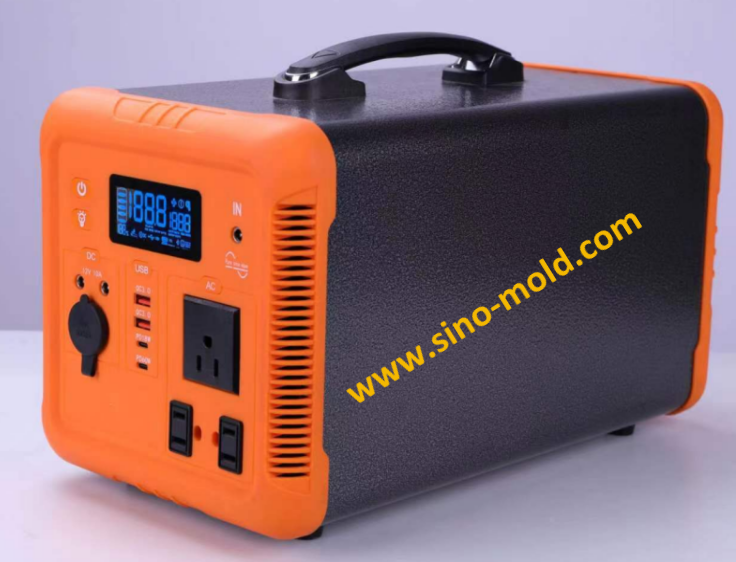
Lead In
As the demand for efficient and sustainable energy storage solutions continues to surge, manufacturers face the challenge of meeting these evolving market needs. In the pursuit of innovation, it is crucial for energy storage manufacturers to recognize the vital role of injection molding in their production processes. Injection molding has emerged as a game-changing, manufacturing process technique that offers unmatched precision, scalability, and cost-effectiveness, making it an indispensable tool in the quest for superior energy storage products.
Significance of injection molding in various industries
Injection molding is very important in many industries, including automobiles, electronics, consumer goods and medical devices. It enables efficient and precise manufacturing of complex components, resulting in cost-effective production and consistent part quality.
In automobile industry, injection molding is helpful to manufacture light and durable parts, thus improving fuel efficiency and overall performance. In the field of electronics, it allows the the mass production of high-precision complex and compact components. For consumer goods, injection molding can produce high-quality products with aesthetic appeal in large quantities.
Injection molding is now being used in the energy storage field.
It provides advantages such as design flexibility, cost effectiveness and simplified production processes. By virtue of its ability to manufacture complex and precise parts, injection molding meets the requirements of energy storage systems, including high pressure resistance and high temperature resistance.
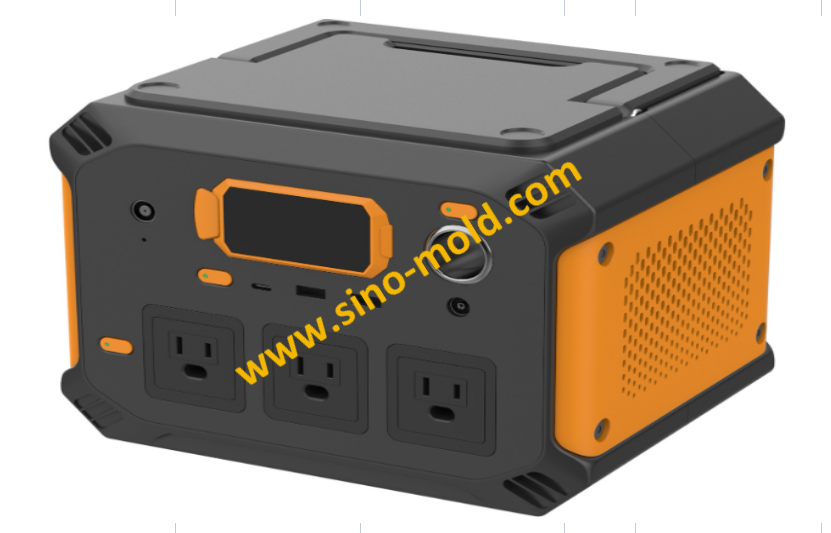
Present situation and challenges
On the other hand, more and more blackouts, long-term blackouts related to natural disasters and the imminent risk of cyber attacks all indicate the need for a thorough inspection of power infrastructure. At the same time, the original equipment manufacturers in the distribution industry are actively seeking solutions to curb the impact of the current depressed power grid:The monumental scale of modern electrical grids poses a series of formidable challenges for manufacturers of primary equipment. National power grids, comprising interconnected systems, operate semi-autonomously to ensure stable power flow and prevent disruptions. However, the inherent design complexities of these grids necessitate redundancy in both their requirements and maintenance. This, in turn, puts significant pressure on distribution equipment manufacturers to consistently supply critical components.
The benefits of Injection Molding in Energy Storage
Diverse Component Manufacturing: Injection molding technology allows for the flexible production of parts in various shapes and sizes, catering to different requirements in energy distribution systems. Whether it’s complex geometries, small components, or large structural parts, the injection molding industry provides highly customizable solutions.
High Precision and Consistency: The injection molding process enables highly accurate manufacturing of components, ensuring that the dimensions and performance of the parts in energy distribution systems meet the required specifications. This precision and consistency contribute to accurate and stable energy distribution, enhancing system reliability and efficiency.
Rapid Production and Scalability: Injection molding is an efficient large-scale production technique capable of manufacturing a high volume of parts within a short period. This is why transfer molding is crucial for meeting the production demands of energy distribution systems, particularly in situations where energy demands are rapidly increasing.

Material Selection and Optimization: Injection molding allows for the use of various materials, including high-performance engineering plastics and composites, to meet the strength, heat resistance, insulation, and chemical stability requirements of energy distribution systems. Through material selection and formulation optimization of injection molded part, the performance and reliability of energy distribution systems can be improved.
Cost-effectiveness and Sustainability: Injection molding typically offers lower production costs and high production efficiency, helping to reduce manufacturing expenses in energy distribution systems. Additionally, the use of materials in the injection molding process is relatively efficient, reducing resource consumption and waste generation, aligning injection pressure itself with principles of sustainability.
In summary, injection molding provides flexibility, precision, efficiency, and sustainability advantages in energy distribution. By harnessing this technology, energy distribution systems can obtain high-quality plastic components, enhance system performance, reliability, and sustainability, and meet the ever-increasing energy demands.
Streamlined Production Processes for Efficient Energy Storage Manufacturing
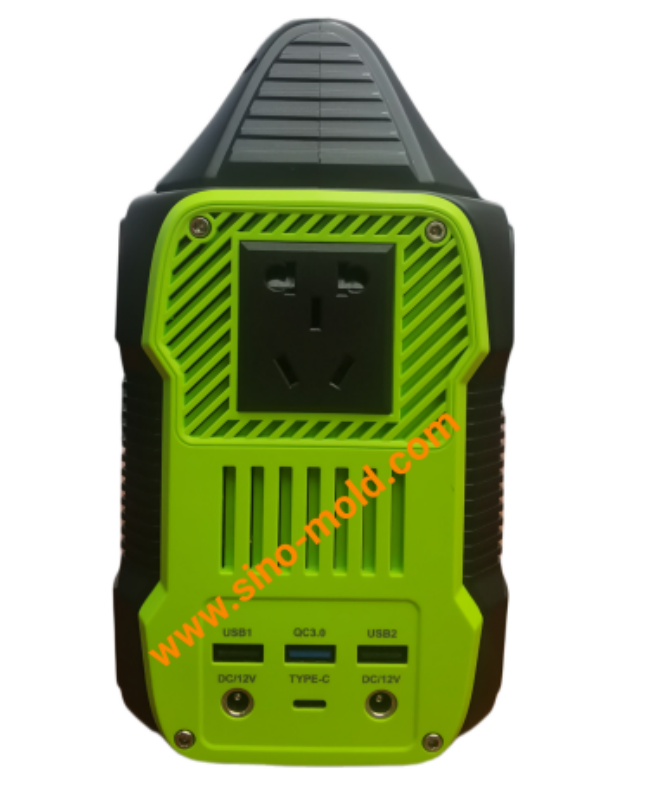
Efficiency advantages of injection molding in large-scale production
Injection molding offers significant efficiency advantages in large-scale energy storage component production. Its high-speed and high-volume capabilities enable quick and consistent production of a large number of parts. The ability to custom injection molders more complex designs in a single cycle further enhances efficiency, reducing the need for multiple manufacturing steps.
Time and cost savings through automation and rapid prototyping
Injection molding’s automated processes save time and costs in energy storage manufacturing. Computer-controlled injection molding machines can operate continuously, minimizing downtime. This automation ensures precise part production, reducing waste and manual intervention. Rapid prototyping enables quick design iterations, reducing development time and avoiding costly mistakes.
Real-world examples of streamlined production
Real-world examples demonstrate the success of streamlined production of plastic materials through injection molding. Battery casings can be lightweight, durable, and include integrated features like cooling channels and mounting brackets. This simplifies assembly and reduces manufacturing time. In capacitor manufacturing, injection molding produces intricate electrode structures for higher energy storage capacity and improved performance.

Energy Storage Manufacturers and Injection Mold Manufacturers Join Forces
Importance of partnerships
Partnerships between energy storage manufacturers and injection mold manufacturers are crucial for driving innovation. By combining their expertise, they can optimize the design and manufacturing of energy storage components. Energy storage manufacturers bring their knowledge of system requirements, while plastic injection molding manufacturers contribute their skills in materials and production processes.
Synergies and benefits of collaboration
Collaboration between energy storage manufacturers and injection mold manufacturers creates synergies that lead to innovative solutions. Injection molding machine part manufacturers provide insights into manufacturing feasibility, material selection, and process efficiency. Energy storage manufacturers share emerging trends and performance requirements. This collaboration enables the development of cost-effective and high-performance solutions.
Future Outlook: Advancements and Emerging Trends
Injection molding has a good development prospect in the field of energy storage in the future. Continued research and innovation are expected to further improve the ability and applications of plastic injection molding in this field.
The ability of injection molding to produce complex geometric shapes and customized designs from plastic material ensures the development of customized energy storage solutions for specific applications and requirements. This customization allows for improved energy efficiency, better integration into existing infrastructure and a more efficient and sustainable energy storage systems.
In addition, as the increasing demand for renewable energy and energy storage solutions, plastic injection molding process can help reduce costs and improve scalability. By simplifying the production processes and optimizing the utilization of materials, injection molding helps to reduce the manufacturing costs, making energy storage technologies easier to obtain and more affordable.
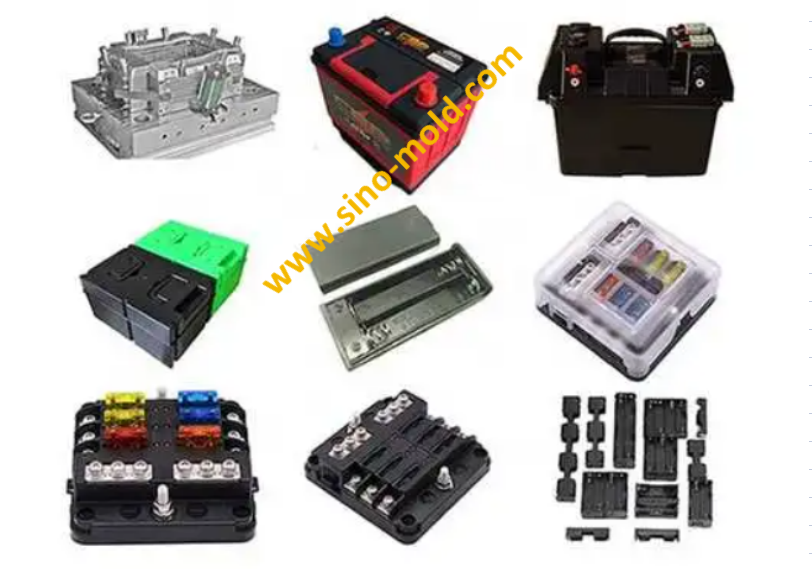
Conclusion
Injection molding plays a pivotal role in shaping a brighter future for energy storage. Its versatility, efficiency, and compatibility with diverse materials make it an invaluable tool for manufacturing energy storage components. By harnessing the benefits of injection molding, manufacturers can optimize production processes, enhance performance, and drive innovation in the energy storage industry.
At Sino Mold Industrial Co.Ltd, we are committed to supporting the energy storage industry’s growth and development. We offer comprehensive injection molding machine manufacturing and design services, as well as rapid prototyping services. Our expertise and capabilities in injection molding enable us to provide tailored solutions to meet the unique needs of energy storage manufacturers.
By embracing injection molding technology and fostering collaborative relationships, we can unlock new possibilities, drive cost-effective manufacturing, and pave the way for a brighter future in energy storage. Together, let us propel the industry forward and contribute to a sustainable and renewable energy landscape, empowering a greener tomorrow.