Lead In
Plastic injection molding is the process of manufacturing plastic components by injecting molten plastic into injection molding cavities. This is a commonly used manufacturing technique. It may generate significant consumption during the process. Sustainability is a matter of great concern for all businesses today. As a continuously evolving and highly demanded manufacturing process, injection molding holds the potential to a significant carbon footprint and have a profound and meaningful impact on the sustainability of plastic products worldwide. To achieve this goal, we need to focus on how to design more sustainable products and processes within the injection molding industry.

How are sustainable development values applied to injection molding?
Design for Manufacturing (DfM) aligns closely with the fundamental principles of sustainable design. DfM focuses on minimizing waste, costs, and time while striving for top-notch quality—a mission that mirrors sustainability’s broader, holistic approach. Sustainable design takes into account the environmental, economic, and social impacts only the amount of a product’s entire lifecycle, from the raw materials to material sourcing to disposal, with the ultimate goal of reducing adverse ecological and ethical effects at every stage.

Optimizing processes to meet DFM objectives often leads to sustainability benefits, including:
- Material Waste Reduction: Improving tool design to minimize material waste.
- Energy Efficiency: Implementing optimized production techniques to reduce energy consumption.
- Reduced Chemical Dependency: Decreasing reliance on chemicals of concern or problematic ingredients.
Moreover, many DfM principles are in harmony with core sustainability tenets, such as:
- Standardized Parts and Materials: Enabling easier recycling, repair, and reuse.
- Modular and Flexible Design: Allowing for upgradeability rather than full product replacement.
- Recycled Materials Usage: When possible, reducing waste, energy demand, and the environmental impact of raw material extraction.
DfM and sustainable design share common goals of promoting maximum efficiency, ensuring process and product safety, and embracing environmental responsibility. DfM serves as a powerful toolkit, while sustainable design provides the underlying values and ethical considerations, such as:
- Minimizing Material Waste: Prioritizing the reuse of scrap materials whenever feasible.
- Energy Efficiency: Emphasizing energy-efficient practices in all equipment and facilities.
- Reducing Adverse Materials: Eliminating or reducing reliance on materials with harmful effects.
- Carbon Footprint Reduction: Using low-emission energy sources to minimize carbon footprints.
- Optimized Water Management: Implementing efficient water usage and responsible discharge treatment.
- End-of-Life Considerations: Facilitating product recycling or biodegradation at the end of their life cycle.
- Worker Health and Safety: Ensuring the well-being of workers through proper protocols and protective measures.
How to Choose Sustainable Materials for Injection Molding?
When it comes to sustainable and injection molding processes, a crucial factor is the choice of environmentally friendly and non-toxic source materials. Designers and manufacturers now have access to an expanding and wide array of eco friendly and sustainable material options, including:
Biodegradable plastic materials or compostable plastics like polybutylene adipate terephthalate (PBAT).
Recycled plastic resins such virgin recycled plastics, such virgin plastics such as recycled polyethylene terephthalate (rPET), recycled polypropylene (rPP), and recycled high-density polyethylene (rHDPE).
Composite plastics blended with natural plastic fibers.
Poly(diketoenamine) or PDK, which is noteworthy for its ability to be produced from biological sources or recycled plastics. PDK can be easily recycled and reprocessed multiple times without significant impact or material degradation. It boasts resistance to high heat, mechanical properties akin to PET and/or HDPE, and, under suitable conditions, the high quality products can be biodegradable and compostable.
Material selection should prioritize reducing plastic product, carbon footprint, minimizing energy consumption, and waste generation while still meeting technical product specifications. Additionally, it should allow for recyclability or biodegradability at the end of a product’s life cycle.

Can manufacturers do anything else?
In addition to material selection, manufacturers can implement eco-conscious practices in plastic parts manufacturing processes and their injection molding production process:
- Utilize energy- and water-efficient equipment, less fossil fuels, manufacture parts using renewable raw materials and consider environmental benefits of upgrading to sustainable machinery.
- Identify and address efficiency losses in processes, optimizing cooling, heating, process settings extra material used, energy usage, waste production recycle materials, and cycle times.
- Embrace renewable energy sources like solar and wind to power facilities.
- Enhance energy efficiency and decrease carbon emissions within facilities by implementing more energy–efficient lighting, HVAC system upgrades, and reducing overall energy consumption to mitigate greenhouse gas emissions.
- Establish rigorous, highly efficient and cost effective preventive maintenance procedures to enhance operational efficiency and prolong equipment lifespan.
- Harness automation and AI to keep production costs minimize scrap rates and material waste.
- Explore reusing ground or granulated scrap or recycled virgin plastic used, in your production processes when feasible.
- Reduce water discharges and invest more customers in closed-loop cooling systems less energy used where possible.
- Minimize or eliminate the use of release agents and opt for non-toxic alternatives.
- Ensure the proper recycling of solvents, fossil fuel fuels and chemicals, both onsite and offsite.
- Develop and enforce protocols for the safe and responsible handling and disposal of non-recyclable waste.
- Continuously monitor sustainability initiatives and key performance indicators (KPIs) and make ongoing improvements where necessary.
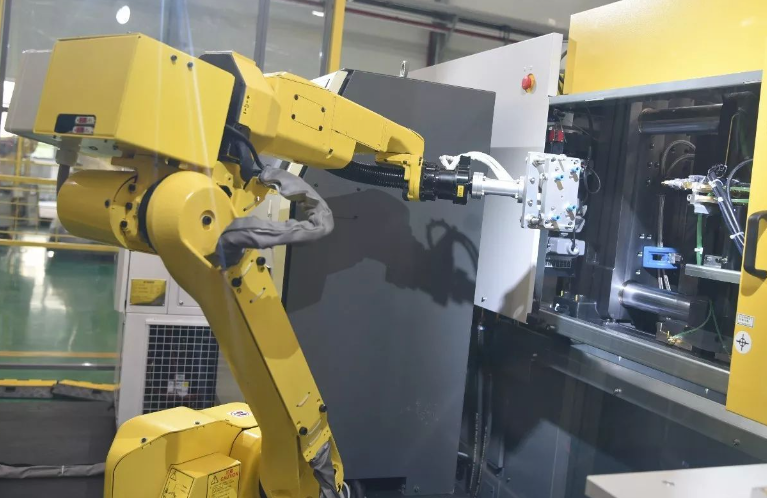
Conclusion
In conclusion, sustainability isn’t the sole influencer of trends in the injection molding process, but upon closer examination, it is undeniably at the heart of many industries the industry’s most significant shifts. Concepts like recyclability, closed-loop processes, automation, and the recent global resin shortages all relate to the growing urgency for more eco-conscious and ethically driven manufacturing processes. As manufacturers adapt their processes, from material procurement to facility operations to end-of-life product disposal, this paradigm shift will continue to present new challenges. Yet, it also holds the potential to create fresh opportunities within injection molding, leveraging innovation and technology to make it a greener, cleaner part of the manufacturing process. Ultimately, sustainability isn’t just a fleeting trend; it’s an emerging standard that is poised to shape the industry for decades to come.
What does Sino Mold do?
At Sino Mold, we strive to minimize the environmental impact of plastic injection molding to the best of our ability. As a company that values sustainability, we actively seek sustainable solutions for both our clients and our operations. While our plastic injection moulding factory is based in China, we also proactively respond to the green initiatives of many manufacturers our European and American clients and align with China’s sustainability policies. As a team, strong communication and concerted efforts from design to implementation are emphasized to streamline production and significantly reduce our resource usage throughout the entire manufacturing process.