing manufacturers to meet market demands.
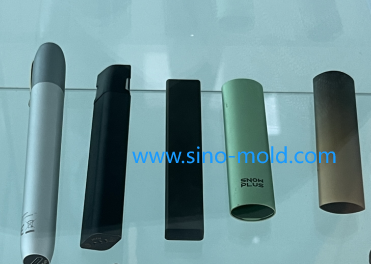
Electronic Device Housings: Multi-cavity molds are the preferred choice for producing casings and enclosures for electronic devices. Whether it’s a smartphone, tablet, or other consumer electronics, these molds ensure uniform appearance and precise dimensions. This uniformity is critical not only for the aesthetics of the product but also for its functionality and ease of assembly.

Conclusion
In the realm of mold design and manufacturing, multi-cavity mold design is a game-changer. It plays a pivotal role in boosting production efficiency, reducing costs, and ensuring product quality. By adhering to the outlined design principles, manufacturers can achieve efficient multi-cavity injection molding machine manufacturing to meet the demands of high-volume production and gain a significant competitive edge in the market.
Design Principles for Multi-Cavity Molds
To harness the full potential of multi-cavity molds and ensure their effectiveness, adhering to several critical design principles is essential:
Uniform Filling: It’s paramount to ensure that each cavity of the multi-cavity mold fills uniformly during the injection process. Inconsistent filling can lead to variations in the quality and dimensions of the produced parts. To achieve uniform filling, the design of the mold should take into account factors such as gate placement, flow channels, and part geometry. Properly balanced flow paths to each mold cavity are vital to guarantee an even distribution of molten plastic material.
Preventing Short Shots: Short shots, where a cavity does not fill completely, can result in defective or subpar products. To prevent short shots, it’s crucial to carefully analyze and address factors such as gate size, injection pressure, and material flow dynamics. A well-designed gating system that provides controlled and balanced plastic flow to each cavity is essential to ensure complete filling and consistency.
Effective Cooling Systems: An efficient cooling system is a cornerstone of multi-cavity plastic injection molding project design. Proper cooling is necessary to maintain the appropriate temperatures for both the mold and the parts during the production cycle. Effective cooling ensures that the plastic solidifies correctly, minimizes cycle times, and prevents warping or deformation of the molded parts. Cooling channels should be strategically positioned to target critical areas, and the cooling process should be carefully controlled.
Mold Flow Analysis: Utilizing advanced simulation tools for mold flow analysis is a valuable practice in multi-cavity mold design. These tools allow engineers to visualize how the plastic material flows through the mold during injection. By conducting a thorough mold flow analysis, potential issues such as air traps, weld lines, or uneven filling can be identified and addressed before the mold is manufactured. This step aids in optimizing the mold design for maximum efficiency and quality.
Material Selection: The choice of materials for multi-cavity mold manufacturing is critical. High-quality materials that can withstand the stresses and demands of high-volume production are essential. The mold material should have excellent heat conductivity, wear resistance, and dimensional stability. The selection of the appropriate material directly impacts the mold’s longevity and its ability to consistently produce high-quality parts over time.
These design principles are the building blocks for successful multi-cavity mold design. Adhering to them not only ensures the optimal functioning of the multi-cavity injection mold but also guarantees the production of high-quality parts consistently. It’s imperative for mold designers to carefully consider each of these principles to maximize the benefits of multi-cavity molds in high-volume manufacturing processes.
What problems are often encountered in the process of multi-cavity mold production, and how to solve them?
Uneven Filling:
Redesign the Mold: Ensure that each cavity of the same mold has a uniform filling path, including well-designed runner systems and cooling channels.
Mold Flow Analysis: Use mold flow analysis software, such as Moldflow, to simulate the flow of molten plastic. Identify the reasons for uneven filling and make design adjustments accordingly.
Short Shots:
Gate Design: Carefully select and design gates to ensure they are sufficiently large to support the filling needs of all cavities.
Fill Time Control: Monitor fill times to ensure each cavity has enough time to fill properly.
Uneven Cooling:
Cooling Channel Design: Design uniform cooling channels to ensure that each cavity receives proper cooling.
Temperature Control Techniques: Consider using temperature control techniques, such as hot runner systems, for more precise temperature control.
Bubbles and Voids:
Mold Design and Material: Redesign the injection molding process to reduce the formation of bubbles and select plastics with low gas emissions.
Mold Flow Analysis: Use mold flow analysis to identify potential bubble issues in single cavity mold and then modify the mold to reduce bubble formation.
Wear and Damage:
Mold Maintenance: Establish a regular mold maintenance schedule, including cleaning and lubrication, to extend mold life.
Wear-Resistant Materials: Consider using more wear-resistant materials for mold components to reduce wear.
Changes and Repairs:
Documentation Records: Maintain detailed records of mold changes and repairs to ensure a clear understanding of historical modifications.
Mold Inspection: Regularly inspect the mold, including all cavities, to identify potential issues and make timely repairs.
Quality Control:
Inspection and Testing: Establish a quality control process, including inspection and testing, to ensure that all cavities produce parts that meet specifications.
Data Analysis: Collect and analyze production data to promptly detect issues and take corrective actions.
In addressing these issues, effective collaboration and communication among mold designers, manufacturers, engineers, and operators are essential. Together, they can identify the root causes of problems and take collective action. Continuous learning and improvement in mold design and production processes are crucial for achieving efficient, high-quality production in multi-cavity mold manufacturing.
The adoption of multi-cavity molds in the plastic injection molding industry has indeed revolutionized manufacturing processes, enabling manufacturers to meet the growing consumer demand for high-quality products efficiently and cost-effectively. This versatile technology, when implemented with careful consideration of design principles and proactive problem-solving, can be a game-changer for businesses striving for competitiveness and excellence in the market.
Sino-Mold Industrial Co., Ltd Case Study: Meeting High-Quality Demands in the European Automotive Industry
Client Profile:
Industry: Automotive Manufacturing
Challenge: Consistent production of precision auto components for European luxury car manufacturers
Client Location: Europe
The Challenge:
A European automotive component manufacturer faced a critical challenge. They were the primary supplier of precision auto components to several renowned European luxury car manufacturers. The demand for these components was not only substantial but also came with exceptionally high-quality standards. The client needed to find a solution that would enable them to maintain consistent, high-quality production and meet the rigorous demands of their prestigious clientele.
Our Solution:
Recognizing the client’s need for precision and consistency, Sino-Mold Industrial Co. Ltd proposed a solution based on multi-cavity molds. The key components of our solution included:
Customized Mold Design: Our team of seasoned engineers designed multi-cavity molds tailored to the specific requirements of the auto components. The design of single cavity molds prioritized uniform filling and precise part dimensions, in line with the high-quality standards of European luxury car manufacturers.
Efficient Cooling Systems: We incorporated state-of-the-art cooling channels within the mold design. These channels were strategically positioned to ensure proper cooling and prevent warping or deformation of the molded parts.
Material Selection: We carefully selected high-quality materials suitable for multi-cavity mold manufacturing, guaranteeing both longevity and consistent performance.
Quality Control: Sino-Mold Industrial Co. Ltd established a rigorous quality control process, including regular inspections and testing, to ensure every cavity-produced parts that met the client’s exacting quality standards.
The Results:
The implementation of multi-cavity molds had a transformative impact on the client’s production process:
Consistent High Quality: The multi-cavity molds ensured the production of auto components that consistently met the stringent quality standards of European luxury car manufacturers. This consistency was essential for maintaining the client’s position as a trusted supplier.
Efficiency and Cost Savings: The ability to produce multiple components in a single injection cycle significantly increases production efficiency. This not only met high-volume demand but also resulted in cost savings, particularly in labor and material expenses.
Competitive Edge: The client’s enhanced production capabilities allowed them to fulfill large orders promptly, giving them a competitive edge in the European automotive market.
Client Feedback: The client expressed their satisfaction with Sino-Mold Industrial Co. Ltd’s solution, particularly in achieving the high-quality standards demanded by their prestigious European clientele. They highlighted the precision and consistency achieved through the multi-cavity molding solution.
Conclusion:
This case study exemplifies how Sino-Mold Industrial Co. Ltd’s multi-cavity mold solution addressed the unique challenges of a European automotive component manufacturer. By ensuring consistent, high-quality production and increasing efficiency, the client was able to maintain its reputation as a top-tier supplier to the European luxury car market.

Contact Us:
If you are facing similar challenges in meeting high-quality demands for precision components in the European and American markets, please don’t hesitate to reach out to us. We are ready to provide the expertise and support you need to optimize your production processes and excel in your industry.
Sino-Mold Industrial Co. Ltd
Email: louise@sinomold.com
Website: www.sinomold.com