The manufacturing industry knows that even the smallest details can have a profound impact on the result. In mold design and injection molding, the finish of the mold’s surface is one such detail that holds tremendous importance. Often overlooked, it plays a pivotal role in determining the appearance, functionality, and overall performance of plastic injection molded parts.
You might wonder, “Why should I care?” Well, let’s explore why mold surface finish matters to you as someone deeply involved in the world of manufacturing.
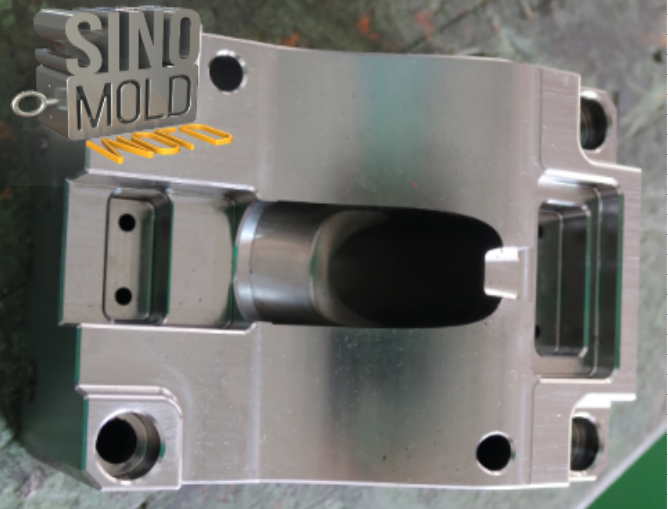
What’s The Advantages Of Mold Surface Finish?
Elevating Aesthetic Appeal: “First Impressions Are Everything”
Think about the last time you were captivated by a beautifully designed product. The surface finish of a mold directly influences the visual appeal of the final product. A smooth and impeccably polished plastic surface finish can result in a visually stunning product, while a very rough, surface texture or imperfect finish may leave you questioning its quality. Whether you’re producing consumer goods, electronics, or automotive components, aesthetics play a significant role in consumer choices. Your attention to mold surface finish can make your creations stand out.
Precision That You Demand
As someone who values precision, you know that even the slightest deviation can lead to costly errors. Mold surface finish is instrumental in maintaining dimensional accuracy. A finely finished surface reduces the risk of imperfections or irregularities on the injection molded parts themselves. It ensures that the details injection molded parts you produce adhere to the required specifications, providing the consistency and precision you demand, especially in industries that rely on accuracy.
Smoother Production: “Friction Is Not Your Friend”
Production setbacks due to friction and wear on steel mold can be frustrating. A polished mold surface minimizes friction between the mold and the molten plastic material during injection. Less friction means less wear and tear on the mold, leading to prolonged longevity and reduced maintenance costs. Additionally, it facilitates smoother ejection of the finished parts, reducing the risk of defects or damage and streamlining your production process.
Ensuring Quality
Quality should always be a top priority. Surface imperfections on the mold can transfer onto the molded parts, resulting in defects like sink marks, weld lines, or poor surface finish imperfections. Your meticulous attention to mold surface finish minimizes these defects, leading to a higher-quality final product. In industries where precision and safety are paramount, such as medical devices and aerospace, your commitment to quality can make all the difference.
Types of Plastic Surface Finish
The different techniques available for completing plastic surfaces are different for each type of product. Textures will be inserted into a mold directly. It is a simple solution that ensures all pieces are finished in the same manner. It also reduces costs by eliminating additional postprocessing. A different method for attaining the desired finish is through post-processing applications. These may include polishing, spraying beads, and polishes.
Application and types of mold surface finish in production.
Automotive Industry (Aesthetic Finish)
In the automotive industry, mold surface finishes play a pivotal role in enhancing the aesthetic appeal of vehicles. High-gloss surface finishes are applied to components like exterior body panels, dashboard elements, and interior trim pieces. These finishes give cars their sleek and polished appearance, contributing to their visual allure on the showroom floor.
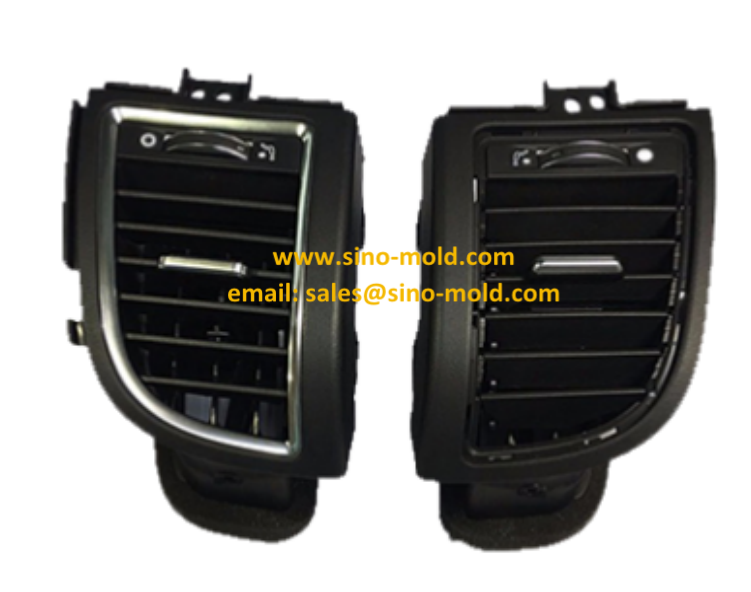
Medical Devices (Hygienic Device Finish)
The whole manufacturing process of medical devices demands the utmost precision and hygiene. Mold surface finishes are meticulously applied to ensure the smoothness and cleanliness of medical components. Injection shop also request to be dust-free. In this context, hygienic part surface finishes such plastic materials, with antimicrobial properties are vital for instruments, implants, and equipment used in medical settings to prevent contamination and ensure patient safety.
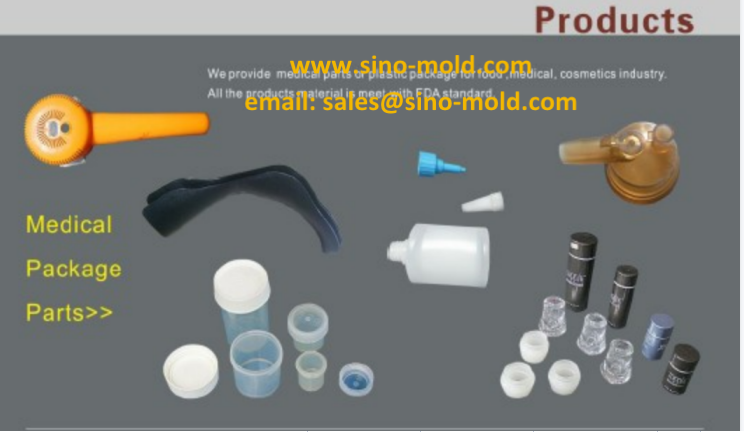
Electronics (Functional and Aesthetic Finish)
The electronics industry requires mold surface finishes that cater to both functionality and aesthetics. External casings and touch surfaces of electronic devices benefit from high-quality surface finishes for a visually pleasing appearance. Additionally, specific rough surface finishes can be engineered to provide heat dissipation properties or others, enhancing the functionality and reliability of electronic components.
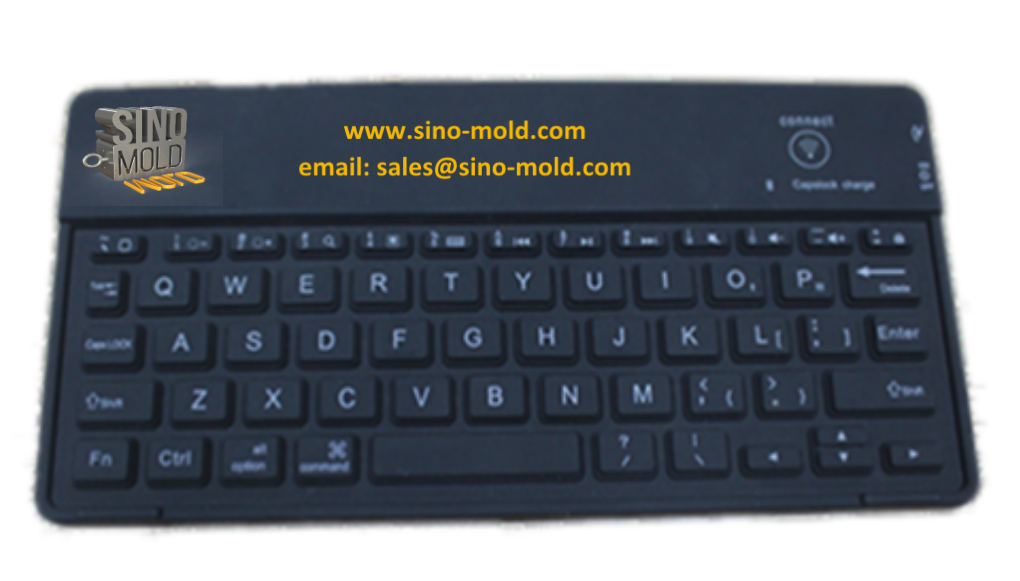
Food Packaging (Hygienic Finish)
In plastics industry for food packaging, mold surface finishes are critical to ensuring the hygiene and functionality of containers. The interior surfaces of plastic parts of packaging must be smooth and non-porous to prevent food particles from adhering, while also supporting effective sealing. This helps maintain food safety and extends shelf life.

Toy Manufacturing (Aesthetic Finish)
Toys often require meticulous mold surface finishes to attract young consumers and meet safety standards. Whether it’s action figures, dolls, or playsets, these products benefit from smooth and visually appealing surface finishes that enhance their overall quality and desirability.
Construction Materials (Textured Finish)
In the construction industry, it is applied to create building materials with various textures and patterns. For instance, concrete panels, decorative tiles, and facade cladding may feature textured surface. These textured plastic not only provide aesthetic variety but also enhance grip and visual interest in architectural designs.
Power Industry (Functional Finish)
The power equipment manufacturing sector relies on the injection molding process and the surface finish to ensure efficient electrical connections. Components such as connectors and terminals require surface treatments that improve electrical conductivity and corrosion resistance. These functional finishes are essential for maintaining reliable power transmission and distribution.
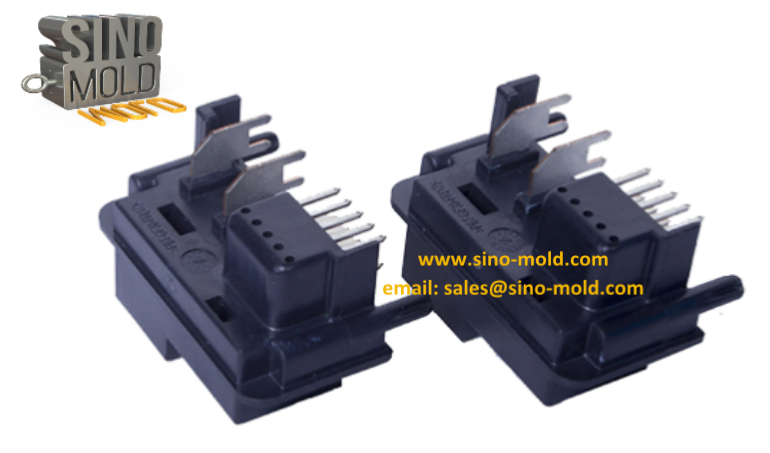
These real-world examples illustrate the diverse applications of mold surface finish across industries, serving functions ranging from aesthetic enhancement to functionality improvement and adherence to industry-specific standards. Selecting the appropriate optimal surface finish, treatment method and finish grade for mold cavity is essential for achieving the desired product quality and performance in each of these production scenarios.
How to Select the Grade of Mold Finish Needed?
The grade of the mold finish determines the surface quality of the molded part, affecting everything from aesthetics to functionality. But how do you go about selecting the right grade of mold finish for your specific project? Let’s dive into the essential considerations.
Understand Your Part’s Requirements
The first step in selecting the grade of mold finish is to understand your molded part’s requirements. Consider the following:
Aesthetic Demands: Does smoother surface of your product require a high-gloss, flawless surface for consumer appeal, or is a matte finish acceptable?
Functional Needs: Does the part’s function demand a specific surface texture or finish, such as reduced friction, better grip, or electrical conductivity?
Industry Standards: Certain industries, like medical or aerospace, have stringent surface finish requirements to meet regulatory standards.
Understanding these requirements is crucial as it sets the foundation for selecting the appropriate mold finish.
Know Your Material
Different materials react differently to mold finishes. For instance, a high-gloss finish may work well for some plastics but not for others. It’s essential to consider the material you’re working with and its specific characteristics, such as shrinkage, melting point, and flow behavior.
Consult with Experts
When in doubt, don’t hesitate to consult with mold design and manufacturing experts. They can provide valuable insights into the best finish grade for your specific project based on their experience and knowledge of industry best practices.
Budget and Lead Time
Finally, consider your budget and lead time. Higher-grade finishes typically require more time and resources. Balancing your project’s requirements with available resources is essential to ensure a successful outcome
Injection Mold Surface Finish Standards
Injection mold surface finish standards are essential guidelines used in the manufacturing industry to define and communicate the required quality and characteristics of a mold’s surface finish. These standards help ensure consistency, precision, and reliability in the production of injection-molded plastic parts and parts. Several organizations and industry bodies have established surface finish standards to serve as references for manufacturers and engineers. Some common injection mold surface finish standards include:
SPI Finish Standards:
The Society of the Plastics Industry (SPI) in the United States has defined a set of surface finish standards for injection molds, known as the SPI injection Molding Surface Finish Guide. It categorizes the surface finish into four main classes:
SPI Grade A: High-gloss finish, suitable for optical parts and products with the highest aesthetic requirements.
SPI Grade B: A good balance between aesthetics and functionality, suitable for a wide range of applications, including consumer goods and automotive parts.
SPI Grade C: A functional finish with visible machining marks, often used for parts where aesthetics and smoother surface finish are less critical.
SPI Grade D: A rough finish with visible machining marks, primarily used for internal components or parts with no aesthetic requirements.
Selecting the right grade depends on your part’s requirements and the industry standards it must meet. For example, products in the medical or aerospace industry often require Grade A or B finishes for their precision and high aesthetic standards.
Each class represents a different level of surface finish quality, with SPI A being the highest semi-gloss finish and SPI D being a semi-gloss finish and having visible machining marks.
VDI Surface Finish Standards:
The Verband Deutscher Ingenieure (VDI), a German engineering association, has established surface finish standards, primarily used in Europe. VDI standards use numerical codes to define different surface finish grades, with lower numbers indicating finer finishes.
ISO 9000 Standards:
ISO 9000 is a set of quality management standards that includes guidelines for surface finish requirements in manufacturing processes. These standards focus on maintaining consistency, meeting customer specifications, and ensuring product quality.
ASTM Standards:
The American Society for Testing and Materials (ASTM) provides various standards related to materials, testing, and surface and plastic finishes used. ASTM standards can be referenced for specific requirements in injection mold surface and plastic finishes used.
Automotive Industry Standards:
The automotive industry often defines its surface finish standards for components used in vehicles. These standards are rigorous and are aimed at ensuring the quality and performance of automotive parts.
Custom Standards:
Some companies or industries may establish their own customized surface finish standards to meet specific product requirements and quality standards. These flawed surface finishes and texture standards are often developed in-house and may not be widely recognized outside of the organization.