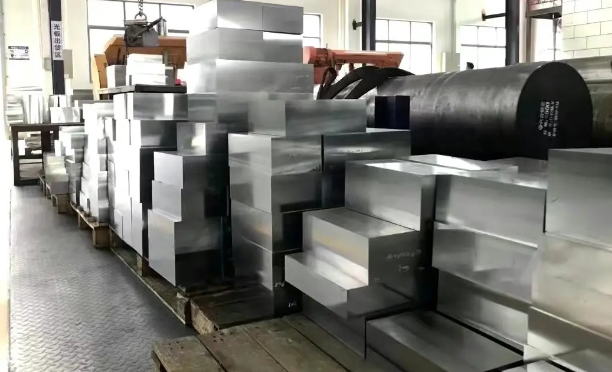
Embarking on a manufacturing journey requires not only skillful craftsmanship but also a keen eye for choosing the right materials. The heart of any molding project lies in selecting the perfect mold steel, a decision that can make or break the success of your endeavor.In this topic post, we’ll delve into the intricate world of mold steels, exploring the nuanced factors that can guide you toward the optimal choice hardened tool steels for your unique project.
As a product development manager, choosing the appropriate mold steel according to your own project can effectively save costs and improve efficiency for the company.
So maybe they always ask themselves:Which mold steel is best for my project?
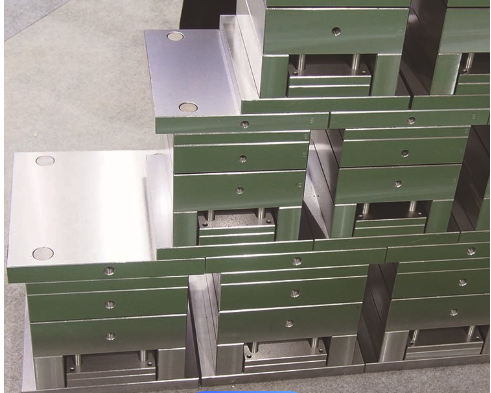
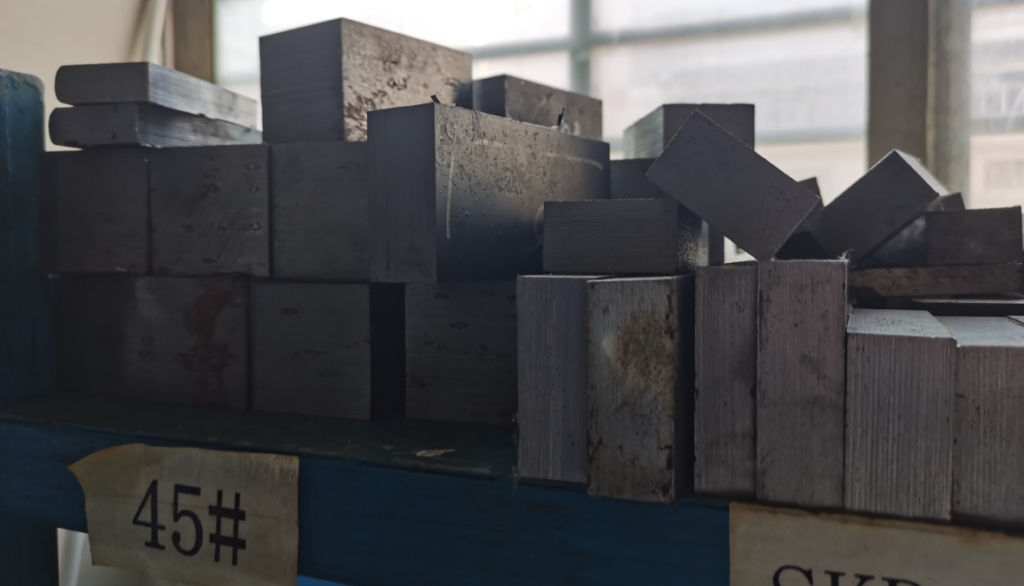
Navigating the Landscape of Mold Steel Selection:
Material Compatibility: Deciphering the Code
In the realm of mold steel selection, material compatibility emerges as a pivotal factor, resembling a delicate dance between the chosen steel and the molded material. This interaction profoundly influences the quality of the final product and the efficiency of the molding process. The right mold steel not only enhances the product’s strength, surface finish, and dimensional accuracy but also streamlines production by minimizing challenges like sticking or warping. Understanding the nuanced characteristics of mold steels, including hardness and thermal conductivity, empowers informed decision-making. Tailoring the selection to project-specific mold material and requirements ensures optimal results. Material compatibility is the guiding star, shaping the success of molding endeavors through seamless integration and superior outcomes.
Let’s take, for instance, a scenario where high-precision components need to be produced. In this case, the choice is P20 mold steel. P20 offers a balanced hardness and superior machinability, making it compatible with a variety of plastic materials. This compatibility ensures a smooth flow during the molding process, reducing the likelihood of defects. The outcome is high-quality components that meet the design specifications. This example underscores the significance of material compatibility in selecting the right plastic injection molding project and steel for seamless integration, ultimately achieving superior results in the molding process.
Hardness and Toughness: The Dynamic Duo
Hardness and toughness form a dynamic duo, each playing a crucial role in the overall performance of a substance. Hardness imparts resistance to wear and indentation, ensuring durability, while toughness provides the resilience to withstand impact and fractures. Together, they create a synergistic balance that fortifies materials for various applications. Understanding and harnessing the interplay between hardness and toughness is key to optimizing the performance and longevity of materials across diverse scenarios.
Consider the application of tool steel in the production of cutting blades for industrial use. In this context, the dynamic duo of hardness and toughness plays a crucial role. The hardness of the steel ensures that the blade maintains a sharp cutting edge, resisting wear and abrasion during repeated use. Simultaneously, toughness becomes paramount to prevent the blade from fracturing or chipping when subjected to high-impact forces, such as cutting through dense materials. The combination of hardness and toughness in the tool steel creates a robust and reliable cutting tool that can withstand challenging conditions, exemplifying the synergistic relationship between these two essential material properties.
Corrosion Resistance: Shielding Against Environmental Forces
Corrosion resistance is often a critical consideration, especially in applications where molds are exposed to aggressive environments. Delve into the characteristics of stainless steel and corrosion-resistant alloys, exploring how they shield molds from the corrosive forces that can compromise both functionality and longevity.
Consider the application of mold shock resistant tool steel in a manufacturing setting where exposure to corrosive agents is a concern. For instance, in the production of molds for plastic components used outdoors, the mold steel, such as corrosion-resistant tool steel like NAK80, acts as a protective barrier. NAK80’s corrosion resistance shields against environmental forces, including moisture and potentially corrosive plastics, ensuring the prolonged durability of the molds. This resistance not only preserves the structural integrity of the molds but also maintains the quality of the molded products. In this context, the corrosion resistance of the mold steel becomes a crucial factor, serving as a robust defense against the corrosive challenges posed by the manufacturing environment.
Machinability and Polishability: Crafting Intricacy
The artistry of mold-making lies in the ability to craft intricate details seamlessly. Explore the machinability of mold steels, examining how easily they can be shaped and formed. Additionally, dive into the realm of polishability, where the choice of steel can elevate the aesthetics of the final product through a mirror-like finish.
Imagine a scenario in precision tooling, where the production of intricate components requires a delicate balance between machinability and polishability. Take, for instance, the creation of precision molds for high-end consumer electronics. Utilizing a mold steel like S136, known for its exceptional machinability, ensures efficient and precise machining of complex mold cavities. Simultaneously, the steel’s high polishability allows for the creation of smooth and flawless surfaces on the molded components. The synergy between machinability and polishability in S136 enables the crafting of intricate details with precision, showcasing how these properties are essential in achieving the desired intricacy in the final product.
Production Volume: Scaling Heights
Production volume is a key determinant in mold steel selection. Explore the wear resistance and thermal properties of various steels under high-stress conditions. Understand how the right tool steel choice can lead to increased productivity, reduced downtime, and enhanced overall efficiency in large-scale manufacturing.
Consider a manufacturing scenario where the demand for high production volume is paramount, such as the mass production of automotive components. In this context, choosing mold steel like H13, renowned for its excellent heat resistance and durability, allows for extended production runs without compromising tool integrity. H13’s ability to withstand the high temperatures and mechanical stresses associated with high-volume production ensures consistent and reliable performance over prolonged periods. The scalability of H13 mold steel becomes evident as it facilitates the efficient and continuous production of large quantities, allowing manufacturers to scale new heights in meeting high-volume demands.
Budget Constraints: Balancing Act
Budget constraints often play a significant role in decision-making. Delve into the world of cost-effective mold steels, understanding how the upfront investment aligns with long-term benefits. Strike a balance that aligns with your project’s financial parameters without compromising on the quality and performance of the chosen steel.
Picture a manufacturing scenario where budget constraints are a crucial consideration, such as in the production of cost-sensitive consumer goods. Here, the choice of mold steel, like the economical P20, becomes a strategic balancing act. P20 offers a cost-effective solution without compromising on essential properties like hardness and machinability. By selecting P20 within budget constraints, manufacturers can achieve the required mold performance, ensuring a delicate balance between cost-effectiveness and the necessary qualities for successful production. In this context, the choice of mold steel exemplifies a pragmatic approach to meeting budget limitations without sacrificing performance.
Heat Treatment Requirements: The Crucible of Transformation
Heat treatment is the crucible where mold steel transforms into a resilient and durable tool. Explore the heat treatment processes applicable to different mold steels, understanding how they influence hardness, toughness, and overall performance. Navigate the intricate world of quenching, tempering, and annealing to optimize the steel’s properties for your project.
Imagine the transformative process of heat treatment in the realm of mold steel, likened to a crucible where properties are meticulously crafted. Consider a situation where the production of high-strength components demands a specific heat treatment regimen. Utilizing a versatile mold steel like S7 allows manufacturers to tailor the heat treatment process, optimizing hardness, toughness, and wear resistance to meet precise requirements. The crucible of heat treatment becomes the key to unlocking the full potential of mold steel, allowing for a customized transformation that ensures the molds withstand the rigors of demanding applications. In this context, the strategic application of heat treatment stands as the crucible where mold steel undergoes a metamorphosis to attain its optimal performance characteristics.
Surface Finish Specifications: The Artistry of Appearance
The surface finish of molded products is an art form that relies on the choice of mold steel. Uncover the characteristics of mold steels that contribute to achieving specific textures and finishes. Whether aiming for a high-gloss shine or a textured surface, understand how different steels lend themselves to the artistry of appearance in the injection molding process.
Consider a scenario where aesthetics play a pivotal role, such as in the production of consumer goods with intricate designs. The choice of mold steel, like the corrosion-resistant and polishable NAK80, becomes an artful consideration for meeting surface finish specifications. NAK80’s excellent polishability ensures the creation of smooth and visually appealing surfaces on molded products. The artistry lies in selecting mold steel that not only meets functional requirements but also elevates the appearance of the final product. In this context, the surface finish specifications become a canvas where the characteristics of mold steel contribute to the artistry of achieving an impeccable and visually pleasing finish.
Unveiling the Masterpieces: Common Types of Mold Steels
P20 (Plastic Mold Steel): Crafting Precision
Craft precision with P20, an ideal choice for low to medium production volumes. Explore its superior machinability and polishability that lay the foundation for meticulous craftsmanship.
P20, a stalwart in the world of plastic injection mold steels, is celebrated for its precision and versatility. Dive into its characteristics, understanding how it excels in low to medium production volumes. Explore its machinability and polishability, making it a go-to choice for crafting intricate plastic molds with precision and finesse.
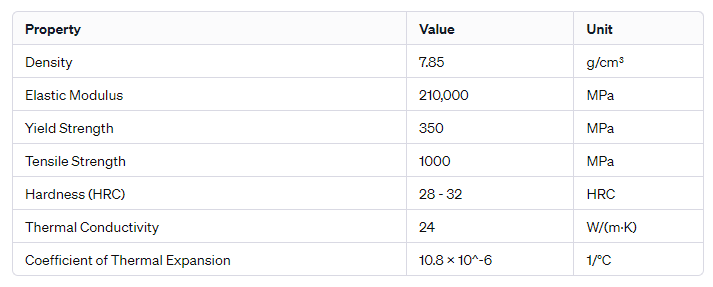
H13 (Hot Work Tool Steel): Embracing the Heat
Embrace the heat with H13, a powerhouse for high-temperature applications. Discover its unparalleled hardness and resistance to thermal fatigue, ensuring durability under extreme conditions.
H13 stands as a robust contender in high-temperature applications. Delve into its heat-resistant properties, exploring how it maintains hardness and strength under intense thermal conditions. Understand its suitability for molds exposed to extreme temperatures, ensuring longevity and performance in demanding environments.
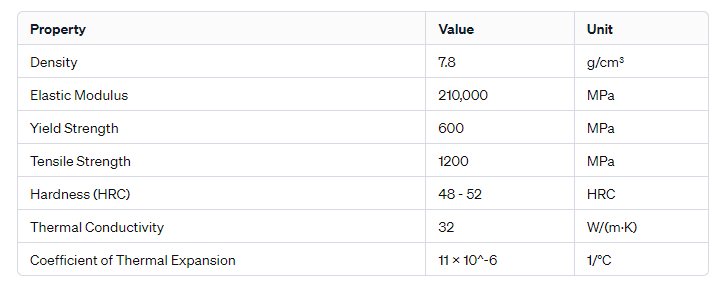
S136 (Stainless Steel): The Guardian of Integrity
Entrust the integrity of your injection molds due to S136, a stainless steel guardian offering superior corrosion resistance. Explore its versatility in molding applications involving corrosive materials.
S136, a stalwart among stainless mold steels, stands as the guardian of mold integrity. Uncover its resistance to corrosion, making it an ideal choice for molds exposed to corrosive materials. Explore its versatility across various molding applications, ensuring longevity and reliability in challenging environments.
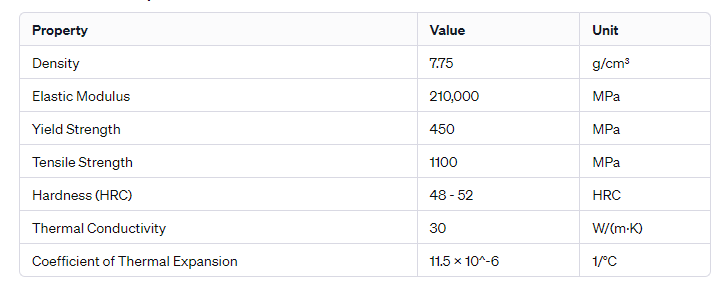
NAK80 (Pre-Hardened Plastic Mold Steel): Sculpting Excellence
Sculpt excellence with NAK80, a pre-hardened steel that excels in high polishability and texture retention. Delve into its capabilities for achieving high-quality surface finishes that leave an indelible mark.
NAK80 emerges as a sculptor’s tool in the realm of plastic mold steels. Discover its pre-hardened nature, making it an efficient choice for molds requiring high polishability and texture retention. Unearth its ability to sculpt excellence in surface finishes, contributing to the creation of high-quality, visually appealing molded products.
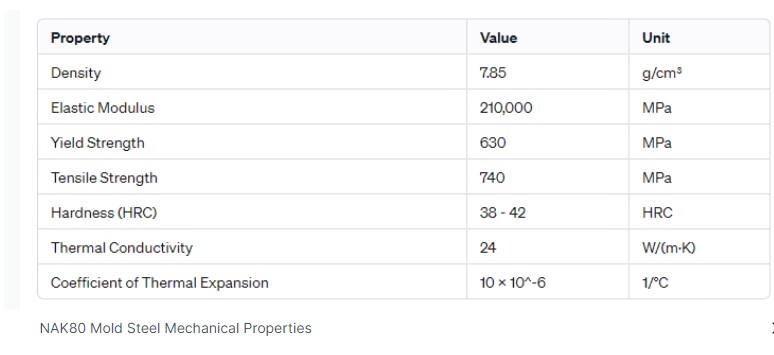
420 Stainless Steel: Polishing Elegance
Polish elegance into your molds with 420 stainless steel. Appreciate its corrosion resistance and polishability, making it an ideal choice for applications requiring a high-gloss finish.
420 stainless steel, known for its elegance and polishability, takes center stage in molding applications where aesthetics matter. Delve into its corrosion-resistant properties, ensuring the longevity of molds exposed to environmental elements. Uncover how it polishes elegance into the final product, making it a preferred choice for applications requiring a high-gloss finish.
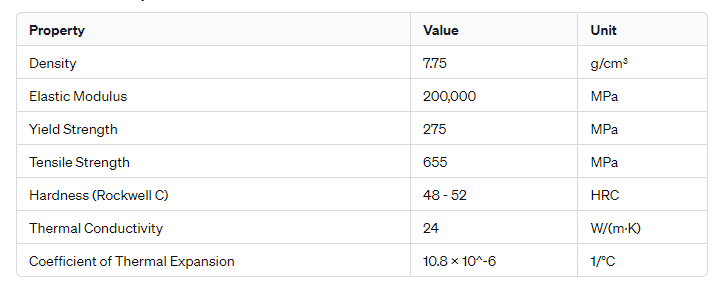
Conclusion: Crafting Your Legacy
Choosing the best mold steel for your project is an art form, a meticulous process that demands a deep understanding of your unique requirements. As you navigate the complexities of material compatibility, hardness, corrosion resistance, and budget constraints, envision the masterpiece you are crafting. The right mold steel is not just a choice; it’s a legacy, ensuring the success and longevity of your molding project. Select with care, and watch your creations stand as a testament to excellence in the world of manufacturing.
In the realm of mold steel selection, each decision is a brushstroke, contributing to the masterpiece of your manufacturing legacy. Navigate the intricacies, understand the subtleties, and let your choice of mold steel be the brush that paints the canvas of your success. Craft with precision, embrace durability, and polish elegance into every mold—your legacy awaits in the products that bear the mark of your excellence.
Choose wisely because in the field of mold making, choosing the right steel will lead to carving the perfect product in the future.
Choose wisely, for in the world of mold making, your steel is the sculptor of your manufactur e?
