Introduction: Embarking on an injection molding project requires a deep understanding of the materials involved. Join(Follow) us, Sino-Mold Industrial Co., Ltd., as we unravel the complexities of injection molding materials and explore their various classifications, examples, effects, applications, and differences.

Material Classification:
Injection molding materials can be broadly classified into thermoplastics, thermosetting plastics, elastomers, and metals. Each classification flexible material offers unique properties and advantages for different applications.

Thermoplastics:
This category of plastic resin material softens when heated and solidifies upon cooling. They can be melted and reshaped multiple times without undergoing significant chemical changes. This type plastic material include plastic resin polyethylene (PE), polypropylene (PP), polystyrene (PS), and polyvinyl chloride (PVC). High-density polyethylene (HDPE) is a type of PE known for its use in manufacturing rigid, heat-resistant plastic products such as storage containers, kitchenware, refrigerator shelving, chemical-based products, pipes, geomembranes, plastic lumber, and injection molded items. Low-density polyethylene (LDPE), another form of PE, is commonly used in injection molding for laboratory equipment, containers, bottles, tanks, and ponds, and is noted for its toughness and flexibility compared to HDPE. Thermoplastics are widely used in injection molding due to their versatility, ease of processing, and recyclability.
Thermosetting Plastics:
Unlike thermoplastics, thermosetting plastics undergo irreversible chemical changes when heated, forming a rigid structure that cannot be remolded. Once cured, they exhibit excellent dimensional stability, heat resistance, and electrical insulation properties. Common examples include phenolic resins, epoxy resins, and melamine formaldehyde. Thermosetting plastics are preferred over thermoplastic materials for applications requiring high-temperature resistance and superior mechanical properties.
Elastomers:
Elastomers, also known as rubber materials, possess elastic properties, allowing them to deform under stress and return to their original shape when the stress is removed. They offer excellent flexibility, resilience, and impact absorption. Silicone rubber, natural rubber, and styrene-butadiene rubber (SBR) are some examples of elastomers used in injection molding. Elastomers find extensive applications in the mechanical and automotive parts, consumer goods, and medical industries. Additionally, thermoplastic rubber (TPR) is a blend of plastic and rubber known for its outstanding chemical and weather resistance, high impact strength, and ability to stretch and return to its original shape. TPR is used in various applications such as fluid dispensers, flexible hoses, catheters, automotive parts, wires, cable insulation, and home appliances, making it a valuable material in injection molding processes.
Metals:
While less common than plastic materials, metals can also be processed through injection molding techniques. Metal injection molding (MIM) involves mixing finely powdered metal with a used thermoplastic polymer or binder to create a feedstock, which is then injection molded and sintered to remove the binder and consolidate the metal particles. This process enables the production of complex-shaped metal components with high precision and dimensional accuracy. Common metals used in MIM include stainless steel, titanium, and tungsten alloys.
Material Properties and Selection:
As a manufacturer or designer embarking on an injection molding project, navigating through the multitude of available materials can be overwhelming. However, understanding the key properties and selection factors of these materials is paramount for making informed decisions.

1. Define Your Requirements:
Start by clearly defining the requirements of your project. Consider aspects such as mechanical strength, chemical resistance, thermal stability, and cost-effectiveness. Identify any specific material performance and criteria that your material must meet to ensure optimal functionality and longevity.
2. Prioritize Key Factors:
Next, prioritize the selection factors based on their importance to your project. Are you primarily focused on mechanical performance, or is chemical resistance a critical requirement? Understanding your priorities will streamline the selection process and guide your decision-making.
3. Assess Material Options:
With your requirements and priorities in mind, evaluate the available material options. Research the properties of different materials, considering factors such as tensile strength, flexural modulus, impact resistance, and hardness. Look for materials that align closely with your project specifications.
4. Consider Secondary Considerations:
In addition to primary selection factors, consider secondary considerations that may influence your decision. For example, if aesthetics are important, explore color options and surface finish capabilities. Ensure that the selected material complies with regulatory standards and industry requirements.
5. Seek Expert Guidance:
If you’re uncertain about which material to choose or need further clarification, don’t hesitate to seek expert guidance. Consult with material suppliers, engineers, or industry professionals who can provide valuable insights and recommendations based on their expertise.
6. Test and Iterate:
Once you’ve narrowed down your options, consider conducting material testing and prototyping to validate your selections. Evaluate the performance of different materials under simulated conditions and iterate as needed to refine your choices.
7. Make Informed Decisions:
Finally, armed with comprehensive knowledge and thorough evaluation, make informed decisions about the materials for your injection molding project. Choose the material that best meets your project requirements, aligns with your priorities, and sets the stage for success.
By following these steps and leveraging a systematic approach to injection molding material selection, you can confidently navigate the complexities of injection molding materials and choose the optimal solution for your project.
Material Effects and Processing Techniques:
Exploring the effects and processing techniques of different materials can provide insights into optimizing injection molding products and processes for better results. Factors such as melt flow behavior, shrinkage rates, warpage tendencies, and mold-filling characteristics impact the manufacturing process and final product quality. Understanding these effects allows manufacturers to adjust processing parameters and their plastic injection molding part designs accordingly.

1. Melt Flow Behavior:
The melt flow behavior of a material influences its ability to flow uniformly into the mold cavity during injection. Materials with high melt flow rates exhibit better flow characteristics, facilitating smooth filling of intricate mold features and reducing the risk of defects such as air traps or flow lines.
2. Shrinkage Rates:
Understanding the shrinkage behavior of different materials is essential for predicting dimensional changes in molded parts. Materials with higher shrinkage rates may require compensatory measures in mold design or processing parameters to achieve the desired final dimensions and minimize post-molding distortion.
3. Warpage Tendencies:
Certain materials are more prone to warpage, deformation, or distortion during cooling and solidification. Identifying materials with minimal warpage tendencies and implementing appropriate cooling strategies in the mold design can help mitigate these issues and ensure dimensional stability in the mold material and finished plastic parts themselves.
4. Mold Filling Characteristics:
Each material exhibits unique mold-filling characteristics, influenced by factors such as viscosity, shear thinning behavior, and cooling rate. By analyzing these characteristics, manufacturers can optimize injection parameters such as injection speed, pressure, and temperature to achieve uniform filling, minimize cycle times, and enhance part quality.
5. Processing Parameters Adjustment:
Based on the observed effects of materials during molding, manufacturers can fine-tune processing parameters to optimize the production process. This may involve adjusting injection speed, holding pressure, melt temperature, melting point, and cooling time to achieve optimal part quality, minimize defects, and maximize productivity.
6. Mold Design Optimization:
Furthermore, insights into material effects guide mold design optimization to accommodate specific material properties and processing requirements. Tailoring mold geometry, venting strategies, gate design, heat treatment, and cooling channel layout can enhance mold filling efficiency, reduce cycle times, and improve overall part quality.
Applications of Materials:
1. Automotive Components:
Injection molding materials play a pivotal role in automotive manufacturing, contributing to the production of interior and exterior components, common materials such as dashboard panels, door handles, bumpers, and trim pieces. Their exceptional strength, durability, and aesthetic appeal make them ideal for withstanding the demanding environments of automotive applications.
For example:Thermoplastics: Polypropylene (PP) and polyethylene (PE) are commonly used for manufacturing automotive interior components such as dashboard panels, door handles, and trim pieces due to their lightweight nature, durability, and ease of molding.


2. Electronics Casings:
In the electronics industry, injection molding materials are extensively used for manufacturing casings, housings, and enclosures for electronic devices, including smartphones, laptops, and consumer electronics. These materials offer excellent electrical insulation properties, dimensional stability, and resistance to environmental factors such as moisture and heat.
For example:Thermoplastics: ABS (Acrylonitrile Butadiene Styrene) and polycarbonate (PC) are preferred for producing casings and enclosures for electronic devices like smartphones and laptops. These materials offer excellent impact resistance, good dimensional stability, and the ability to withstand high temperatures.
Additionally, ABS plastic is utilized in creating wall socket plastic guards, leveraging its insulating properties and suitability for electrical devices, ensuring safety and durability.
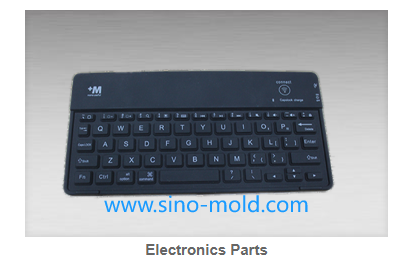
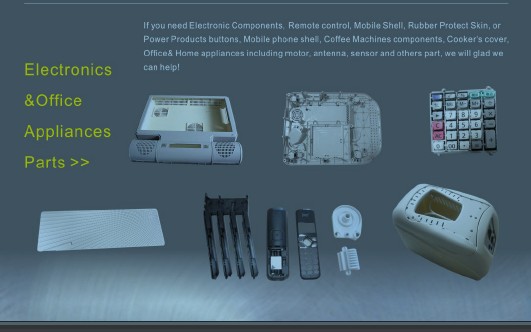
3. Medical Devices:
Injection molding materials meet stringent requirements for medical device manufacturing, delivering biocompatibility, sterilizability, and precision molding capabilities. They are employed in the production of surgical instruments, diagnostic equipment, medical implants, and disposable medical devices, ensuring safety, reliability, and regulatory compliance in healthcare applications.
For example: Thermoplastics: Medical-grade thermoplastics like polyether ether ketone (PEEK) and polycarbonate (PC) are used in the manufacturing of medical implants, surgical instruments, and diagnostic equipment due to their biocompatibility, stabilizability, and mechanical strength. Thermoplastic polyurethane (TPU) is another versatile material known for its softness, elasticity, and excellent tensile and tear strength. It is widely used in medical devices such as catheters and flexible hoses, showcasing its elasticity, transparency, and resistance properties.
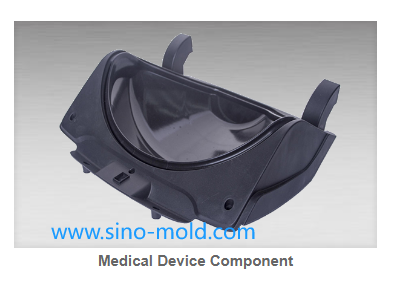
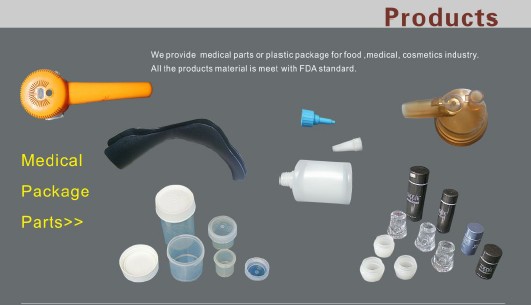
4. Consumer Products:
From household appliances and kitchenware to toys and packaging, injection molding materials contribute to a wide array of consumer products. Their versatility, design flexibility, and cost-effectiveness enable the creation of functional and aesthetically pleasing products that enhance everyday life.
For example:Thermoplastics: Polypropylene (PP) and polyethylene (PE) are widely used for producing consumer products such as household appliances, kitchenware, plastic toys,, and packaging due to their affordability, versatility, and ease of customization.
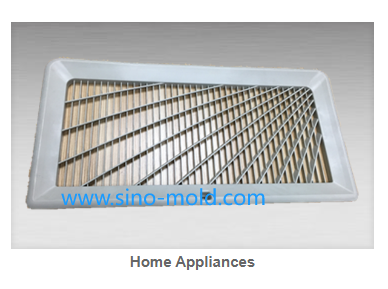
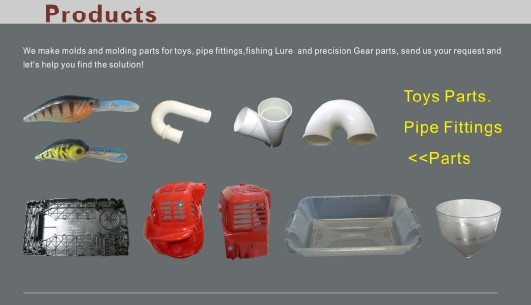
5. Industrial Components:
Injection molding materials find extensive use in industrial applications, including machinery components, tooling inserts, and industrial containers. Their superior mechanical properties, corrosion resistance, and thermal stability make them indispensable for ensuring optimal performance and longevity in industrial settings.
For example:Thermoplastics: Engineering thermoplastics like nylon (PA) and acetal (POM) find applications in industrial components such as machinery parts, tooling inserts, and industrial containers due to their high strength, high chemical resistance,, and dimensional stability.
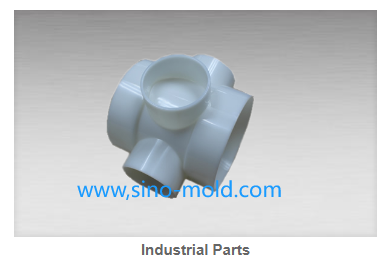
6. Aerospace and Defense:
Materials used in injection molding are also prevalent in the aerospace and defense sectors, where they are employed in high performance engineering components in aircraft interiors, avionics, missile components, and military equipment. Their lightweight characteristics, high strength-to-weight ratio, and compliance with stringent regulatory standards make them suitable for aerospace and defense applications.
For example:Thermoplastics: High-performance thermoplastics like polyetheretherketone (PEEK) and polyphenylene sulfide (PPS) are utilized in aerospace and defense applications for producing lightweight yet durable components, including aircraft interiors, avionics, missile parts, and military equipment.
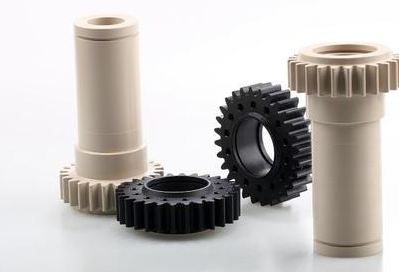
Environmental Sustainability:
Addressing the environmental implications of injection molding materials and production processes underscores the industry’s commitment to sustainability and eco-conscious manufacturing practices. Here are some key points to consider:
Biodegradable Polymers:
Introducing biodegradable polymers, derived from renewable sources such as corn starch or sugarcane, offers a greener alternative to traditional plastics. These materials break down naturally over time, reducing environmental pollution and landfill waste.
Recycled Plastics:
Utilizing recycled plastics, sourced from post-consumer or post-industrial waste, promotes circular economy principles and minimizes the consumption of virgin raw materials. Recycled plastics can maintain comparable performance and quality to virgin plastics while reducing energy consumption and greenhouse gas emissions.
Eco-Friendly Processing Techniques:
Implementing energy-efficient and resource-saving processing techniques, such as optimized injection molding parameters, reduced cycle times, and closed-loop water systems, contributes to lower environmental impact and operational costs. Additionally, the use of bio-based injection mold and release agents and environmentally friendly additives further enhances sustainability throughout the manufacturing process.
Life Cycle Assessment (LCA):
Conducting a life cycle assessment (LCA) allows manufacturers to evaluate the environmental footprint of their products from raw material extraction to end-of-life disposal. By identifying areas for improvement and implementing cost effective, eco-friendly design strategies, companies can minimize their environmental impact and enhance overall sustainability.
Regulatory Compliance and Certification:
Adhering to environmental regulations and obtaining certifications such as ISO 14001 demonstrates a commitment to environmental responsibility and ensures compliance with stringent sustainability standards. Customers increasingly value partnerships with environmentally conscious suppliers, driving demand for sustainable injection molding solutions.
Emerging Materials and Technologies:
As the injection molding industry evolves, it’s essential to stay abreast of the latest materials and technologies driving innovation and advancement. Here are some key areas of exploration:
Bio-Based Polymers:
Bio-based polymers, derived from renewable resources such as plants or algae, offer a sustainable alternative to traditional petroleum-based plastics. These materials exhibit similar properties to conventional plastics but have a lower environmental impact, contributing to a more sustainable future for injection molding.
Nanocomposites:
Nanocomposites, composed of nanoparticles dispersed within a polymer matrix, offer enhanced mechanical, thermal, and barrier properties compared to conventional materials. By incorporating nanofillers like graphene, carbon nanotubes, or clay nanoparticles, manufacturers can achieve superior performance and functionality in injection-molded products.
Additive Manufacturing (3D Printing):
Additive manufacturing, particularly 3D printing, is revolutionizing the injection molding process by enabling rapid prototyping, tooling fabrication, and low-volume production. By utilizing 3D-printed molds or directly printing end-use parts, manufacturers can reduce lead times, minimize material waste, and explore complex geometries with greater design freedom.
Smart Materials:
Smart materials, embedded with sensors, actuators, or responsive elements, introduce new functionalities and capabilities to injection-molded products. These materials can exhibit properties such as self-healing, shape memory, or conductive behavior, opening up opportunities for innovative applications in the automotive, electronics, and healthcare sectors.
Recycling and Circular Economy Solutions:
Advancements in recycling technologies and circular economy solutions are driving the development of recycled and recyclable materials for injection molding. Closed-loop recycling systems, chemical recycling processes, and material recovery innovations contribute to a more sustainable and resource-efficient supply chain.
Conclusion:
Navigating the world of injection molding materials can be daunting, but with the right knowledge, you can make informed decisions for your projects. At Sino-Mold Industrial Co., Ltd., we’re here to support you every step of the way, offering expertise and solutions tailored to your needs.
More Topic You Would Like To Know?
What are the most common plastic materials used in injection molding?
What factors should I consider when selecting an injection molding material?
What is the difference between thermoplastics and thermosetting plastics?
Are there environmentally friendly options for injection molding materials?
What are some common challenges associated with injection molding materials?
How can I ensure regulatory compliance when selecting injection molding materials?
What role does material testing play in the injection molding process?
How can I stay informed about the latest advancements in injection molding materials and technologies?
Join the Conversation:
Curious to learn more about injection molding materials or interested in exploring collaboration opportunities? Connect with me, Louise Luo, and Sino-Mold Industrial Co., Ltd. on LinkedIn to join the conversation and stay informed about the latest advancements in materials technology and manufacturing processes.
Change to :
Curious to learn more about injection molding materials or interested in exploring collaboration opportunities? Connect with our Best Editor:Louise Luo, following our LinkedIn Page and join the conversation and stay informed about the latest advancements in materials technology and manufacturing processes.
www.sino-mold.com/ www.linkedin.com/in/louise-injectionmold