Introduction: Embarking on the journey of plastic injection molding unveils a realm of possibilities for transforming raw plastic into myriad products. As Louise from Sino-Mold Industrial Co., Ltd., let’s demystify the complexities of plastic injection molds common manufacturing process and molding timelines, providing you with valuable insights to facilitate informed decision-making.
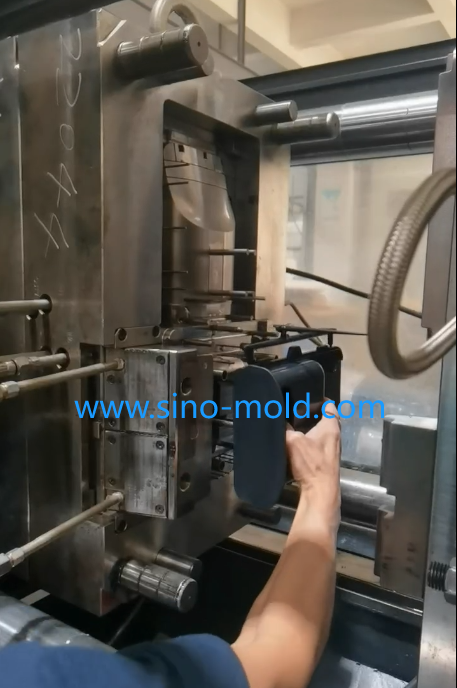
What Factors Influence Injection Molding Timelines?
Design Complexity:
The intricacy of product designs significantly influences lead times and the time required for molding. Products with complex geometries or intricate details demand meticulous attention and may affect lead time or extend the production cycle.
Material Dynamics:
The choice of plastic material plays a pivotal role in determining injection molding timelines. Each material has unique melting and cooling characteristics, directly impacting the overall duration of the injection mold and unit make process.
Mold Design Precision:
The precision of mold design is a critical factor. Molds crafted with meticulous detail enhance efficiency, while intricate designs may extend the production cycle. Striking the right balance is key to optimizing timelines.
Injection Dynamics:
The speed and pressure at which molten plastic is injected into the mold influence both the quality of the end product and the time required for molding. Optimal injection settings high pressure are essential to achieve high-quality results within reasonable timeframes.
Cooling Efficiency:
The cooling system’s effectiveness is paramount in manufacturing processes, among other factors in determining how swiftly a molten material or plastic solidifies. A well-designed and efficient cooling system accelerates production speed, contributing to timely product delivery.
Ejection Mechanism:
The efficiency of the ejection mechanism, responsible for removing the finished product from the mold, is a crucial component in the overall timeline. A streamlined ejection process ensures smooth and efficient demolding.
Typical Injection Molding Cycle Unveiled:
Mold Closure:
Initiating the cycle, the mold closes, creating a sealed cavity for the injection molded molten plastic. This marks the beginning of the first time for plastic injection and molding process.
Plastics Melting:
Solid plastic pellets undergo a transformative process, melting into a flowable molten plastic ready for injection into the mold cavity.
Precision Injection:
Molten plastic is injected into the mold cavity with precision, ensuring that the material takes the mold steel the desired shape.
Cooling:
Cooling channels and holes come into play, facilitating the solidification and cooling of the plastic. This phase is critical in achieving the desired product properties.
Mold Unveiling:
The mold opens, revealing the formed product while still attached to melted plastic. This step prepares simple mold for the subsequent ejection phase.
Ejection:
A well-orchestrated ejection mechanism propels plastic parts of the finished product out of the mold, completing the testing phase of the injection molding cycle.
Cycle Renewal:
The mold closes again, seamlessly preparing aluminum mold for prototyping phase the next injection cycle. This cyclical process allows for continuous and efficient production.
Conclusion: Mastering plastic injection molding timelines involves navigating an intricate dance of design, the material selection, mold, and process dynamics. As your partners at Sino-Mold Industrial Co., Ltd., our expertise ensures optimized timelines for your plastic products. For tailored solutions and insightful collaboration, reach out at louise@sino-mold.com.
How Fast Can Your Plastic Products Be Produced?
To truly understand the speed at which plastic products can be produced through injection molding, some real-world examples highlight the varying production lead times based on different types of products.
Example 1: Small and Simple Components
Consider small and relatively simple plastic components, such as caps or fasteners. Due to their uncomplicated designs and smaller sizes, these products often require a shorter production time. In a well-optimized injection molding process, these items may be produced at a rate of 1000 shots per hour, showcasing the efficiency of manufacturing less intricate and complex parts.
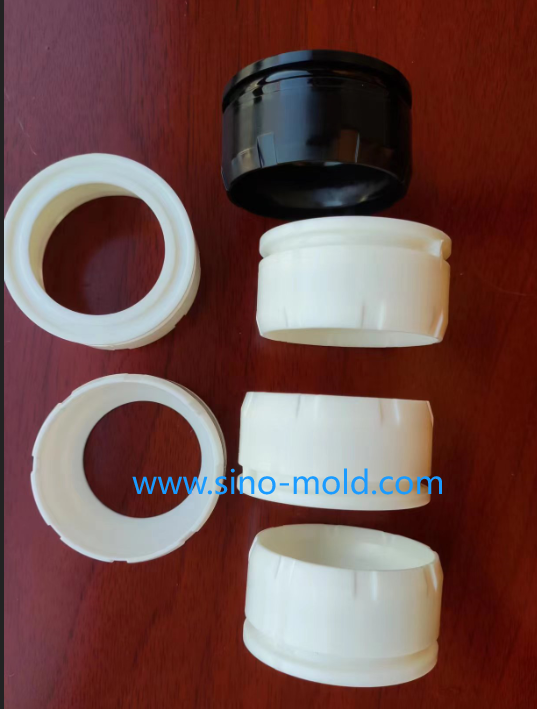
Example 2: Medium-sized Components with Moderate Complexity
Now, shift your focus to medium-sized plastic components with moderate complexity, like housings for electronic devices. These items may involve more intricate designs but are still manageable in terms of production and typical lead time. Production speeds for such components could range from 800 to 1200 shots per hour, depending on the specific design intricacies and material requirements.
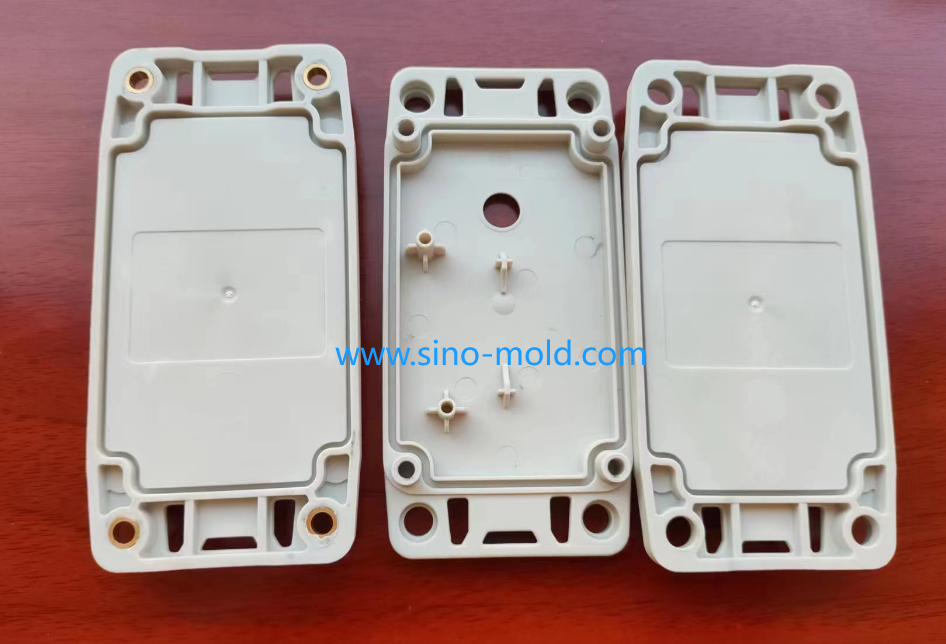
Example 3: Larger and Complex Products
Imagine larger and more complex plastic products, such as automotive parts or intricate consumer goods. The production time for these items tends to be longer due to their size and intricacy. In such cases, production speeds may vary from 500 to 800 shots per hour. The emphasis here is on meticulous molding processes to ensure the quality of the larger, more intricate parts.
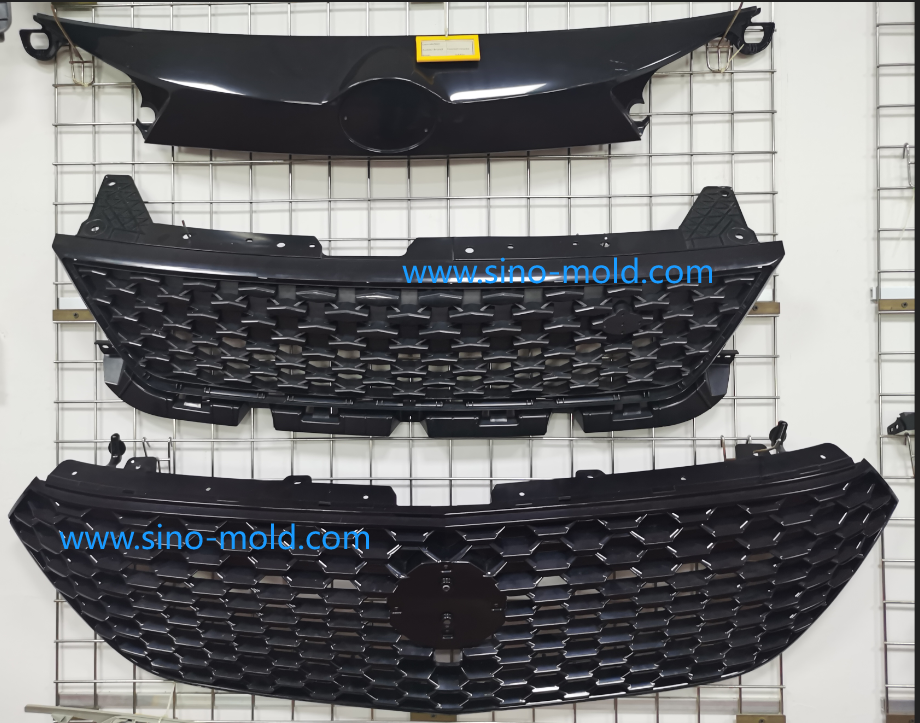
Example 4: High-precision Components
Consider high-precision plastic components, like medical devices or precision engineering parts. These items often demand careful attention to detail, leading to a slower production pace. Production speeds for high-precision components may range from 300 to 500 shots per hour, reflecting the need for precision in the injection molding process.
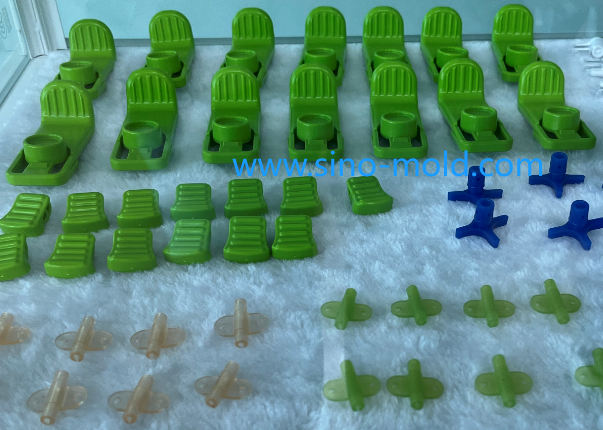
The production time for plastic products in injection molding is influenced by the specific type and complexity of the components. Small and simple parts boast faster production than other manufacturing processes, while larger and more intricate products may require a more time-intensive manufacturing process. Understanding these distinctions allows manufacturers to tailor production speed to meet the unique requirements of different product types.
How to solve cycle time in injection molding production?
Now we share success stories from various industries:
Case Study 1: Automotive Precision Parts
Challenges: An automotive manufacturer faced stringent timelines for the production of precision components. The complex shapes and high-performance standards needed careful attention when creating the mold and choosing the materials. The challenge was to meet these demands without compromising on quality.
Solutions: Sino-Mold Industrial Co., Ltd. team employed advanced mold simulation software to refine the mold design and optimize cooling channels. High-precision molds were crafted using state-of-the-art CNC machining techniques. Additionally, a collaborative effort with material suppliers led to the identification of a specialized polymer with enhanced flow properties, reducing injection and cooling times.
Outcomes: The implementation of these solutions resulted in a 20% reduction in production time. The components met the stringent quality standards, showcasing the successful integration of advanced technologies and material science in the injection molding process.
Case Study 2: Consumer Electronics Housings
Challenges: A consumer electronics company sought to expedite the production of intricate device housings without compromising on aesthetics and structural integrity. The challenge was to balance the intricacies of the design with the need for mass production within a limited timeframe.
Solutions: Utilizing multi-cavity molds, the production capacity was significantly increased, allowing for the simultaneous molding of multiple parts in each cycle. The implementation of a hot runner system reduced material waste and enhanced the overall efficiency of the injection process. Additionally, real-time monitoring systems were integrated to identify and address any deviations promptly.
Outcomes: The optimized injection molding process led to a 30% reduction in production time. The consumer electronics housings maintained a high level of the entire production process, demonstrating the effectiveness of innovative mold configurations and real-time monitoring in meeting tight timelines.
These case studies exemplify the intersection of technology, design ingenuity, and collaborative problem-solving in the injection molding realm. They showcase that, with strategic planning and the incorporation of advanced techniques, it is possible to achieve both efficiency and excellence in injection molding timelines across diverse industries.
At Sino-Mold Industrial Co., Ltd., we stand at the forefront of this transformative journey, offering cutting-edge solutions that redefine the possibilities of injection molding. Our commitment to quality, backed by advanced technologies and a dedicated team, ensures that your projects not only meet but exceed expectations. For tailored solutions, insightful collaboration, and a future where your visions become reality, reach out to us at louise@sino-mold.com.