Plastic injection molding is a frequent challenge in injection molding that can significantly affect the quality and functionality of the final product. It occurs when different areas of a molded part cool and shrink unevenly, leading to distortion or bending. When a shrinkage difference occurs between the top and bottom surfaces of a part, it can cause one side to shrink more, resulting in potential warpage.
Understanding the root causes of warpage is essential for anyone involved in the design and manufacturing of plastic parts.
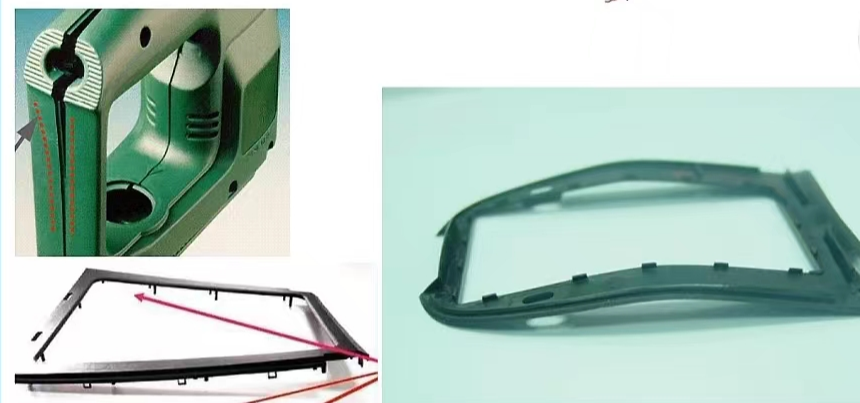
Common Forms of Warpage
Warpage can manifest in several ways, including:
Overall warpage: The entire part bends or twists in a particular direction.
Localized warpage: Only a specific area of the part warps, such as edges curling up or the center sagging.
Twisting: The part’s flat surfaces become distorted, resembling a wave.
Sink marks: Depressions or hollows form on the part’s surface.
Key Factors Contributing to Plastic Injection Molding Warpage:
1.Material Shrinkage:
During and after the injection molding process, plastic materials shrink, which plays a crucial role in why parts warp.
Shrinkage difference occurs between different areas of a part, leading to warpage as one side shrinks more than the other. This shrinkage varies depending on the type of polymer used—whether amorphous, semi-crystalline, or fiber-reinforced.
Amorphous materials, like ABS and polycarbonate, generally shrink uniformly but tend to contract more in the direction of material flow. Semi-crystalline materials, on the other hand, exhibit higher shrinkage rates, particularly perpendicular to the flow direction. Fiber-reinforced materials may reduce shrinkage due to the stabilization effect of the fibers. Fiber reinforced materials fibers help mitigate shrinkage effects during temperature variations by maintaining dimensional consistency.
2.Mold Design and Cooling Rate:
Variations in cooling rates across different regions of the part can lead to uneven shrinkage, which is a primary cause of warpage. Shrinkage difference occurs due to these variations, causing one region to shrink more than another.

Thicker areas of a part typically take longer to cool, leading to more significant shrinkage and potential distortion. Additionally, mold design, including the location of gates and cooling channels, plays a crucial role in managing cooling rates to ensure uniform shrinkage. Uneven cooling contributes to warpage and emphasizes the importance of uniform cooling to prevent defects.
3.Processing Conditions:
The conditions under which a part is molded—such as injection speed, temperature, and pressure—must be meticulously controlled. Imbalances in these conditions can create internal stresses within the part, which may lead to warpage when the part is ejected from the mold. Mold restraint, or the degree to which a part is held in place during cooling, also affects shrinkage, especially in the thickness direction.
Filler or fiber reinforcement impacts the melting and cooling characteristics of plastic materials, playing a significant role in understanding material shrinkage and subsequent warping.
4.Part Design:
The geometry of the part can significantly influence the degree of warpage. Complex shapes, varying wall thicknesses, and corners that are thicker than the nominal wall thickness can exacerbate the problem.
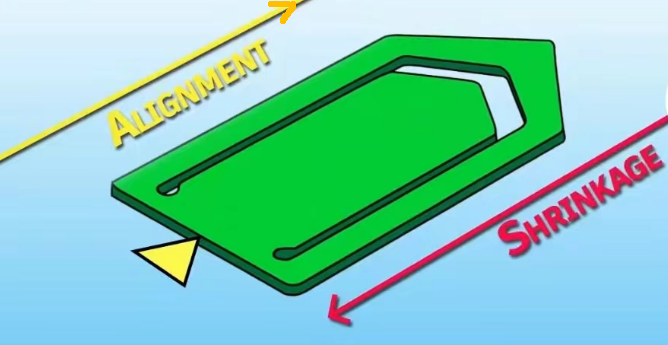
Simplifying the design and maintaining uniform wall thickness can help reduce the risk of warpage. Understanding the melting and cooling characteristics of plastics is crucial in relation to material shrinkage, as these characteristics vary depending on the type of polymer and the presence of fillers or fiber reinforcement.
5.Use of Simulation Tools:
With the assistance of advanced simulation tools like Autodesk Moldflow, engineers can visualize and predict warpage during the design phase, long before the mold is cut.
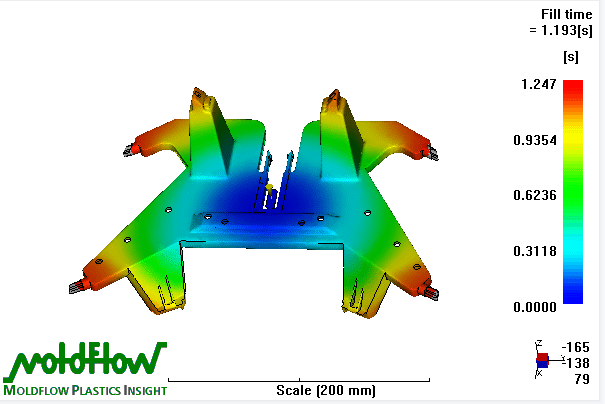
By running cooling analyses and simulating different processing conditions, engineers can identify and address potential warpage issues early, optimizing both part design and processing parameters to minimize distortion. The shrinkage difference between different sides of a part can lead to warpage, particularly in cross-section analysis, resulting in physical deformities like bowing.
Practical Strategies to Prevent Warpage: Controlling Mold Temperature
Preventing warpage in injection molding requires a holistic approach that includes:
1.Optimizing Material Selection:
Choose materials with low and uniform shrinkage rates. Selecting such materials can help prevent shrinkage difference occurs. Consider using fiber-reinforced polymers to reduce differential shrinkage, especially in complex or high-performance parts.
Understanding the melting and cooling characteristics of plastics can help mitigate warped injection molded plastic.
2.Improving Mold Design:
Ensure that the mold design includes adequate cooling channels and that these are strategically placed to promote uniform cooling. Strategic placement of cooling channels can minimize shrinkage difference occurs. Avoid drastic variations in wall thickness, and where unavoidable, use design features such as ribs to support thinner sections and reduce warpage.
Factors contributing to plastic warpage include errors related to mold design, machine errors, and inconsistent cooling rates. Optimizing mold parameters is crucial to prevent these defects.
3.Controlling Processing Parameters:
Fine-tune processing conditions such as mold temperature, injection pressure, and cooling time. Consistent processing parameters reduce the likelihood of introducing internal stresses that could lead to warpage.
Consider using a mold temperature controller to maintain consistent cooling. The phenomenon of plastic injection molding warpage is primarily caused by cooling rate, cavity pressure, and fill rate.
4.Using Simulation for Early Detection:
Leverage simulation tools during the design phase to anticipate and correct potential warpage. By adjusting the design or processing parameters based on simulation results, you can address issues before they occur, saving time and cost in the production phase.
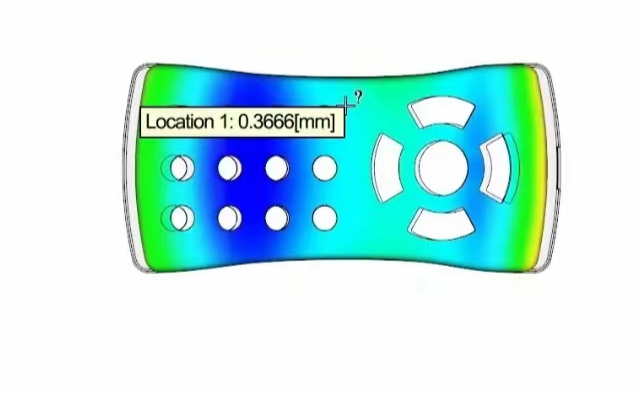
Real-World Example: How Simulation Helped Reduce Warpage in Injection Molding
At Sino-Mold Industrial Co., Ltd., we recently worked with a client facing significant warpage issues in a complex automotive component.
By applying our expertise in mold design and utilizing Autodesk Moldflow, we were able to simulate various cooling scenarios and optimize the mold design accordingly. The simulation helped identify areas where shrinkage difference occurs, leading to optimized mold design.
The introduction of fibers can mitigate polypropylene tensile bar shrinkage during temperature changes, as demonstrated by Moldflow simulations showing differences in shrinkage patterns for polypropylene tensile bars with and without glass fiber at various gate locations. The result was a 40% reduction in warpage, leading to a higher-quality, dimensionally stable product that met all the client’s specifications.
Conclusion: Why Partner with Sino-Mold Industrial Co., Ltd.
At Sino-Mold Industrial Co., Ltd., we specialize in precision mold design and injection molding solutions that directly address challenges like warpage. We also tackle issues where shrinkage difference occurs, using our expertise to analyze the cross-section of parts and mitigate potential warping. By leveraging cutting-edge simulation technologies and our extensive expertise in material selection, mold design, and processing, we ensure that every aspect of the production process—from material choice to cooling—is optimized to reduce the risk of warpage and deliver high-quality, dimensionally stable parts.
Is warpage affecting your injection molding projects? Let’s discuss how we can help you achieve better results. Feel free to reach out to us, at Sino-Mold Industrial Co., Ltd., or visit our website www.sino-mold.com to know more about our services and how we can support your next project.
More Topic You Would Like to Know?
What is the reason for warpage in injection molding?
How to prevent warpage in injection molding?
How can warpage be prevented?
How do you solve warpage problems?