Which is the Right Choice for your new project?
Currently, 3D printing stands as a widely embraced technology in the manufacturing industry, while injection molding boasts a rich history and a high level of maturity. The appearance of cost-effective 3D printing technology makes rapid prototyping possible and provides an alternative method for manufacturing plastic parts and products. Injection molding and 3D printing are common and efficient technologies, but sometimes, one method may be more suitable for your project. Evaluating certain aspects of the project helps to determine that injection molding or 3D printing is the best choice. This article provides a brief overview and comparison of the two technologies, and a series of key factors to consider when choosing the best production method, for your project.
What’ s the difference between 3D printing and injection molding?
3D Printing
3D printing is a form of additive part manufacturing process, which means the entire production process involves adding material layer by layer. With 3D printing, there’s no need to create molds for manufacturing parts – all you require is a 3D printing model file. Moreover, the market offers a wide array of 3D printing technologies and materials to choose from.
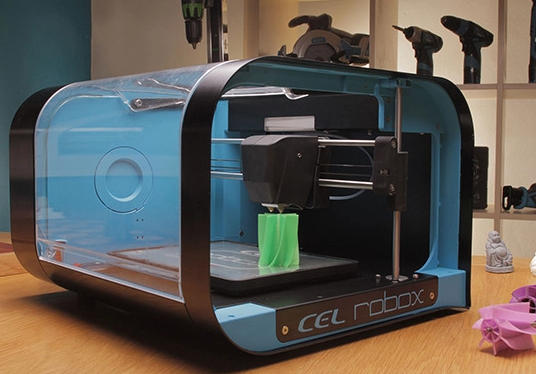
Injection Molding
Injection molding is a traditional and widely used industrial manufacturing technique. It involves the initial fabrication of molds, followed by the placement of these molds into an injection molding machine. The process creates the contours of parts by injecting material into the injection molders’ cavities. By introducing molten material into the molds, this manufacturing technique allows for the rapid formation of your product. Subsequently, the material cools down and attains its final solid shape.
What are the advantages of injection molding or 3D printing?
Injection Molding
Injection molding offers significant advantages, particularly for large-scale production, with high precision and perfect repeatability. When using plastic injection molding, you have a wide range of materials to choose from. Each material can have thousands of variations through additives, each resulting in different material properties throughout. Material weight, cost, flexibility, limited only by plasticity, and possibilities seem endless.
Injection molding can both mass-produce and create intricate details. Adding details to injection-molded parts is relatively easy due to the Injection Molding process’s repeatability. It makes manufacturing parts with higher strength straightforward. In fact, injection molding processes can use fillers within the injection molds.

3D Printing
3D printing boasts numerous advantages that make it a valuable complement to traditional, manufacturing methods and techniques. Firstly, it excels in product iteration. While 3D printing has evolved into a reliable manufacturing technology, it still shines as a rapid prototyping tool. With 3D printing, you can print prototypes for testing, make all modifications using 3D printing modeling software, and then print again to confirm changes. This flexibility saves you time and money while refining product design.
Using 3D printing also aids in material waste reduction. Compared to traditional CNC machining methods, 3D printing can use just the amount of material required for the entire project, reducing waste and indirectly lowering production costs. With 3D printing, you can also optimize supply chain management to avoid storage costs associated with excess inventory.
How to choose:
When contemplating the development of a project, it’s common to be torn between choosing 3D printing or plastic injection molding for a mass production part. Here are some factors to help you make a right decision.
Batch Size:
- Injection Molding is ideal for large-scale production (1000+ parts).
- 3D printing suits low volume production runs (<10) and is cost-effective for simple designs.
Design Complexity:
- Injection Molding requires complex mold designs.
- 3D printing excels in handling intricate designs with ease.
Iteration Duration:
- Injection Molding takes longer (10-20 days).
- 3D printing offers rapid iterations (as quick as 3 days).
Customization:
- Injection Molding is less suitable for modifications.
- 3D printing allows easy customization and prototyping.
Material Strength:
- Injection molding produces stronger parts.
- 3D printing may have structural imperfections.
Surface Finish:
- Injection Molding provides a smoother finish.
- 3D printing may require post-processing for a ridged surface.
Material Waste:
- Injection Molding uses materials efficiently.
- 3D printing may generate waste from support structures, which matters less in larger custom batches.
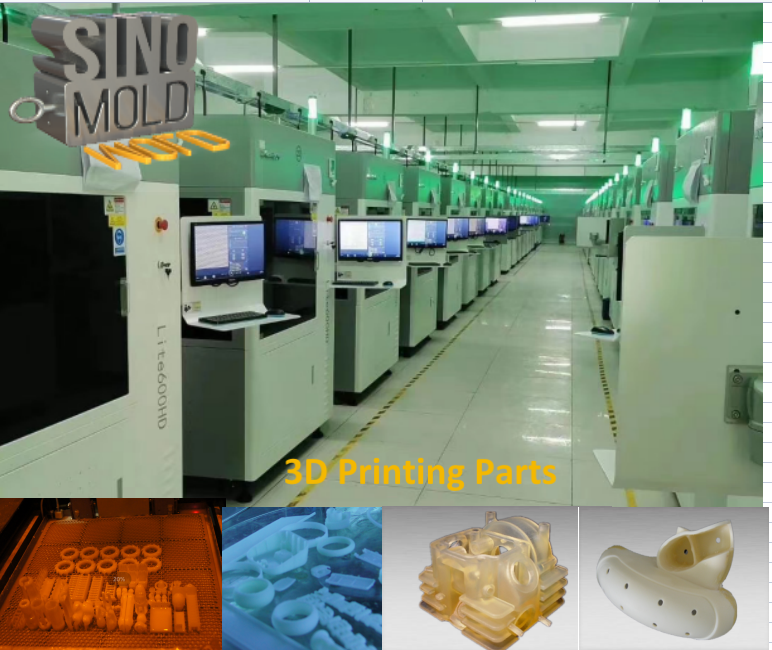
Conclusion
3D printing and plastic Injection Molding are not in direct competition; rather, they complement each other. Both can be used for manufacturing and rapid prototyping. While 3D printing, especially various additive manufacturing processes, is gaining popularity, high volume production relies on Injection Molding process and molding equipment. Typically, 3D printing is an effective tool for rapid prototype development.
When you’re faced with a decision for a new project, consider the choice of manufacturing technology. Whether it’s 3D printing or the injection molding process, our company, Sino Mold industry, has extensive experience in both. If you’re unsure about which manufacturing method to choose, you can consult our professional team to help you select the most suitable approach for your project.