Understanding Deformation in Injection Molding
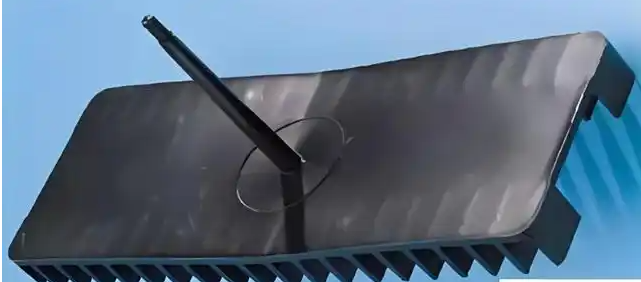
What Causes Deformation? The Role of Mold Temperature
Deformation refers to unintended shape changes in plastic parts during manufacturing, leading to defects like warping, sink marks, and shrinkage. Critical factors include:
Material Stress: Uneven cooling or improper heat treatment.
Structural Weakness: Poor gate design or non-uniform wall thickness.
Machining Errors: Micro-deformations from CNC processes.
Plastic Materials: The structure of plastic materials, characterized by long molecular chains, influences their behavior under internal stress and affects shrinkage rates.
Why Large Molds Face Higher Risks
Large molds (e.g., automotive bumpers, appliance housings) are prone to deformation due to:
Complex geometries requiring precise cooling.
Residual stress accumulation from extended cycle times.
Dimensional instability during mass production.
Mold Cavities: Poorly designed or degraded mold cavities can lead to issues like flash and inadequate clamping force, contributing to deformation.
Types of Deformation in Injection Molded Parts
Deformation in injection molded parts can manifest in various forms, each with distinct characteristics and causes. Understanding these types is crucial for diagnosing and addressing issues in the injection molding process. The most common types of deformation include:
Warping: Warping occurs when the molded part develops a twisted or bent shape after it cools and solidifies. Non-uniform cooling, unequal shrinkage rates, or internal stresses within the plastic material often cause this type of deformation. Warping can lead to significant dimensional inaccuracies and affect the overall functionality of the injection molded part.
Sink Marks: Sink marks are depressions or surface imperfections that appear on the part’s surface during cooling. They typically occur in thicker sections of the part where the cooling rate is slower, leading to uneven shrinkage. Sink marks not only affect the aesthetic quality of the injection molded parts but can also indicate potential issues with the mold design or injection process.
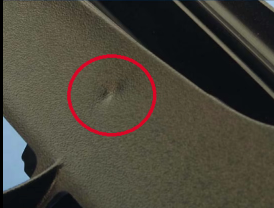
Shrinkage: Shrinkage refers to the reduction in dimensions of the part as it cools and solidifies. This is a natural phenomenon in the injection molding process due to the cooling of molten plastic. However, excessive shrinkage can cause dimensional inaccuracies, leading to parts that do not meet the required specifications.
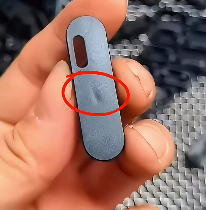
Flash: Flash is the excess plastic that appears as a thin layer or protrusion along the parting line of the mold. It occurs when molten plastic escapes from the mold cavity during the injection process. Flash can increase the post-process workload and pose quality risks if not properly managed.
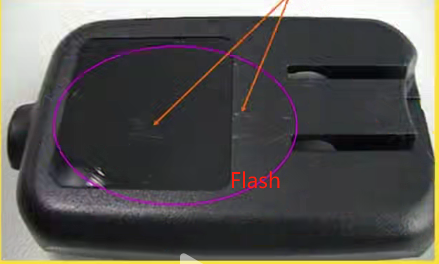
Sinkage: Similar to sink marks, sinkage is a type of deformation where the molded part develops a depression due to uneven cooling or shrinkage. This can compromise the structural integrity and appearance of the injection molded parts.
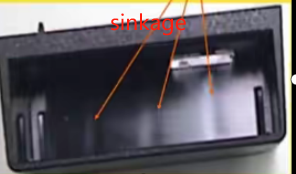
Effects of Deformation on Molded Parts
Deformation in injection molded parts can have significant repercussions on the mechanical properties and aesthetics of the final products. The effects of deformation include:
Compromised Mechanical Properties: Deformation can weaken the structural integrity and reduce the mechanical strength of injection molded parts. Warping, for instance, can lead to uneven stress distribution, affecting the load-bearing capabilities and potentially causing premature failure in critical applications. Ensuring uniform wall thickness and proper mold design can help mitigate these issues.
Aesthetic Defects: Deformation defects such as warping, sink marks, and shrinkage can mar the appearance of injection molded products. Surface irregularities and dimensional inaccuracies may render the parts visually unappealing and unsuitable for applications where aesthetics are crucial. Maintaining consistent mold temperature and optimizing the injection molding process can improve the visual quality of the parts.
Functional Issues: Deformation can lead to misalignments, interferences, or poor fitment with other components, resulting in impaired product performance or assembly difficulties. For example, excessive injection pressure or uneven shrinkage can cause parts to deviate from their intended dimensions, complicating the assembly process and reducing overall product reliability.
Quality Concerns: Deformation-related defects can compromise the overall quality of injection molded products, reducing customer satisfaction and potentially leading to costly product recalls or rework. Addressing these issues through careful mold design, precise control of injection speed, and reducing injection pressure can enhance the quality and consistency of the final products.
Identifying Deformation in Injection Molded Parts
Identifying deformation in injection molded parts is crucial for ensuring the production of high-quality, dimensionally accurate parts with minimal deformation. The following methods can be employed to identify deformation:
Visual Inspection: Signs of Deformation
Visual inspection is a simple and effective method for identifying deformation in injection molded parts. Signs of deformation include:
Warping: A twisted or bent shape of the molded part indicates warping. This can be visually detected by comparing the part to its intended shape and checking for any deviations.
Sink Marks: Depressions or surface imperfections on the part’s surface are indicative of sink marks. These can be identified by closely examining the surface of the part for any irregularities.
Shrinkage: Reduction in dimensions of the part can be observed by comparing the part to its original design specifications. Shrinkage is often noticeable in areas where the part appears smaller than intended.
Flash: Excess plastic, flake, or hairy material on the parting surface and line is a sign of flash. This can be easily detected by inspecting the edges and seams of the molded part.
Sinkage: A depression or sink mark on the molded part can be identified by examining the surface for any areas that appear sunken or uneven.
Measurement Techniques: Detecting Deformation
Measurement techniques can be employed to detect deformation in injection molded parts. These techniques include:
Dimensional Measurement: Measuring the dimensions of the molded part to detect any deviations from the designed specifications. This can be done using calipers, micrometers, or coordinate measuring machines (CMMs) to ensure the part meets the required tolerances.
Surface Roughness Measurement: Measuring the surface roughness of the molded part to detect any irregularities or defects. Surface roughness testers can provide precise measurements of the part’s surface finish, helping to identify any issues that may affect the part’s appearance or functionality.
Warpage Measurement: Measuring the warpage of the molded part to detect any twisting or bending. This can be done using specialized equipment such as laser scanners or optical measurement systems to accurately assess the part’s flatness and overall shape.
Sink Mark Measurement: Measuring the sink marks on the molded part to detect any depressions or surface imperfections. This can be done using profilometers or other surface measurement tools to quantify the depth and extent of the sink marks.
5 Proven Strategies to Eliminate Deformation
1.Plastic Materials & Heat Treatment Optimization
High-Stability Steels: Optimizing the manufacturing process, including the use of pre-hardened grades (P20, 718H) and alloys (NAK80) with < 0.5% composition variance, is essential to reduce deformation in large plastic molds.
Vacuum Quenching: Triple tempering reduces internal stress (±1 HRC tolerance). Case Study: Reduced warpage by 40% in a 2.8m EV bumper mold using gradient quenching.
2. CAE-Driven Structural Design
Moldflow/AutoForm Simulation: Predict warpage hotspots with 95% accuracy.
Topology Optimization: Achieve 15% weight reduction while enhancing rigidity.
Project Highlight: 3.2m dashboard mold optimization cut cycle time by 22% for a Tier 1 supplier.
3.5-Axis CNC Precision Machining
DMG MORI 5-Axis Systems: Eliminate repositioning errors for complex contours.
Adaptive Cutting: Real-time feed rate adjustments minimize machining stress.
Accuracy: ±0.02mm cavity tolerance, Ra 0.4μm surface finish.
4.AI-Optimized Cooling Systems
3D-Printed Conformal Cooling: Thermal gradient <5°C across mold surfaces.
IoT Monitoring: Live temperature tracking + automated flow control.
5.Deformation Compensation Technology
Laser Scanning & CMM Verification: Full-scale inspection at all stages.
Machine Learning: Predictive toolpath correction based on historical data.
Case Study: Solving Injection Molding Defects in a 3.5m Air Conditioner Housing Mold
Client Challenge: 0.7mm mid-section shrinkage causing assembly mismatch.
Sino-mold Solution:
Redesigned conformal cooling channels + zone-specific temperature control.
5-axis compensation machining with closed-loop feedback.
Results:
Flatness improved to 0.08mm (meeting ISO 2768 fine tolerance).
Annual scrap cost reduced by $150K.
Get Your Deformation-Free Mold Solution,Email: louise@sino-mold.com